Highly customized products in short series characterize the shipbuilding industry. In shipbuilding projects, engineering changes introduced throughout the project duration are unavoidable. They cannot be planned or introduced to the next production run since ships are built only once and rarely repeated. Adding to the challenge is the complex structure of a ship, the numerous working disciplines involved, and the vast amount of information flowing between different stakeholders during design and construction, including design consultants, suppliers, and subcontractors who may be affected by a change.
Why is managing change in shipbuilding important?
Since the sheer number of changes during a new build or refit/conversion project is very high and can affect several entities in the value chain, poorly managed change processes impact the ability of a shipyard to deliver ships on time and budget. Also, 70-85% of a ship’s construction cost is predetermined in the design and engineering phase, so using an appropriate ship design tool (ship CAD software) that provides capabilities for rapidly developing the ship design with efficient tools for making design and engineering changes as the design evolves is critical. Add to that the need to keep track of all changes during the design and construction phases, manage the change process, and communicate the changes effectively to all stakeholders on time, every time. This is the only way to minimize the potential for errors and reduce time-consuming rework and resulting costs.
Common types of change
There are two aspects to be considered – engineering changes and engineering change management. Ship design is an iterative process, and engineering changes are natural and expected as a design evolves or gets refined. These changes are made using the design team’s CAD tool(s). Different CAD tools are often used for different phases of ship design – one for concept design and another for initial/basic and detail design. How easily and efficiently the ship CAD tool manages these changes as the design evolves, underpins, and adds to the competency of the design team in developing their designs quickly. For this, the ship CAD tool must have capabilities like associative and parametric modeling, catalog support, rules, and standards, links between functional (2D like P&ID) and 3D design (like pipe routing in 3D), etc. The ship CAD tool should provide easy change management capabilities for the many continual changes as the design progresses, with the ability to see what has changed and to create an audit trail of the changes made by the design team. The different design steps in the ship CAD tool, design change activities, and the impact on the model should be tracked and managed through tasks and sub-tasks in the CAD tool itself (refer to Fig. 5 below).
On the other hand, engineering change management of released designs comes into play when a change request comes up for a design already released to a downstream stakeholder. This means the change request would affect all associated released drawings, bill of materials (BOMs), and production outputs or manufacturing information (MI). A change request can come from any source, starting with the customer, to production, supplier, or class, and downstream stakeholders may include entities outside the shipyard, like subcontractors. This is best managed by a PLM or Product Lifecycle Management system.

While changes come up both during ship design and construction, the design changes during the concept and basic design phases are macroscopic (e.g., changes to hull form) and significantly impact the overall design and the lifecycle cost of the vessel. Changes during detail and production design and production phases of the ship are at a more detailed level and significantly impact the production schedule and cost.
A change at first glance may appear as simple (e.g., changing a bulkhead location), but since the impact of the change may cascade through the product model (3D model of the vessel) and to associated drawings and MI, the ship CAD tool needs to have several capabilities or functions to make the changes or design modifications efficiently and rapidly, and the mechanism to track and manage those changes.
Change to existing models
Different CAD software use different modeling approaches and, consequently, different mechanisms to carry out changes in the model. These vary from script or macro-based approaches in which the model is rebuilt from an underlying set of scripts or macros on demand to parametric modeling, associative modeling, and hybrid. The flexibility, versatility, and efficiency of ship CAD tools become critical factors enabling design innovation in shipbuilding. The blog The Importance of Parametric Modeling elaborates on this topic further.
While it is imperative that designers and drafters can make fast changes in the model, it is equally important that they can view, control, and understand the results of the change before it happens and can limit the impact of the change only to items they choose (refer Fig. 1 below). The impact of a change, e.g., to modeled structural parts, may extend to associated released drawings, bill of materials (BOMs), MI, and other disciplines like piping, HVAC, or electrical.
