Challenges
- Improving design efficiency
- Build standardization and minimizing production time
- Bill of Materials (BOM) for procurement, planning, quoting
- Minimizing handling and module movement
- Eliminating service clashes
Solutions
- Reducing time to cut parts
- Introducing automated nesting
- Aligning design deliverables with build methodology
- Material tracking and usage across production
- 3D visualization and fly-through
Products Used
Incat, a leading design house and shipyard, is known for pushing the boundaries of innovation in the shipbuilding industry. The company’s latest project, Incat Hull 096, the world’s largest battery electric ferry, demonstrates their commitment to cutting-edge technology and sustainable vessels. This 130-meter-long vessel will accommodate 2100 passengers and over 220 vehicles, powered solely by battery electric propulsion. In addition, Incat is using zero-emissions energy to operate the shipyard and build the vessel.
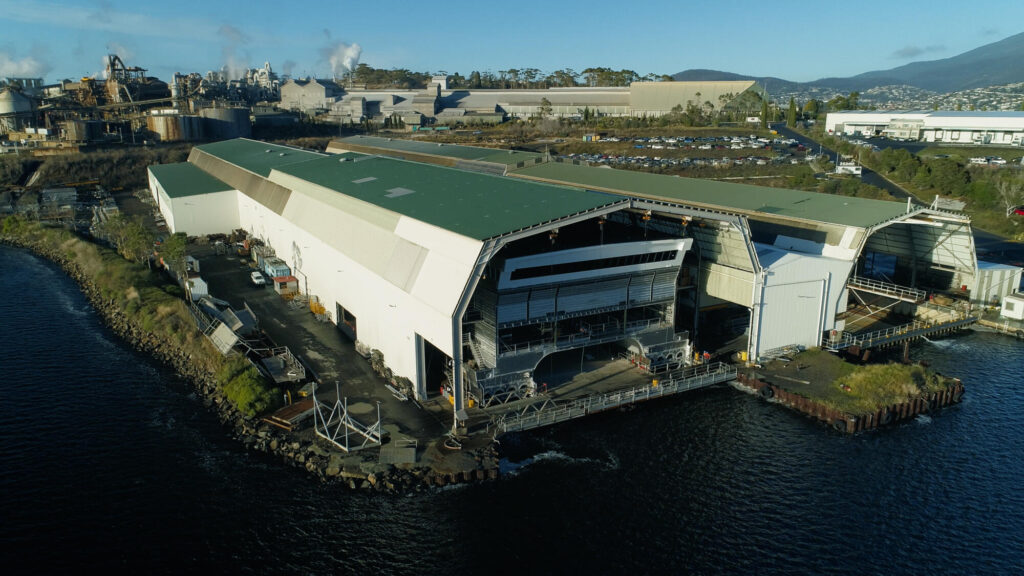
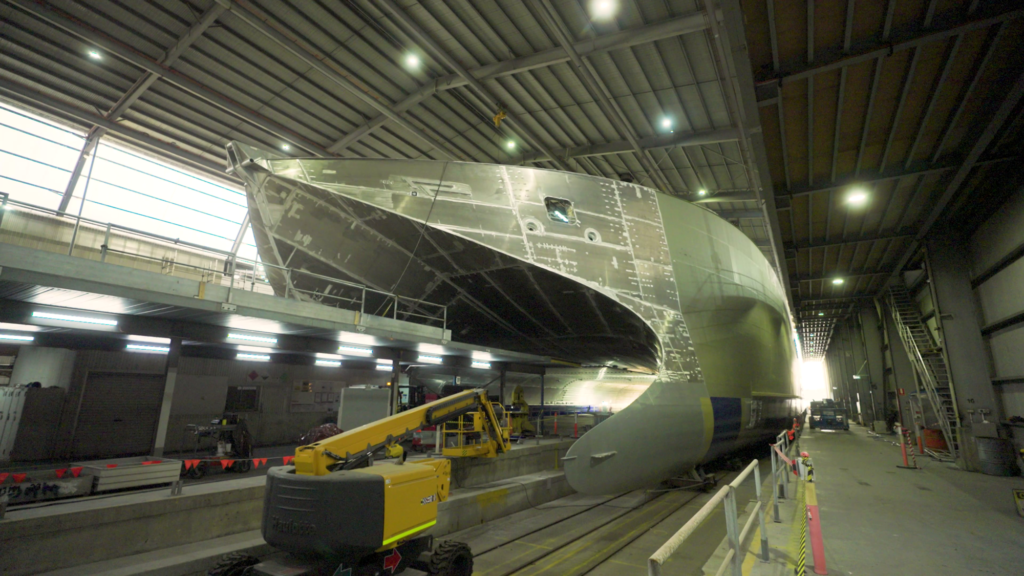
Challenge
As Incat embarked on this ambitious project, they faced the challenge of modernizing their business processes to enhance efficiency and data management. The shipyard’s existing systems were robust but needed to evolve to support the new demands of digitalization and data tracking across various departments. The goal was to eliminate siloed information, reduce double handling of work, and maintain continuous production without disruption.
