Introduction
Information is at the heart of the digital shipyard, but ensuring that information is available across your organization is a challenge. Throughout this playbook, you’ll find actionable strategies and best practices for your shipyard when it comes to getting information to the waterfront.
You’ll find strategies to:
Chapter 1
Understanding Your Shipyard’s Information
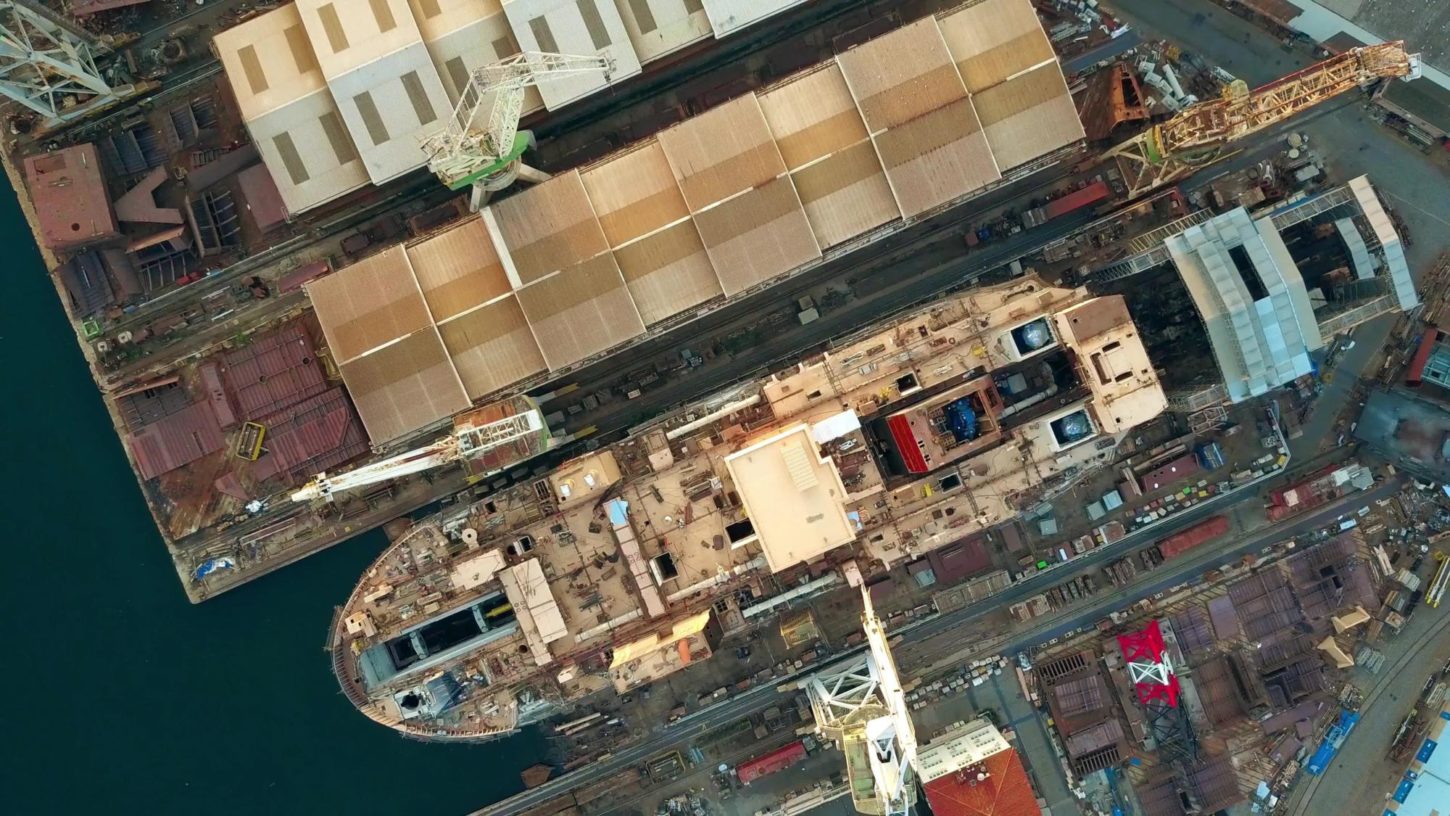
Today’s innovations require digital data to be available in a usable form to feed other platforms, departments, and organizations. However, not all digital data is the same. The needs of each digital technology that’s part of our digital transformation are different and require different digital data to fuel them.