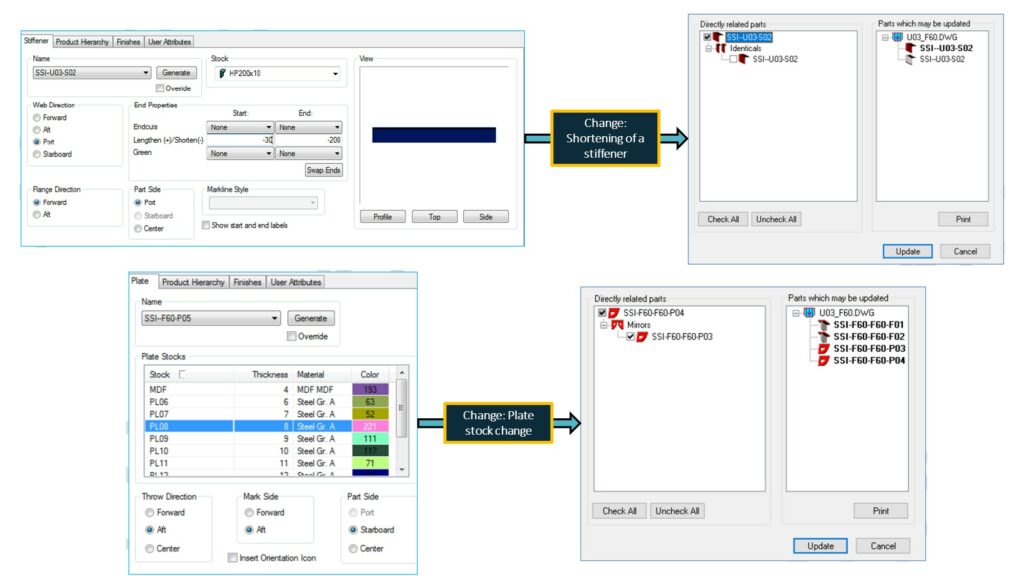
Change to catalogs, rules, and standards
Changes to catalogs, rules, and standards should be automatically reflected in the 3D model under user control. For outfitting disciplines, e.g., piping, the change should be reflected in the corresponding P&ID, again under user control.
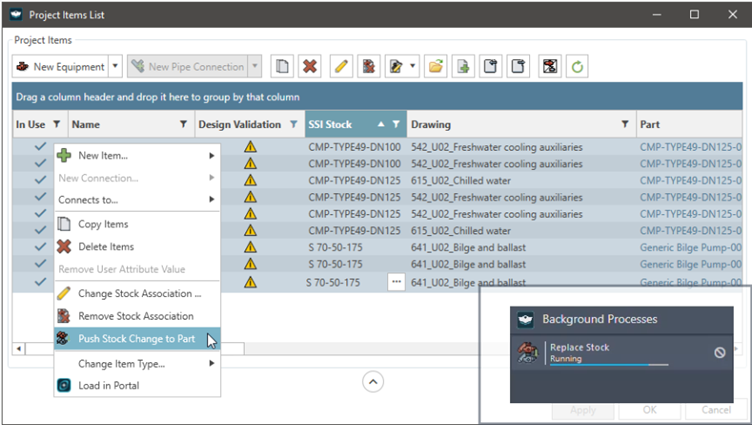
Changes across sister ships
When it comes to sister ships, the challenge is to make the changes only once and transfer the changes to sister ships. Since each vessel in the series would be at a different design or construction stage, the resulting change or the effects of applying that change on each ship may differ. The change has to be viewed for each ship configuration with all its surrounding items.
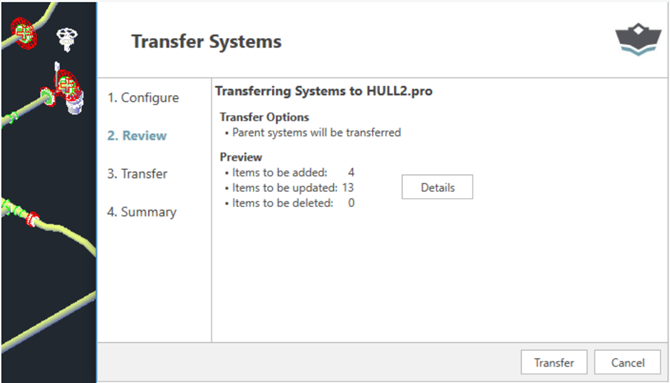
Change status reporting
Task Management in CAD enables accurate and comprehensive change status reporting while a ship design evolves through iterative design (refer to Fig. 4 below). Task Management is synced with engineering change requests (ECRs) from PLM. This allows designs to be iterated within a workgroup before they need a formal review in a PLM system (refer to Fig. 5 below).
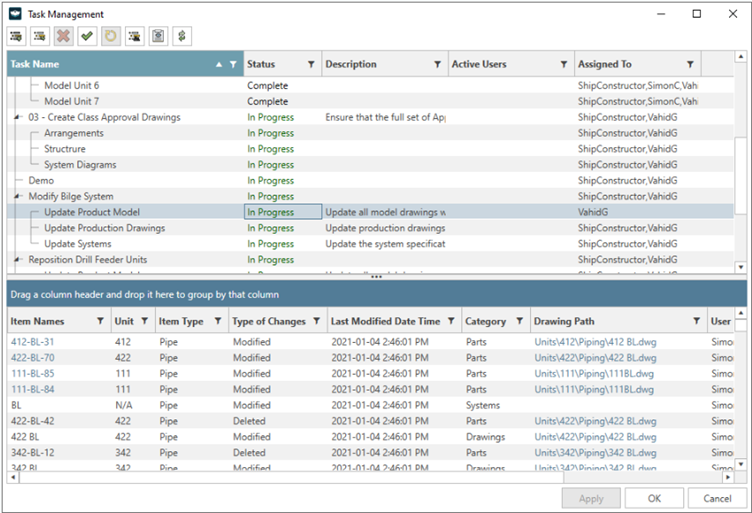
How does a PLM system help manage change?