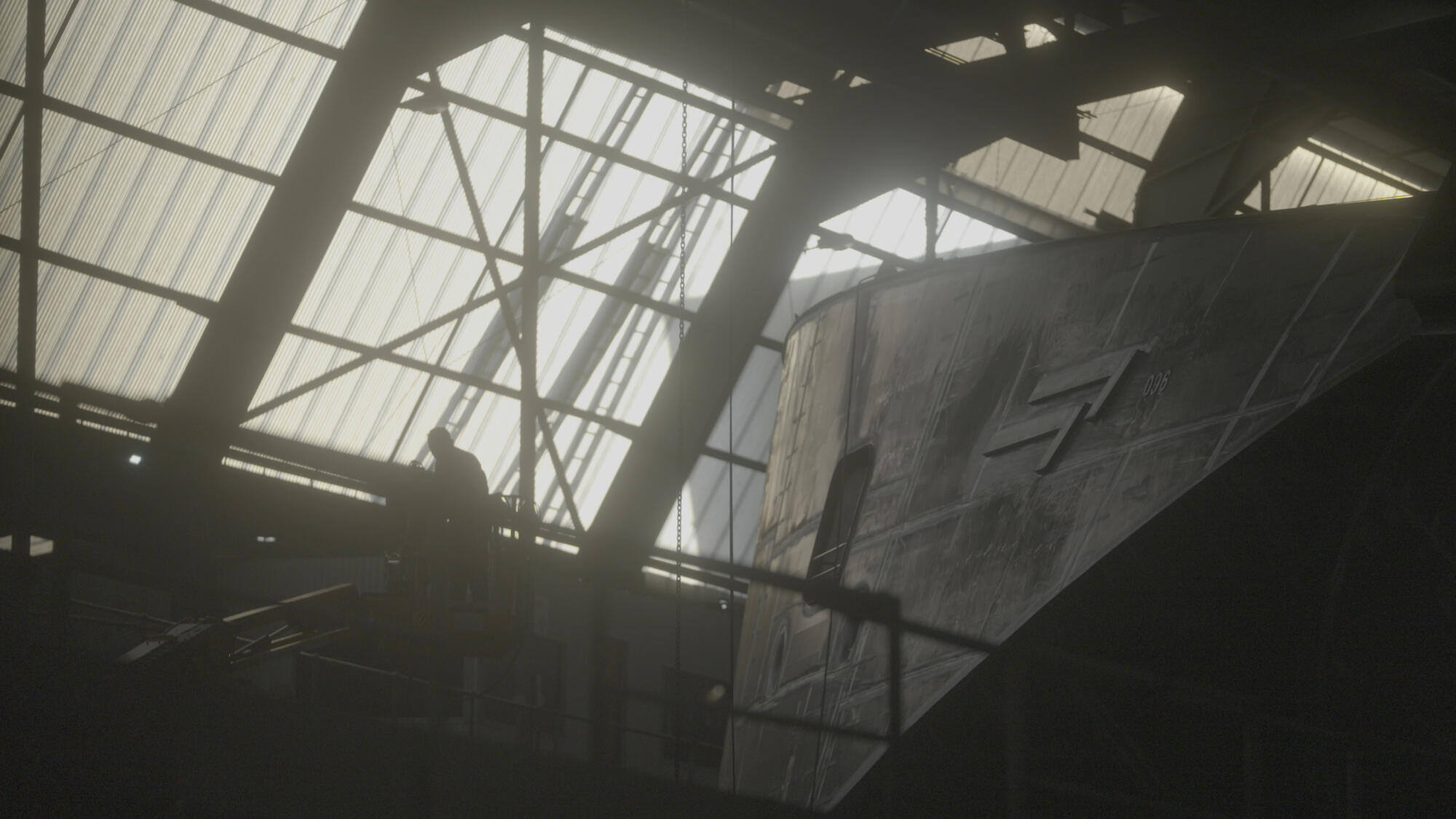
“At Incat, we don’t have the luxury of stopping production. Our prime focus is continuing production and we needed to be very wary of how we did that to not lose any of the proven processes we have in place.”
Stewart Wells, Technical Manager, Incat
The additional challenge for Incat and their in-house design office, Revolution Design, was going to be switching a key part of their design and engineering technology part-way through this large and complex project. Doing so, without interrupting ongoing production or disrupting the project schedule, added an additional layer of risk that had to be addressed.