Digital data is foundationally crucial for business success and forces many organizations to find better ways to handle their digital information. Unfortunately, digital information is often abundant but disparate, and it is a challenge to relate digital information across platforms – making it unusable.
Organizations are looking for new technologies that ensure legacy digital data and information is usable while also providing an open architecture for current and future business needs. However, new technologies can only take shipbuilders so far – there needs to be a cultural shift in how we perceive and consume digital data.
Shipbuilding leaders can get the most out of their digital assets by:
- Identifying the difference between data and information.
- Prioritizing areas for future investment.
- Taking steps towards increased data governance.
Data is a company asset
Any shipbuilding organization will benefit from a firmer grasp of the data it creates, consumes from other partners/suppliers, or changes.
A company mindset and culture that thinks of data as an asset rather than a byproduct will produce a team that understands how data quality and accessibility will add long-term value. When treated as an asset, temporary fixes, spreadsheets, and workarounds aren’t viable data management solutions. Thinking of digital data as an asset will encourage companies to think of other ways to leverage existing data in their ecosystem. Treating data as an asset changes behaviors on creating, consuming, and distributing data in the digital age.
Data vs. information
Data and information are often interchangeable terms, and most of the time, it isn’t problematic to think this way. However, the distinction is crucial for better understanding each system’s role, process, and platform within your shipyard.
Data is like raw crude oil, and it’s what is directly produced by your software. Without manipulation, it’s difficult or impossible to get any value from it (think: the mass and position of every individual part within your model).
Information is a refined product. It can be used directly for decision-making and is the true source of value for your organization. The manipulation of raw data into information can happen behind the scenes within a platform, through connection with another platform, or manually.
Who owns the information?
It is essential for shipbuilding organizations to:
- Have clearly defined data management responsibilities that mitigate data siloes.
- Have a consistent source of truth.
- Use data and information governance frameworks (how data and information are managed, controlled, and shared).
Organizational culture must shift away from the notion of individuals and teams as data owners with information specific to individuals and their departments. Instead, they need to move towards a culture where everyone acts as data stewards in a larger ecosystem of information. This shift promotes holistic information creation by keeping the bigger picture and collaboration top of mind. Even without a formal framework, shifting the cultural perception of data and information can play a part in maintaining a single source of truth.
Information architecture investment
Shipyards are investing massive amounts into innovation. Technologies like VR/AR, additive manufacturing, connectivity, and robotics – to name a few. But while these innovations solve specific challenges, they can create new data points that aren’t taken full advantage of. Turning that data into information that every department can use is the missing link for many shipyards—connecting disparate information into a single source of truth that every team can reference.
Maintaining a single source of truth through a tightly integrated and shipbuilding-specific PLM solution has emerged as the best way to complement existing MRP, ERP, and CAD platforms and get the most value out of innovation. Out of those that completed our shipbuilding innovation assessment, 55% indicated their organizations have budgeted for improvements to PDM, PLM, ERM, or MRP platforms within the next 12-18 months.