Managing engineering changes for released designs needs a proper change management process handled by a PLM system. Because there are myriad players in the shipbuilding value chain, tight and efficient engineering change management (ECM) directly affects a shipyard’s ability to deliver ships on time and on budget.
A PLM system provides ECM capabilities by organizing, controlling, and managing the workflow and information flow for engineering changes (ECs), starting from problem reports (PRs) to engineering change requests (ECRs) to change execution (engineering change orders or ECOs which authorize the actual implementation of a change). A shipbuilding-specific PLM system would support ECM through different phases of ship design, between various departments in a shipyard, and across the extended enterprise to include sub-contractors and class, for example.
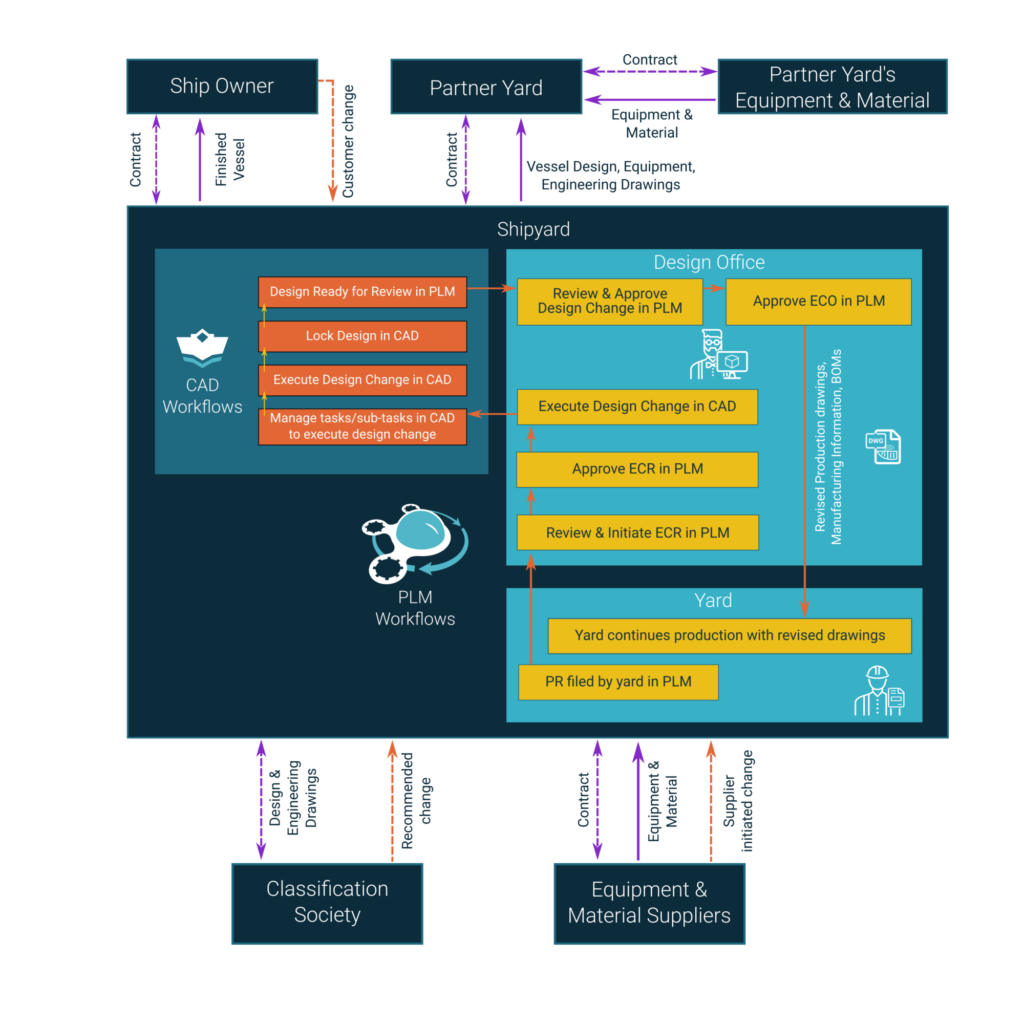
A shipbuilding-specific PLM system should seamlessly integrate with the ship CAD system to trace individual change activities at the part level. This means that while designers and drafters make changes in CAD as the ship design evolves, part-level changes and relationships to all deliverables (e.g., a pipe spool drawing getting revised with a change in pipe routing) are tracked and managed automatically by the PLM system, transparent to the designer or drafters using the CAD system (refer Fig. 6 below). Further, all those changes should be applied effectively to sister ships using the CAD system without rework and still tracked and managed at the part level by the PLM system. This is where a shipbuilding-specific PLM system would typically differ from a generic PLM system implemented for shipbuilding. Generic PLM systems do not understand the relationships inherent in a vessel (even with substantial customization) and between the model and production outputs, especially once sister ships come into play. In many cases where generic PLM systems are implemented for shipbuilding, they only provide change management capabilities at the drawing or document level, not at the individual part level.