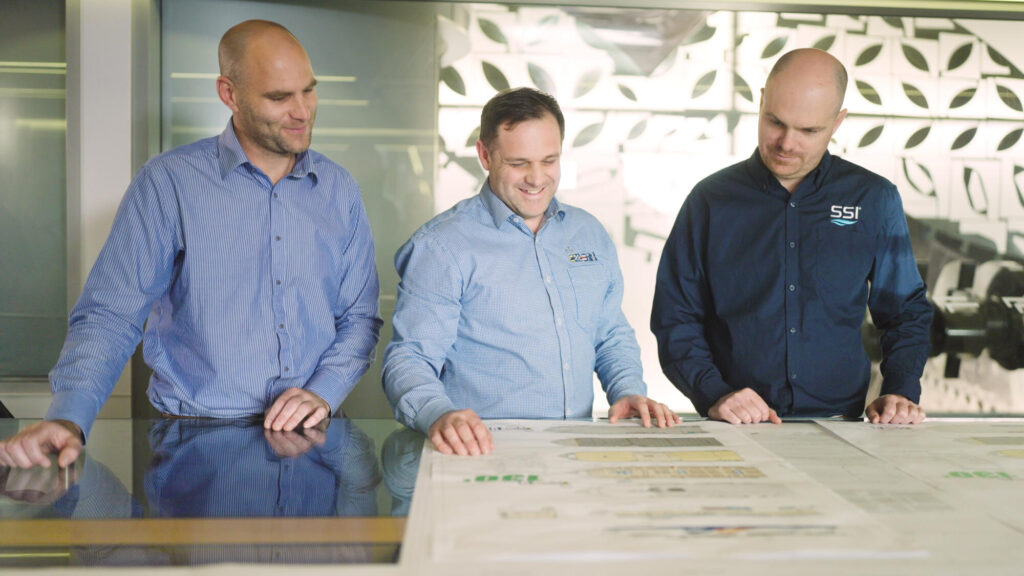
Partnering with SSI
To address these challenges, Incat partnered with SSI, a company known for its expertise in providing comprehensive shipbuilding software solutions. The initial focus was on improving production documentation. SSI ShipConstructor enabled Incat to leverage detailed data and product information, enhancing the design process and increasing efficiency.
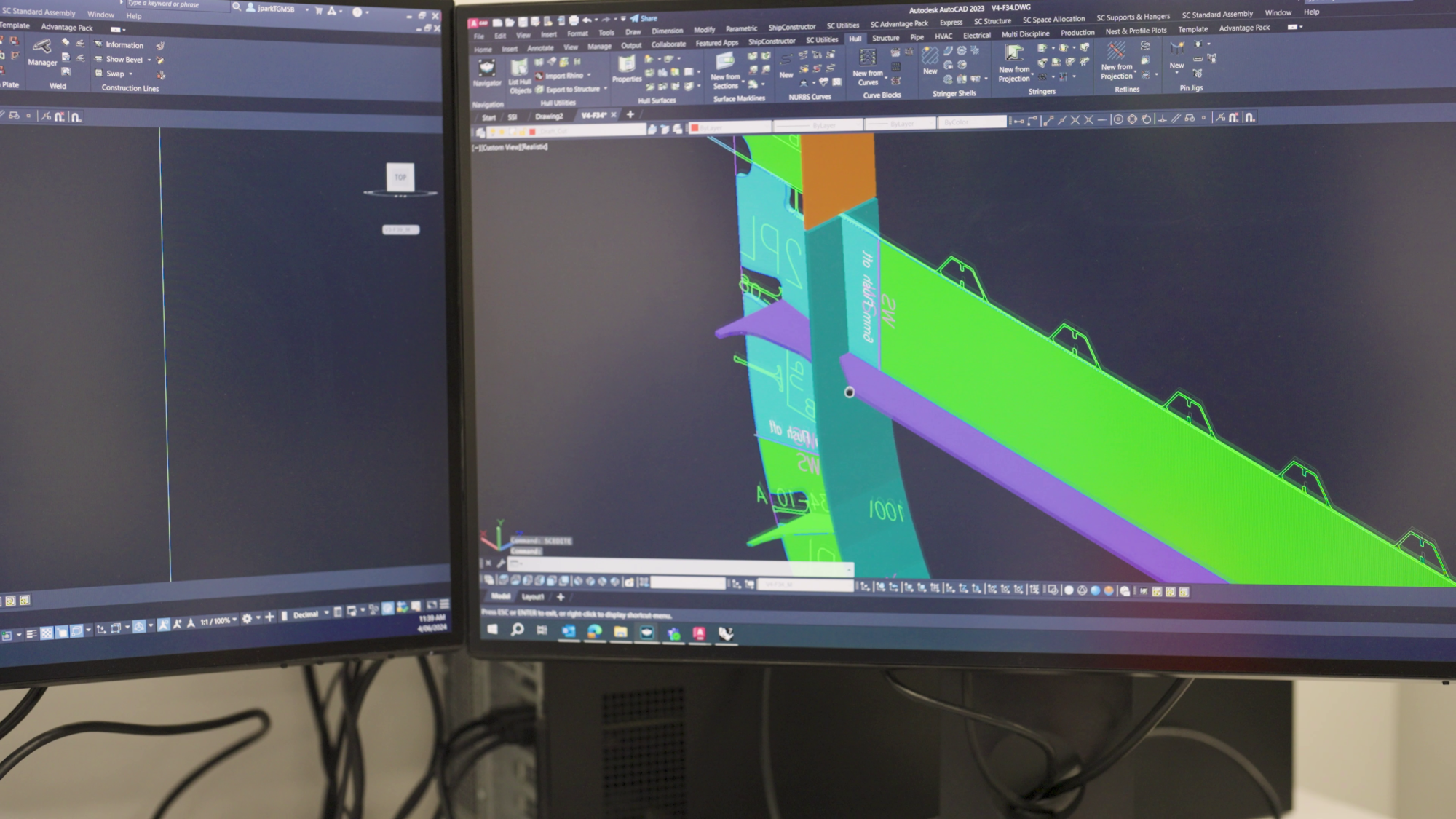
“We’re looking to move the business into a new realm in terms of digitalization and data tracking across the business. Part of that is working with SSI to really understand how we can utilize that through the business.”
