ShipConstructor has recently completed a series of meetings with US shipbuilders and design firms regarding methods for enhancing Design for Production (DFP).
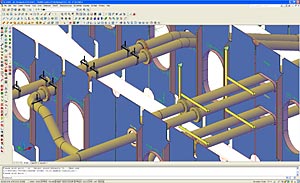
Rule-based distributed systems supports (shown in yellow) are a practical application of DFP.
“ShipConstructor’s software is widely used at US shipyards so it was natural for our industry group to collaborate with them,” says Don Sauvage of Northrop Grumman.
ShipConstructor has recently completed a series of meetings with US shipbuilders and design firms regarding methods for enhancing Design for Production (DFP).
These meetings have been part of a project funded by the National Shipbuilding Research Program (NSRP) involving Northrop Grumman (Avondale & Pascagoula), Bollinger Shipyards, Marinette Marine, VT Halter Marine, as well as Genoa Design.
The goal of DFP is to optimize design for efficient production so the team members identified two software functionalities as practical applications.
The first was the use of standard assemblies during the 3D modeling process. This would involve the creation of standard components that followed DFP principles. These components could then be reused anywhere within the model to ensure consistency.
The second functionality was a rule-based program for the creation of distributed systems supports. To optimize DFP, the supports for a ship’s pipes and HVAC components (distributed systems) need to be designed in a specific way depending on the system’s location, configuration and materials used. This is a complex task so a rule-based program would be of assistance.
Industry representatives have collaborated with ShipConstructor in the development of both identified functionalities which will be included in the upcoming ShipConstructor® 2008 R5 software release.
To download high resolution versions of the images in this press release please visit:
http://downloads.shipconstructor.com/press_release_images or click here to download them directly