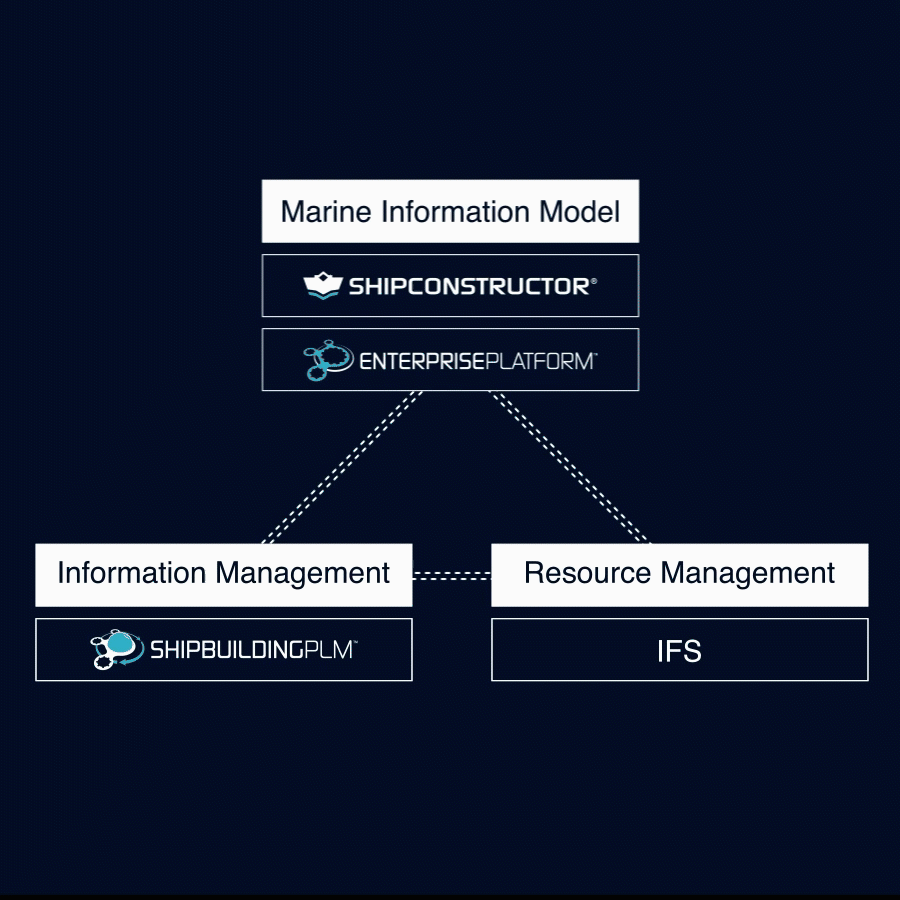
Changing the mindset
Changing an organization’s culture and mindset that makes full use of digital data is a noteworthy achievement. However, there are some core tenets that data-driven companies need to remember:
- Leadership commitment and adoption are required – not just lip service.
- Actions speak louder than words.
- Leadership must make decisions that align with a data-driven business.
- Technology is not the magic bullet – no single technology implementation will solve all data challenges.
- Updating enterprise business systems is vital, but it’s not the only thing needed (people and culture are just as important as process and tools).
- Data-driven ecosystems will initially require more upfront effort – nothing comes for free. There may be an initial setup to make sure the data will be available to all stakeholders and systems.
- The benefit, unfortunately, may not be attained instantly but rather soon after
- Make realistic and attainable goals – many digital transformation initiatives fail because the goal is unreachable (the goal should be achievable within several months).
- Make constant and steady progress – as the saying goes, “Rome wasn’t built in a day.”
- Impatience often leads to significant obstacles that will result in a lack of engagement and commitment, making it even harder to reach the goal.
Supporting goals with information
With a clear understanding of the difference between information and data, an idea of the information infrastructure needed to manage that information, and a commitment to improving data and information governance within your organization, the foundation for better decision making will be in place for the long term.
Evolving an organization to be more data-driven is not easy and cannot be solved only with technology. At all levels, there must be a commitment from the organization, patience to endure the obstacles that will arise without going back to the previous way of working, and a constant and steady-paced pursuit of the data-driven goal.