Stewart Wells, Technical Manager, Incat
A key component of the solution was the implementation of a digital twin, which allowed Incat to access and utilize information across different areas of the business. This comprehensive digital approach allowed for increased build standardization, quicker and more efficient ways of delivering information to the plate shop, more efficient fabrication and assembly on the shop floor, and project information that is more accessible to downstream users in the organization.
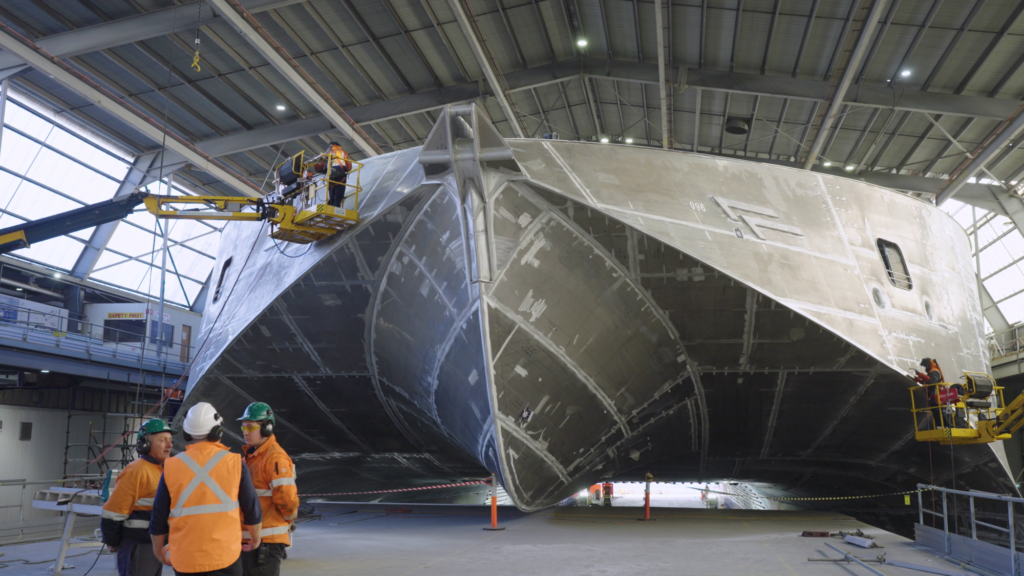
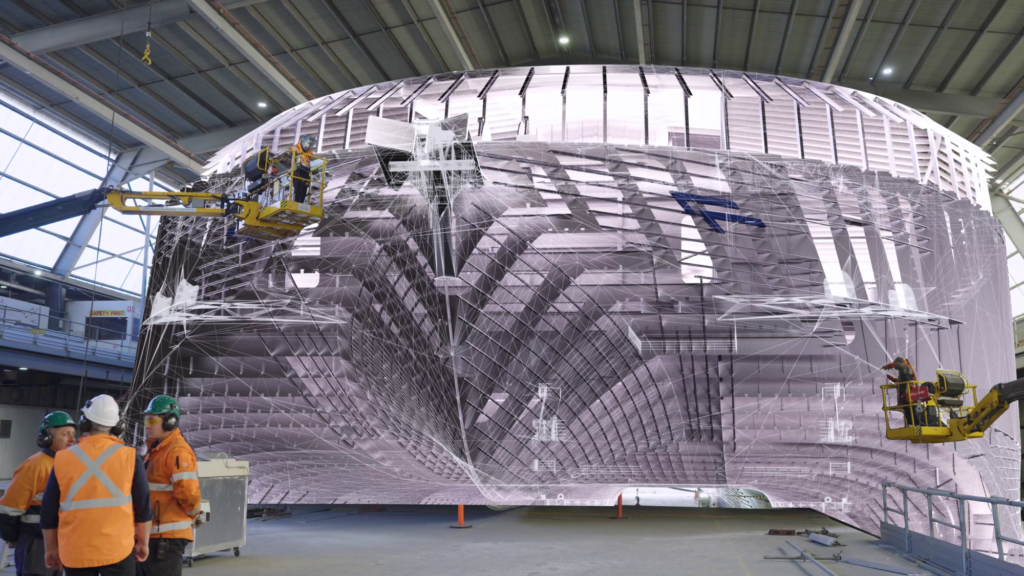
Implementation without disruption
The implementation process required careful planning to avoid disrupting ongoing production. SSI worked closely with Incat, providing dedicated support to identify the best workflows and processes to integrate into the existing way of doing work.