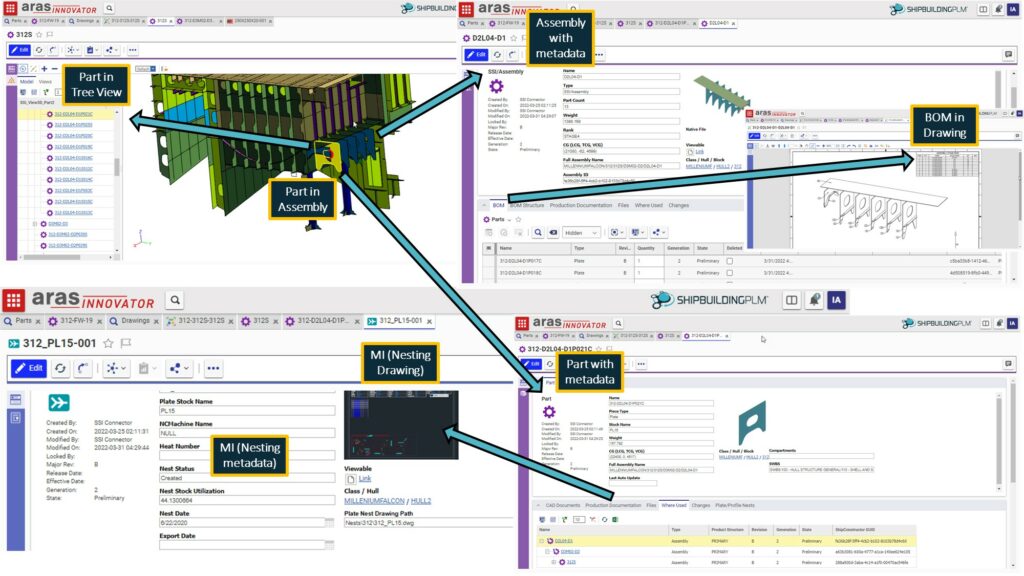
The PLM system would also enable changes to be managed not only during design and construction but also through the entire lifecycle of a ship with full traceability.
The nature of shipbuilding and concurrent engineering across multiple disciplines is complex, and because of this, unidentified change propagation is a huge challenge. Many shipyards do not have systems in place to identify or aid in the identification of change propagation and instead rely on the experience of their employees.
A shipbuilding-specific PLM system, like SSI ShipbuildingPLM, possesses the capabilities to identify change propagation, meaning it can provide a precise list of items affected by a change, which aids in decision-making. This is far superior to paper-based ECM or keeping track of changes manually and removes dependency on personal experience in assessing the impact of a change, or if a change propagates outside the team area of expertise.
A PLM system helps overcome the difficulties in comprehending complicated technical drawings defining the change by providing 3D visualization (3D model) of the changed and affected items at an individual part level, drawing comparisons between revisions, and accessing all related textual information like item parameters or part metadata. This makes it easy for end-receivers who must carry out the change to interpret the information and for non-technical staff involved in the review and approval process as decision-makers.
The PLM system also facilitates central storage and retrieval of ECM-related engineering data by all stakeholders, facilitating real-time collaboration and maintaining change history. When similar issues or change requests come up again in other projects, a shipyard can retrieve and study past ECRs from the PLM system and reuse the knowledge, saving valuable engineering capacity.
Conclusion
The right approach, technology, and tools to effectively execute and manage engineering changes in ship design and construction can create significant competitive advantages for a shipyard. In addition, the technology should be easy to adopt without making change management cumbersome. It is best that design groups can go through different design iterations in a CAD system as a ship design evolves without each design iteration at a workgroup level being rigorously controlled by a formal change management process in a PLM system. In contrast, released designs are managed formally by an engineering change management (ECM) process using a shipbuilding industry-specific PLM system, with seamless integration between the CAD and PLM systems. SSI ShipConstructor and ShipbuildingPLM provide such an environment.