‘Parametric Modeling’ is often mentioned when discussing CAD systems in the shipbuilding industry. What does it mean? How is shipbuilding-specific parametric CAD software different from generic parametric CAD software? In this post we’ll explore how parametric modeling helps streamline the ship design process, quickly creating an intelligent 3D product model. Then, we’ll look at how ShipConstructor works with parametrics to manage change.
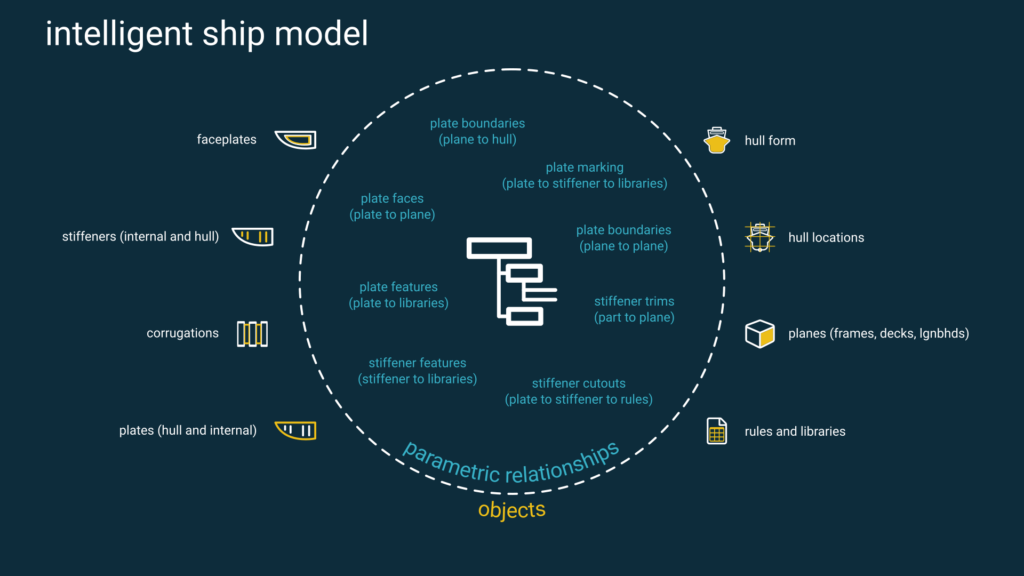
What is parametric modeling?
Parametric modeling is when parts are defined using algorithmic processes rather than direct manipulation. When a parameter changes, the part changes. Parts can be defined by numeric input, datum lines, interfacing parts, geometric parameters, features, variables, and constraints.
Direct modeling, as opposed to parametric modeling, is modeling un-intelligent parts. Geometry is defined without a relationship to another part or algorithmic value.
Why a parametric model?
A parametric part is quickly created by inputting basic parameters, e.g., length, width, height. This may also include selecting associated parts, datum lines, stock association and assembly (connecting parts must be compatible). The part inherits further properties from its relationship to catalogs and standards. A part is modified when a parameter or connecting part is changed. For example, if you move a plate part, any connecting parts (like stiffeners) would move with the plate. If you move a pump, the connecting pipe will move with it and adjust between the pump and connecting asset (e.g., valves, tanks, etc.).
Here’s an example of some of the parameter inputs used to define two types of common shipbuilding parts within ShipConstructor. Input parameters can be default values, only changed when required.
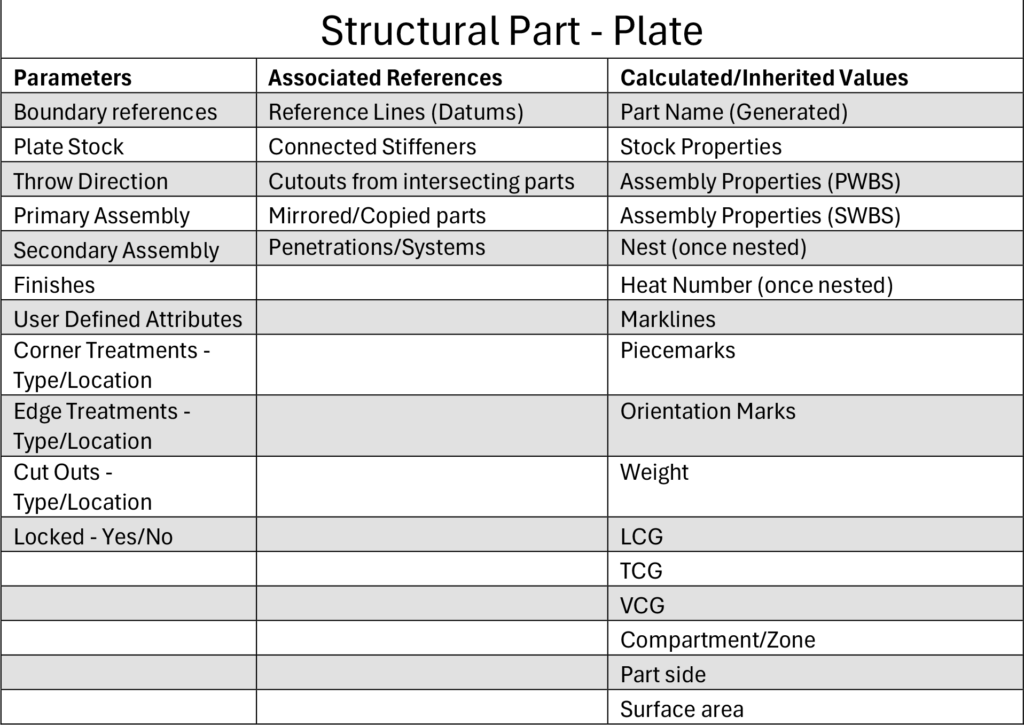
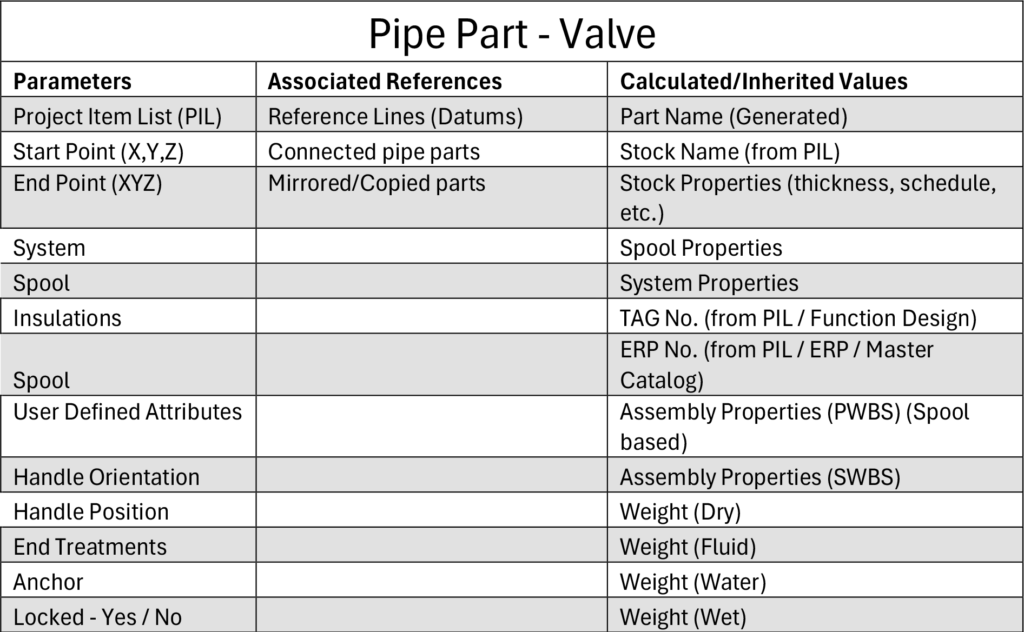
Benefits
There are 3 main benefits to parametric modeling
1. Part Definition
Designers can quickly define intelligent parts without manually drawing the geometry and adding data. A timesaving ten-fold!
2. Part Modification
Designers can quickly modify parts by updating a parameter. For example, changing the height above the baseline of a tank top deck (defined by a mold plane) moves the deck to the new height.
3. Updating related parts
Associated parts are updated. Further to the previous example, all the frames below the deck would update in shape to suit the modified deck height as their vertical boundaries are defined by the baseline and tank top.
Industry-Specific VS Generic CAD Parametrics
Generic CAD software typically use parameters that are geometric, stock, or material-based, and/or connected to related geometry. Industry-specific software, like ShipConstructor, goes a few steps further by incorporating shipbuilding-specific concepts and manufacturing methodologies. These parameters cannot be easily configured or controlled in generic solutions and help to streamline the design process. Industry-Specific Parameters