“With SSI, we always knew that we were partnering with a group that was not going to just provide us with a set of software,” said Jason McVicar, Head of Design at Incat. We knew that we were going to have a dedicated person to help us through that process of looking at our workflows and identifying the best workflows and processes to implement in their tools that also complement the way that we work.”
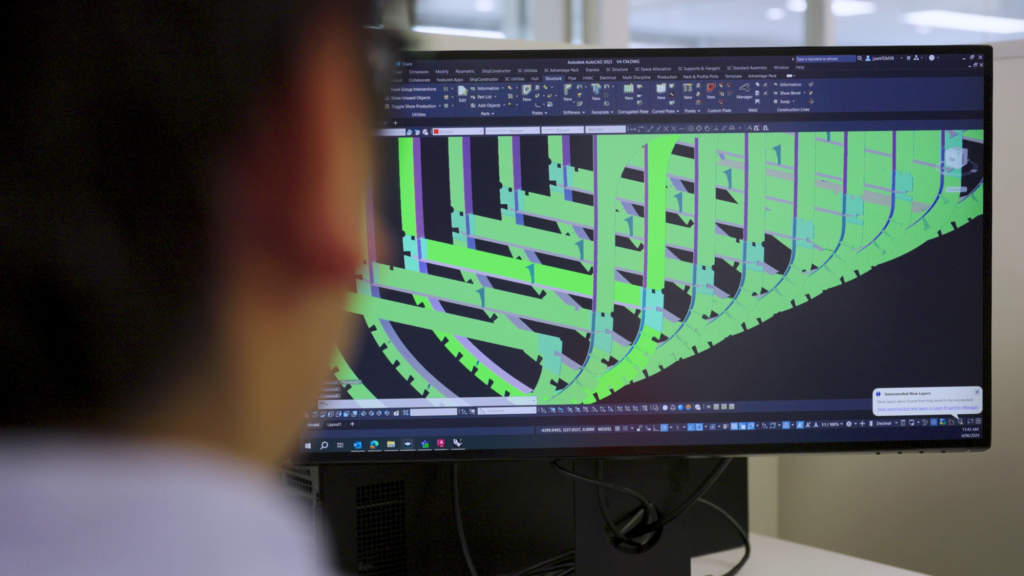
SSI’s ongoing support included implementation training and consulting, ensuring that Incat could effectively utilize the new systems. This collaborative approach allowed Incat to continue production without any adverse impact to the schedule, even while taking advantage of the new capabilities available to the team.
Outcomes
The partnership with SSI brought significant benefits to Incat. The shipyard experienced enhanced efficiency in the design process, with detailed designs reaching production faster than before. The automation of processes through ShipConstructor led to quicker output and the ability to cut plate sooner, keeping projects on schedule.
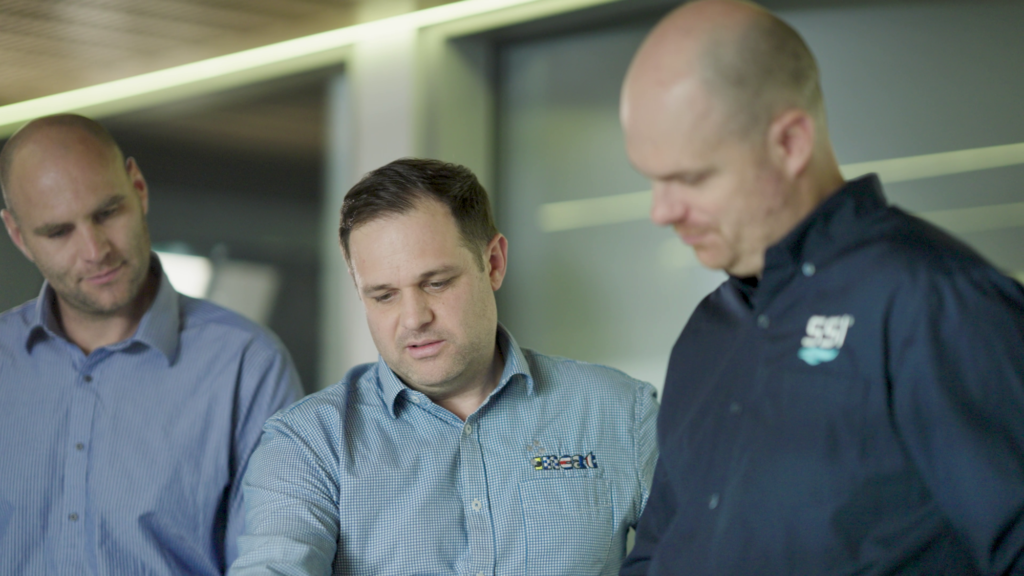
The pace of implementation was critical to Incat’s success. The company managed to modernize its operations without halting production, demonstrating the effectiveness of the collaborative approach. The expertise and support from SSI were instrumental in achieving these positive outcomes, ensuring that Incat could maintain its position at the forefront of shipbuilding innovation.