Chapter 2
Finding the Source of Truth
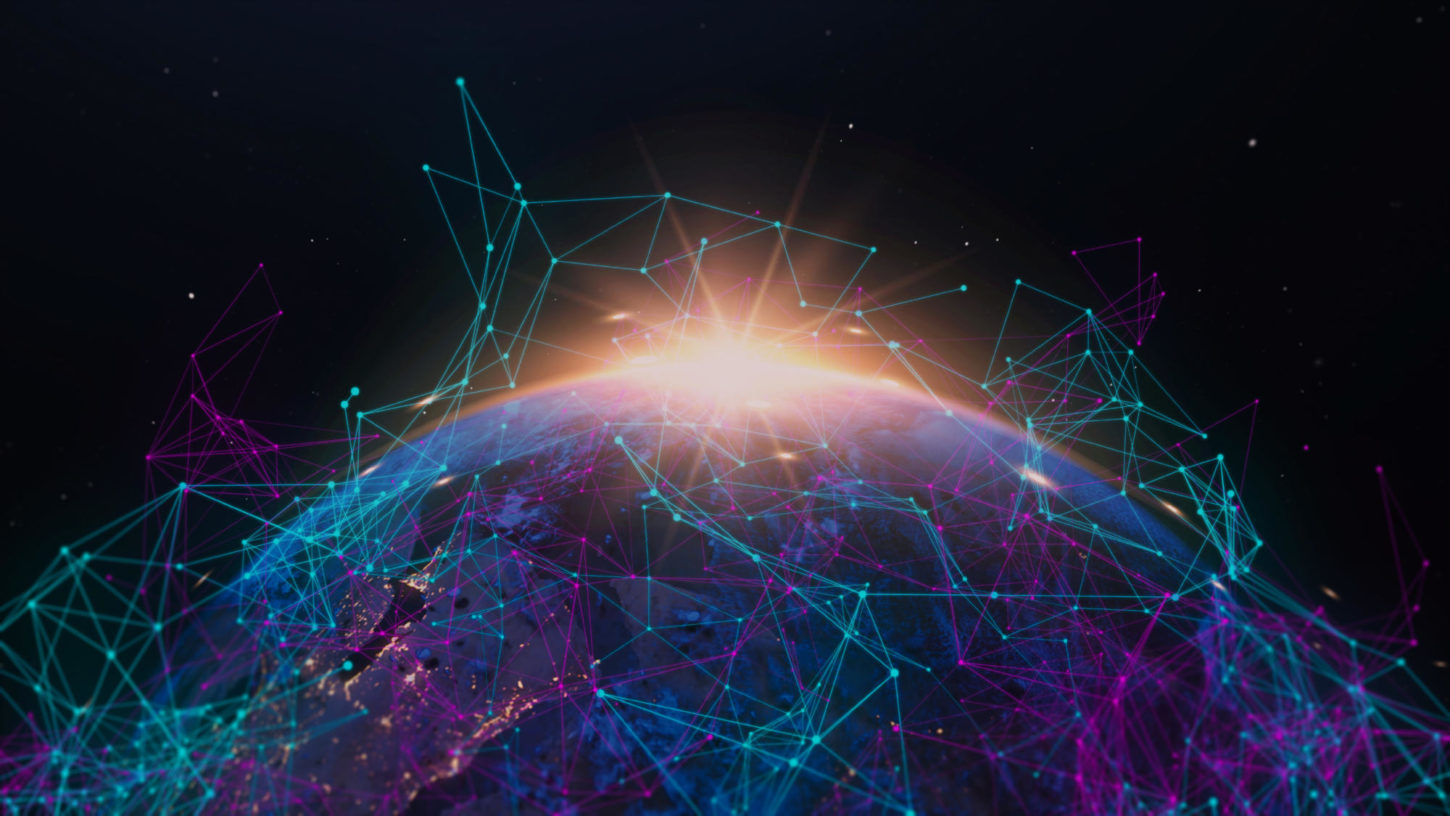
The Digital Twin is a virtual model of a process, product, and service of our asset. From conception to decommissioning, information gets created (which builds up our Digital Twin), and information gets consumed from our Digital Twin throughout the ship’s entire life cycle.
