Nowadays, there is a lot of buzz related to digital transformation in many industries. Shipbuilding has already used 3D CAD modeling methods for over three decades, but is that enough to prepare a shipyard for the next stage in its digital evolution?
The visualization of various structures and elements is better with 3D CAD design; however, that’s not enough for a shipbuilding project to succeed, especially for complex Defense projects. If 3D alone is not enough, what do shipbuilders need to do?
Minimizing Project Risk
The key is having the engineering team understand the design intent. I.e., identify the impact of changes upfront and create an intelligent product model that contains and maintains logical links between individual parts or larger blocks and units.
When the shipyard records all the relevant and required data and structures the processed information, it turns into an immense knowledge base that can be transferred efficiently from project to project. This approach minimizes risk and ensures projects are delivered on time.
Starting with 3D
Interestingly, it took me almost 15 years to put into words what I had intuitively understood when I started 3D modeling back in 2006. I was charmed by the concept of plotting ideas on the screen and replicating the real-life structures. In contrast, my more experienced colleagues stayed skeptical, as they didn’t see much time gains when designing 3D versus 2D.
At first, I thought they were right. Even though I didn’t need to use the time to produce three views of a structure in my head, I did use quite a bit of time to create each part, set up and structure all the details and features, make an assembly model, and produce a 2D engineering output. It felt like I had to take more steps to achieve the same result as traditional 2D CAD.
However, I also saw many errors in 2D output drawings caused by the manual input of experienced engineers or the fact that the engineering department failed to transmit the change information to all stakeholders.
I continued to advocate for 3D CAD modeling in my engineering department, slowly gaining engineering and modeling skills with the aquaculture projects at that time and studying the benefits of parametric modeling hiding beneath the surface.
3D Alone is not Enough
There’s value in running shipbuilding projects in 3D, like leveraging visualization, detecting design flaws, and getting it right – before the ship is in production. But, through my experience, I have realized that 3D alone is not enough.
Moving Beyond 3D
Indeed, the design time is usually the same in 3D as in 2D, even though many companies are proficient with 3D CAD design technologies and widely utilize them.
Suppose the shipyard, in addition to capturing 3D geometry, also lays good groundwork for establishing project workflows and capturing that in the product model. In that case, when the shipyard needs to quickly manage a change in the project, there is a large payoff. That’s where shipyards see a real gain when they take the next steps towards a digital transformation. A change should result in a natural, predictable result that can be communicated downstream.
Getting the Model to Respond Well to Change
If you ever worked on an engineering team and made changes to a detailed model you took over from a colleague, you may have felt it was easier to model it from scratch rather than make a slight design change.
For example, you needed to update the elevation of a deck and adjust all the affected structures (bulkheads, stiffeners, brackets, etc.). But if the team didn’t define and set up the design intent correctly, the change could easily break logical links and bring up numerous warnings of conflicts in the model. For example, the bulkhead structures would not intuitively update to adjust to the new height.
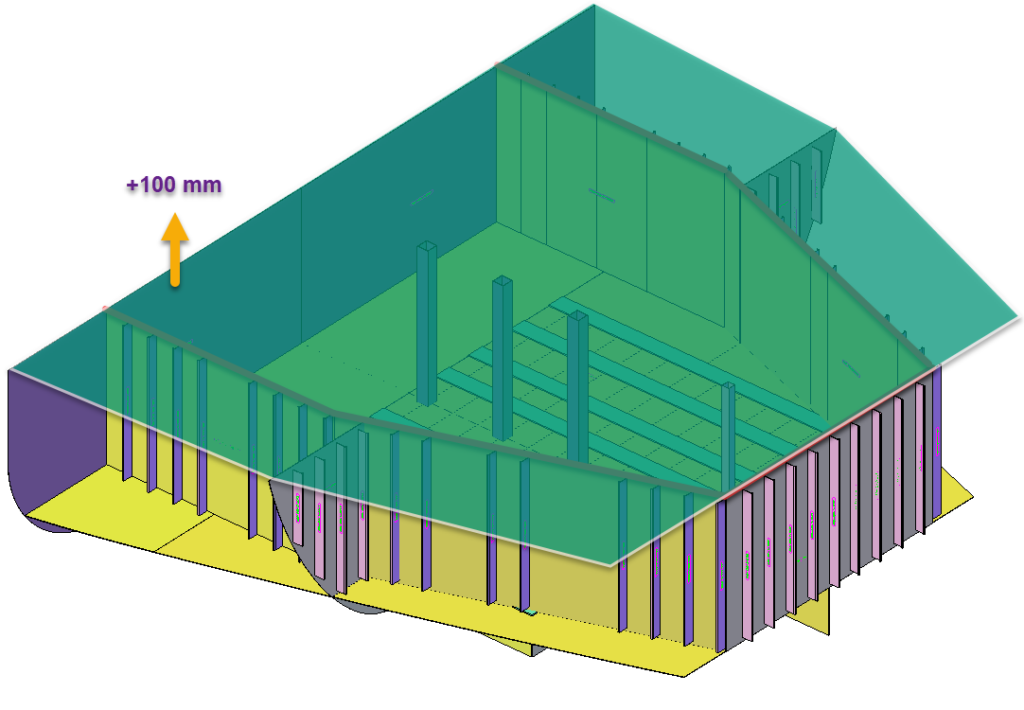
Not all engineers apply good modeling practices because they are worried about the amount of work they can perform on an individual level. They find shortcuts and skip some steps in creating a complete product model containing all required metadata. And that affects the efficiency of the whole shipyard at a later stage.
The value add when there is a mutual understanding of the principles of parametric modeling in the shipyard, and the engineers do it consistently, ensures the product model responds well to the most natural changes.
Here are just a few benefits of applying good practices of 3D modeling in shipbuilding:
- Capturing geometry gives a more visual representation of a ship. It makes it easier to share the design with the stakeholders and work more efficiently across disciplines. For example, it allows people with less technical experience to understand complex structures and provide feedback during reviews or planning activities.
- Capturing relationships between existing parts means changes are accurate and quick. Production may initiate the change due to fabrication constraints, or the owner may drive it due to changes in the international regulations. The change might apply to just this hull or for sister ships. Using relationships means that all the engineering output documentation is updated and generated automatically.
- Collecting all relevant engineering data in 3D captures and retains knowledge in the shipyard even if employees leave or retire. New people can better understand the project and the background of taken decisions and apply that in their work.
- Focusing on main design challenges instead of supporting manual operations saves time and ensures the project is delivered on time. For instance, the engineering team defines logical links in the assembly just once instead of calculating fasteners or consumables in a spreadsheet by hand for similar units and the whole project. The CAD system calculates the total number of fasteners used and populates the information in a suitable format for anyone that needs it.
- Setting up the metadata and the relationships properly in 3D creates a single source of truth. It’s easier to maintain and keep up-to-date. That also prevents errors and confusion in the project due to several hard copies in the shipyard. Any manual input is prone to error, so utilizing automation in the shipyard reduces such risks and ensures that all disciplines in the project operate with the same set of information.
Getting the Most out of Your Model
It’s important to remember that 3D CAD is a potent tool. However, to benefit from it to its full potential, the shipyard needs to develop a holistic approach. In other words, the engineering team must understand the design intent, identify upfront how a change can affect the whole project model and other departments, and then create a stable and robust project model.
Subscribe for More Shipbuilding Solutions
To be the first to see the next insights from Valentina and our Solution Specialists, make sure to subscribe.