“We haven’t stopped production,” said Stewart Wells. “We’ve had a project running this whole time and there’s been no impact. In fact, we’re seeing benefits.”
Facilitating build standardization and adding automation
Capturing the build strategy digitally has made it easier to drive production deliverables and introduced more build standardization into their process. Doing so has aligned the design and production teams more closely than before.
In the past, with deliverables that were generated across multiple different platforms for assemblies, class drawings, construction drawings, and nest arrangements, there was more double handling that was required. Drawings would often require modification downstream, and changes needed to be made across three sources of information.
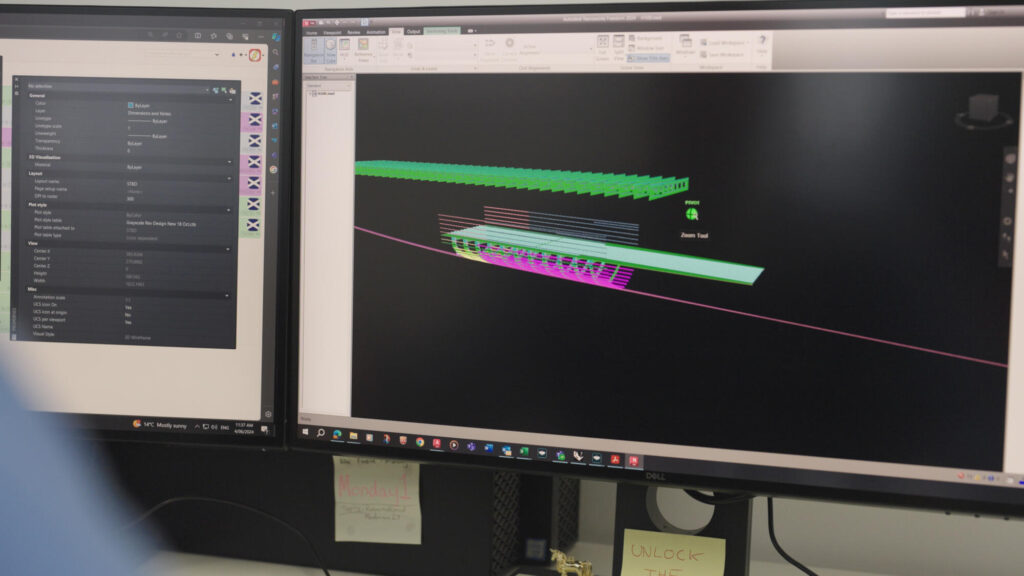
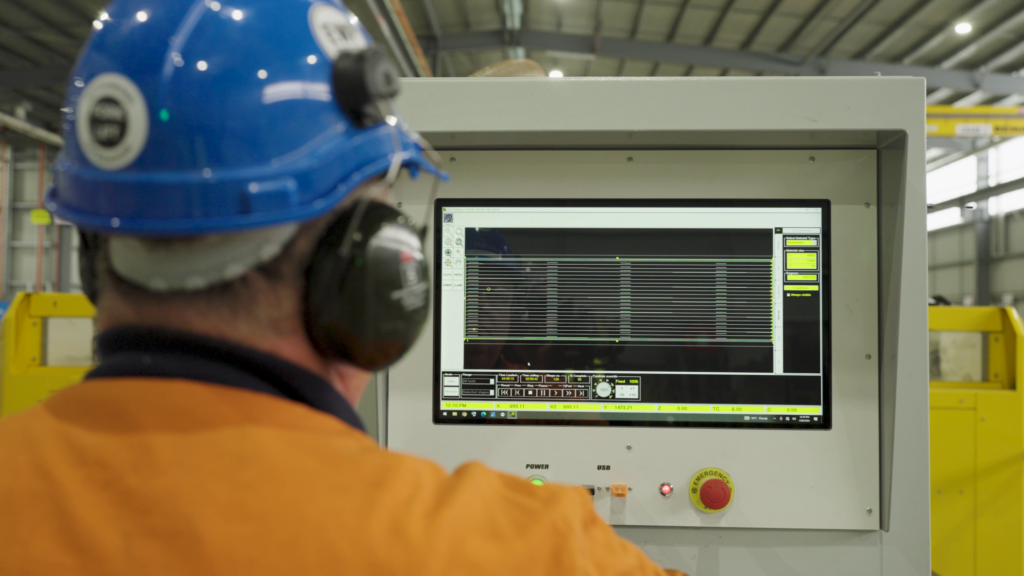
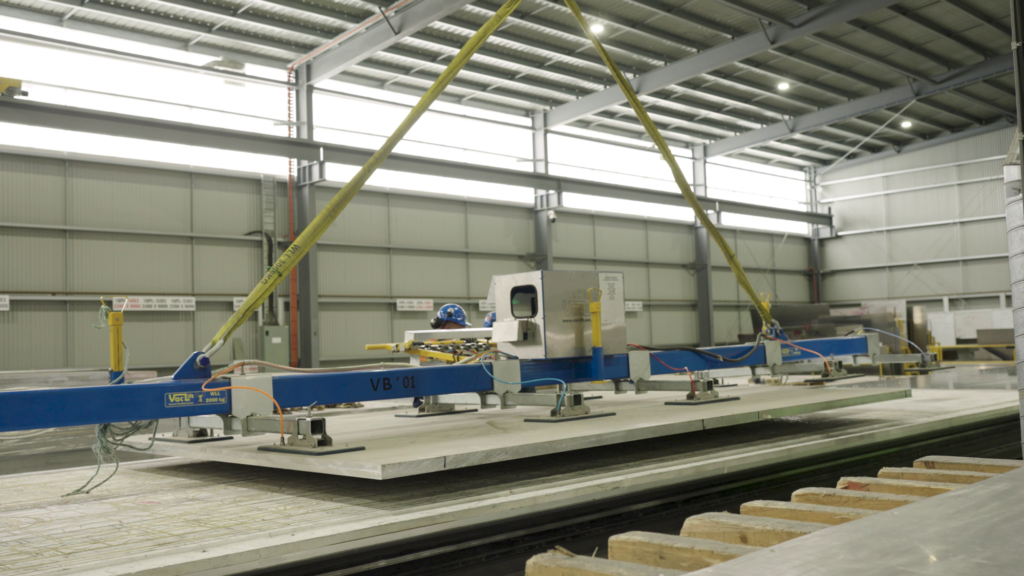
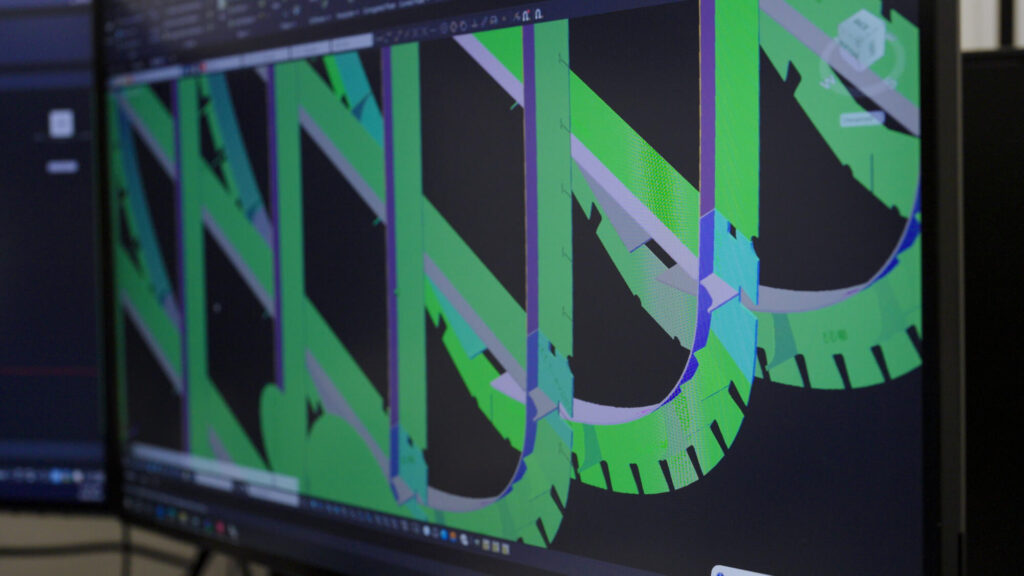
SSI worked with Incat to eliminate the double handling of work and utilize the common ShipConstructor product model as the single source of information to feed the design and build process. Automating the creation of deliverables and the transfer of information minimizes the chance of errors and speeds up information sharing. Downstream, stakeholders can generate automated reports directly from the information in the product model to understand and track progress on the project.
The end result is improved material tracking, build standardization, increased efficiency through automation, and faster cycles from design to cut parts.
Building toward a synchronized shipyard
The partnership between Incat and SSI highlights the importance of leveraging digital shipbuilding solutions and the expertise of shipbuilding technology experts. The Incat team’s innovation-focused mindset embraces digitalization and improving data management, driving it to set a new standard for efficiency and innovation. The successful implementation of SSI ShipConstructor software and the ongoing collaboration have positioned Incat to continue leading in the development of sustainable and technologically advanced vessels.