As it becomes easier for every department to access the data behind our digital twin, we can begin to get more out of our information over a longer time scale. In every phase of the lifecycle of our asset, we use information created in previous stages. We even use an earlier ship’s digital twin to aid in cost/performance estimates.
Ultimately, this allows for better decision-making, creating more information that gets included in our digital twin.
One step at a time
Many companies are looking to make small but valuable steps on their journey by adopting a digital twin solution for a specific asset. The goal is to see the entire ship as our physical asset, and therefore the digital twin should be a complete representation of the ship.
The amount of “sub-assets” (engines, steel, valves, pumps, propulsion, scrubbers, etc.) in a modern ship are in the 10s or 100s of thousands. Attempting to include them all in our digital twin representation is an enormous undertaking. Therefore, we have seen many digital twin solutions focus on a subset of our ship’s key and critical assets. From a holistic digital ship perspective, digital twin solutions for these asset subsets will act as a single node in a connected multi-node environment.
Platform of Platforms Architecture for the Digital Twin
Successful shipbuilders will opt for the popular Platform of Platforms Architecture for the Digital Twin over the ‘meshed’ and the ‘unified model.’
Several larger platforms contain highly related information with the Platform of Platforms approach, with specific apps tightly connected to these platforms.
Increasingly, platforms are becoming more open to participate in this environment and can connect, link, synchronize, federate, transfer, etc., information and processes to other platforms.
The future of the holistic Digital Twin will span:
- Multiple platforms.
- Multiple companies.
- Multiple platform vendors.
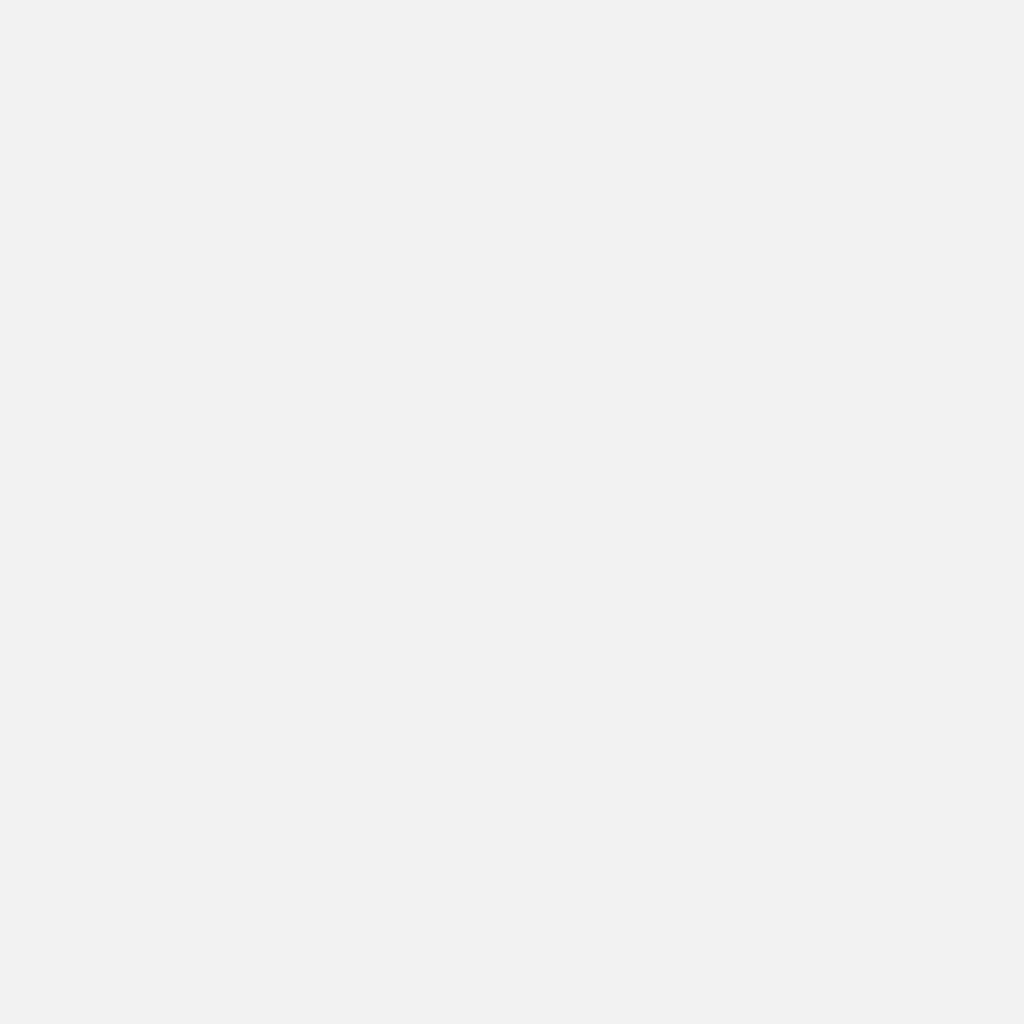
Tools for effective change management
Introducing a Platform of Platforms Architecture for the Digital Twin will require a change management strategy. The complexity of shipbuilding projects necessitates the use of computer-based tools to support change management.
However, no one tool is a silver bullet. Some may make certain aspects of change management more straightforward, but the right solution for your organization will depend on your specific challenges and requirements.
Guide to using IT-based tools for change management
- Use a standardized data model to develop a shared understanding of the underlying business process between various stakeholders.
