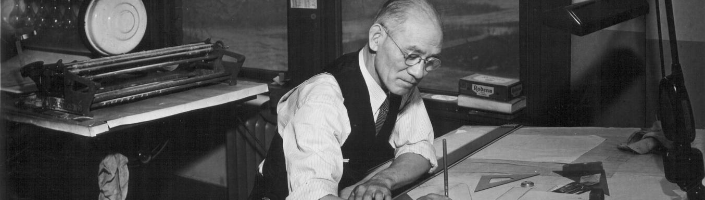
For the last few posts (What is the Biggest Challenge in Shipbuilding? and Shipbuilding’s Biggest Challenge: Stakeholders’ Perspective?) we have been discussing one of shipbuilding’s biggest challenges. The source of the challenge begins because of the lack of concentration / focus / understanding regarding including the 3D model in any of the yard’s deliverables to their client. However, even though most shipbuilding projects do not have any 3D digital model requirements in any of their deliverables, there are shipyards that have seen significant benefits by taking a more modern approach and including these items.
Many of my thoughts throughout this blog post series were formulated from discussions with several companies that already have implemented an approach which emphasizes the value of the 3D virtual model. These yards have adapted to the new digital era and have included the 3D digital model of the ship in most of the milestones to their client.
I will not be able to share the companies’ names for obvious reasons; however, the shipbuilding industry is pretty small so I am sure you will be able to find a nearby yard that is practicing this approach.
Some of the Benefits Mentioned
The companies I have talked to mentioned several benefits:
- Better designed ship: With a more complete digital model they were able to work with the owner very early on and throughout the delivery/construction of the project. There are always changes required by the owners for several reasons but by having early virtual model reviews they were able to catch some significant issues and adjust the model to accommodate the changes. When the finally documentation went to production they still had some production issues but the scale of the issues was significantly smaller than on previous projects. Construction with pre-outfitting was also optimized, resulting in a better crafted ship.
- Cost effective: There were three main reasons why they saved time and money:
- Changes from the client were mostly done early in the design phase which is much cheaper.
- There was less time recreating production documentation which therefore allowed for better quality output to the production floor. This resulted in less mistakes, communication issues and rework in production.
- The third reason for reduced costs (which the two above fostered) was the reduction of late changes to the project schedule. This allowed the project schedule to be executed without much disruption, maximizing the usage of the production facility.
- Build ships faster: It was mentioned several times for the reasons discussed above (less errors, less changes, better planning, etc.) that the shipyards were able to build the ship faster or at least with the same final deliverable date with a higher level of quality.
Types of Companies
I did start to see a trend regarding the type of yards and even clients who started to include a 3D model as part of their delivery schedule. Here are some loosely defined categories:
Working on Navy & Coast Guard Projects
Many government projects are looking at the new and better ways to design and construct ships. Some of them are following a more 3D model centric delivery schedule appended to their previous traditional milestone structure. This has caused the companies working on these projects to change their internal processes and culture in order to achieve the added 3D model requirements.
Companies which are the Builders and Owners
Companies that are both builders and owners of a vessel are also adopting this strategy. This is an interesting situation and the one that actually caused me to start thinking the shipbuilding industry could adapt to a new milestone structure. I am completely aware that this situation has a whole different financial structure but what I found interesting is that when a company is invested in both the final deliverable (ship) and the construction, they look at optimizing the entire process. These companies have proven that having a more complete design is better overall for the organization. It is cheaper, reduces delivery time, reduces man hours required, reduces costly reworks and improves quality of the final deliverable in craftsmanship and ship performance.
Using 3D for Basic Design
Other companies I have seen that have introduced a 3D digital model to their milestones started off because they were using a 3D model for their basic design. They still generated the same traditional 2D packages but these drawings were generated from their 3D digital model. They then used this 3D model to discuss various aspects of the ship with the owner (or their representative) and immediately got buy-in from the client. This was interesting because they started to use the 3D model to improve their internal processes but in turn also helped communicate and collaborate with the owner early on.
Innovative Yards with good Partners and Clients
Last but not least, there are many yards which do not fit into the above loosely defined categories but have found a way to evolve the traditional milestones. This is usually with the help of some very well selected design partners and clients who are willing to try something new, mostly because of the trust that has been built throughout the years.
Closing Remarks
This is the final post of the series but I do plan on writing on this subject in the future.
I stated this post series talking about the need to incorporate a 3D model right from the first milestone but I do not think nor suggest a fully complete and detailed model is required before the first equipment is ordered or material is cut.
The strategy I am suggesting instead is that we would add a milestone at the beginning of the project which would be a 3D digital model containing the information we need to reduce or eliminate the amount of changes downstream. We would still keep the current physical milestones but include or add additional milestones which continue to refine the 3D digital model by adding more details as the project progresses.
There are many yards and clients that have changed their business to work in this more digital friendly strategy. My prediction is that we will see this strategy used more and more in our industry. One thing I mentioned but did not emphasize as much as I should have is the importance of changing internal workflows, tools and even culture. I guess I will write a post on that topic in the future.