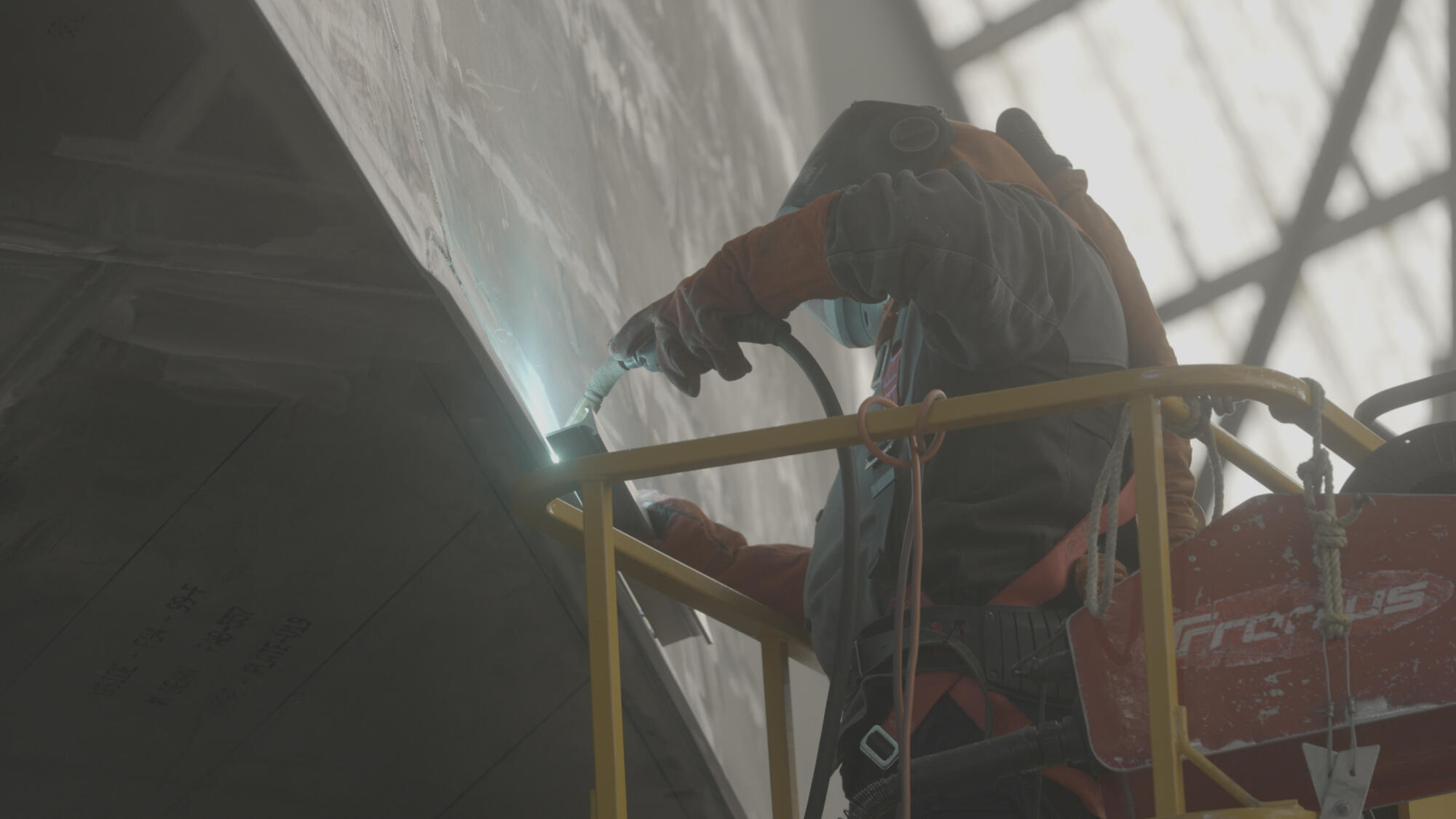
“With change, it’s always good to have the right minds around the table, and certainly the expertise at SSI was critical to making that process go well.”
Jason McVicar, Head of Design, Incat
About Incat
Australian shipbuilder Incat is renowned for construction of highspeed lightweight catamarans. Sitting at the cutting edge of environmentally friendly craft, Incat provide optimal lightweight ship solutions for ferry operators, special service providers and militaries. From fast, flexible and efficient vehicle-passenger ferries to high-speed military support vessels, crew ships and dynamic platforms, Incat sets the global benchmark in aluminium ship technology.
With the continuing emphasis on eco operations and fuel efficiency Incat has continued to develop the breed with lightweight, environmentally friendly fuel-efficient ships carrying heavier vehicle loads than ever before and at the lowest operational costs.
Incat’s shipyard is on Prince of Wales Bay at Derwent Park near Hobart, Tasmania, Australia. The facility incorporates more than 70,000 m2 of undercover production halls, with two dry-dock areas capable of accommodating up to six vessels under construction.