- Include parent and child relationships, birth and death information, revision/modification history, and the details of any constraints on product use (guidance on use or applicability) for all product (information) records.
- Familiarize staff with the product information model and maintain an accurate recording discipline, whether their role is related to design, procurement, manufacturing, sales, maintenance, or support.
- Understand how changes are connected. If the change situation is not understood, a tool can provide only limited help.
- Present product information dynamically, enabling users to see a product’s change history from the past, present, and future.
Comparing change management technologies
- Office productivity tools: Provides tracked changes, document properties management, routing (through email).
- Document management system: Some document management systems provide ECM capabilities like versioning, workflow or routing, etc. However, such systems handle engineering artifacts as documents.
- CAD: Some of the COTS CAD software available for ship design and construction provides high levels of Engineering Change Management (ECM) capability without the need for a separate PDM/PLM system. These ECM-specific capabilities include the association between parts & assemblies, file versioning, change propagation/impact analysis/traceability, collaboration, etc. The ECM coverage is limited to the business processes handled by the CAD software (e.g., design & fabrication), after which hand-off is required to PDM/PLM/ERP systems to extend change management to other business functions in the shipyard/enterprise.
- PDM/PLM: PDM/PLM systems provide ECM capabilities, starting with the product definition phase, and can extend to the complete ship lifecycle. They provide necessary ECM functionalities, like versioning, workflow or routing, search/query, change propagation/impact analysis/traceability, collaboration, reports generator, knowledge management, etc.
- ERP: While ERP systems handle change management, such systems can trigger a change process based on production issues. When implementing a change requires a change in the product definition, a PLM system provides the necessary functionalities.
Actioning the Digital Twin
Finding the source of truth requires a Digital Twin that is used and updated throughout the vessel’s lifecycle. The recommended way to facilitate this Digital Twin is to implement a ‘Platform of Platforms’ approach with the help of PDM/PLM technology.
Chapter 3
How Information Availability Can Augment Shop Floor Activities
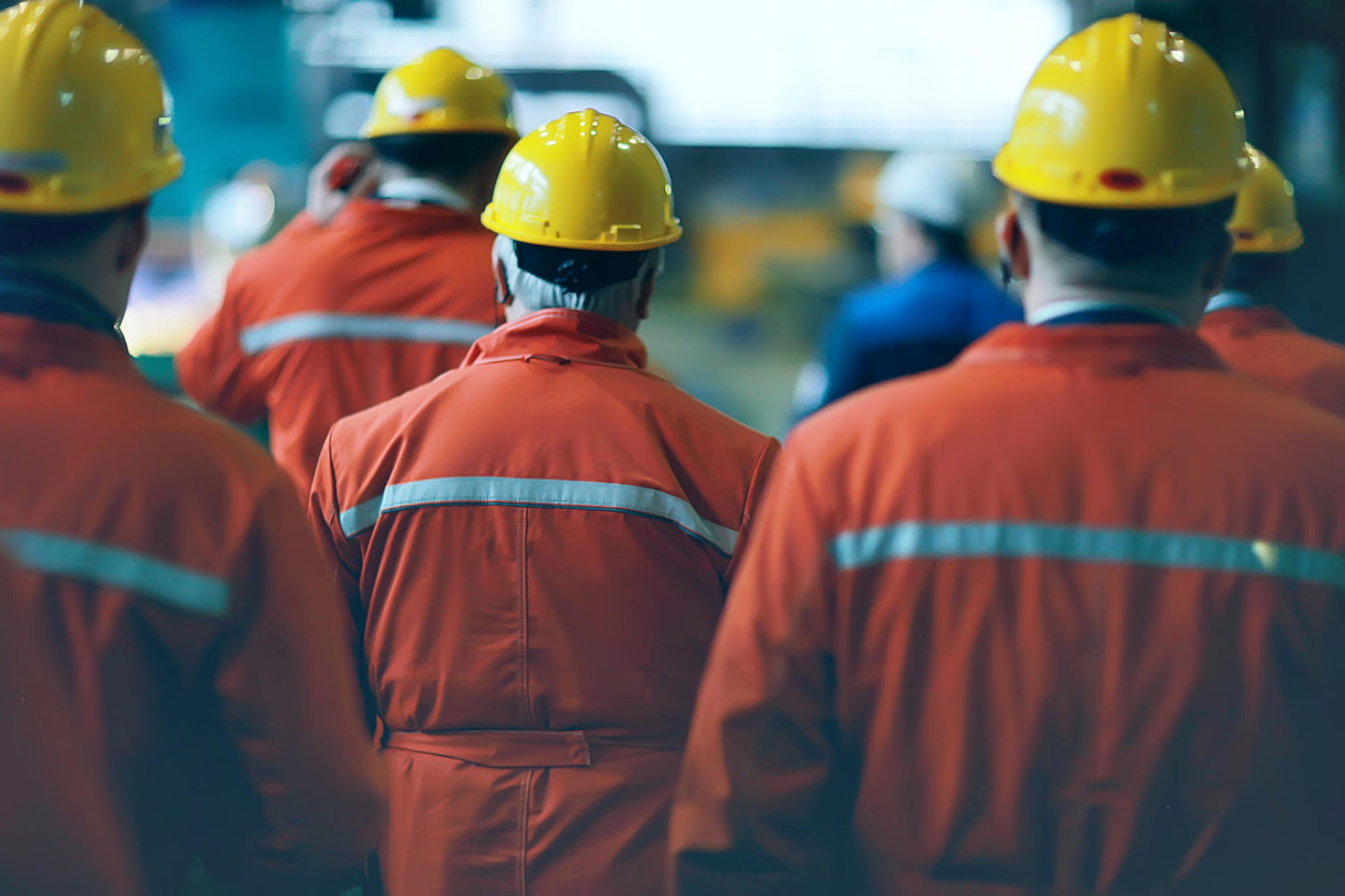
Information is at the heart of any digital or business transformation. Still, the conversation often focuses on the need to transform and not what that looks like on the waterfront. The shop floor is one area that will see large-scale improvements to what we can currently achieve thanks to better management and synchronization of shipyard information.
Automating production machinery
The automation of production floor machines is the future. Across the industry, more and more initiatives are emerging to drive machines on the shop floor using the digital twin. The successful implementation of these initiatives leads to completing increasingly complex tasks quicker and frees up skilled individuals on the shop floor to take on higher-value activities. A great example of this is the implementation of automated robotic welding.
In shipbuilding, we do not have the luxury of having a standard part/assembly. That means that we cannot just program the robot once and have it repeat itself. We need to support the most complex scenario of producing different welds, using different paths, and generating a different physical structure through information contained directly in the product model.
The workflow:
- Automatically identifies the welds in the 3D product model.
- The user refers to an interactive 3D visual drawing to configure the weld properties such as the weld standard, weld breaks, weld pitch, etc.
- Export the weld information and data like the geometry of the panel to the welding machine.
- The machine runs a path planning algorithm and evaluates several collision avoidance scenarios.
- When the operator is ready, they hit “Go,” and the robot automatically sizes up the panel with several touch sensing actions and then completes the welds.
The key: there was absolutely no programming of the robot required since all the weld path and attribute information was taken directly from the engineering information stored in the model. The weld planning path magic, kinematics calculation, and collision-free robot movement all happen with no input from the user.
A game-changer
This type of automation is truly a game-changer for our industry. What makes it happen is a transparent and seamless flow of information to the shop floor. As we explored in the earlier section, this starts with understanding your information and then getting control over it. This process significantly reduces the amount of time required to prepare an assembly for robotic welding, making it cost-effective for most global shipyards.
The push for Industry 4.0 or smart manufacturing has many shipyards looking at how they can improve their manufacturing capabilities. Combine that with the aging workforce about to retire, taking all the tacit knowledge with them. Shipyards must find some mechanism to capture that knowledge and use it going forward. With the abilities of today’s robots and the capabilities of today’s software to capture some knowledge, robotic welding is a perfect activity to streamline. When every department seamlessly passes information to the waterfront, we eliminate the programming of the robot and, in essence, are driving the robot from the information already contained in the information platform. Though it was thought to be impossible, we proved it through client implementations and NSRP project demonstrations.
Communication with the Shop Floor
When we talk about communication in the shipyard, particularly after covid-19, the discussion centers around verbal or text-based communication in the form of video calls or comments within a platform. However, communicating information to and from the shop floor effectively is overlooked, despite having a much more significant impact on the organization if done poorly.
Digital Transformation for Operations
Reporting back on progress
During the day, as construction progresses, progress needs to be reported back to the rest of the organization. An advanced way of doing this is using an augmented reality view or a virtual reality model. This is where a user will check off the items installed, the welds completed, and the items fabricated. This information will go back to the information platform, letting the rest of the organization identify bottlenecks or potential costly delays.
Reporting on required changes
Managing change is one of the key challenges for shipbuilders, and we touched on some of the tools and strategies needed to do so effectively in section two. One critical part of any change management strategy is the need for the shop floor to have a straightforward way to report the issues they see to the engineering team.
When a process and system are in place to capture a problem during construction, the shop floor user can request guidance from an engineer via a virtual dashboard or similar system. This request will feed the issue back to the engineering team and information platform. With the issue resolved, what has changed propagates back to the information platform, making it clear to every department how it impacts them. For the shop floor, this removes guesswork over what they need to execute.
Steps to a smarter shipyard
The missing piece in many shipyards that prevents the shop floor from taking full advantage of the digital twin is not having the right information at the right time in the right format. To make that possible, the shipyard needs to have:
- An information platform that can act as a single source of truth.
- Tools that use agnostic inputs and outputs.
- A culture that values sharing information across the organization.
With these elements in place, the digital twin information you already have can benefit downstream activities all the way to the waterfront. The result is a shop floor that is smarter, makes the best use of resources, and frees up your team to take on the highest value tasks.