Industry-specific parameters include
- Reference to mold planes – Frames, decks, longitudinals
- Ship references – Centreline, port, starboard, forward, aft
- Throw directions – Up, down, port, starboard, forward, aft
- Work Breakdown Structures – Build Strategy, Systems
- Compartments / Functional Spaces
- Project Item Lists (Master Equipment Lists)
- Association to change management controls
- Intelligent ship-specific referencing
- Ship-specific part definitions e.g., Corrugated bulkheads, extruded panels, etc.
Manufacturing Methodologies
Industry-specific manufacturing methodologies include
- Plate marklines
- Shipbuilding datums
- Support for machines commonly used in industry – profile cutters, pipe benders, robotic welders, etc.
- Systems management
- Industry-specific production outputs
Why industry-specific parametric modeling tools?
Not all parametric modelers are created equal
Parametric modeling tools can be complex, requiring significant training and expertise to use effectively. Parametric modeling uses automation to make design changes throughout the model. This poses a risk that designers will not be able to understand the flow on effects of the change.
Industry-Specific parametric modeling
When parametric modeling is done right, it is great; when not done correctly, it can lead to a tangle of unforeseen impacts to the product model. Industry-specific parametric modeling tools, ShipConstructor in particular, mitigates this risk by introducing industry-specific workflows to maintain the project integrity and carefully track change. The industry-specific parameters and manufacturing methodologies listed above are enhanced further with intelligent constraints, intelligent revision tracking (down to the part level), intelligent part locking, and the common 3D model being the single source of information for all production drawings and outputs.
Not all modeling has to be fully parametric
Shipbuilding projects are on a huge scale, and in many cases, the project may be a one-off build. Parametric modeling may introduce unnecessary complexity and delay to a project. Particularly generic CAD parametric software where the overhead effort in training and setup is not justified. Generic CAD Parametric modeling excels at creating precise, geometric shapes subject to change e.g., mechanical components.
Some flexibility in the level of parametrics is required as all projects are different. A standard should be agreed upon to effectively support design activity. See further reading for more information on project set up.
Conclusion
There are many CAD tools available – some create direct models; others have partial parametric inputs. Generic CAD tools offer great parametric capabilities for mechanical or component design e.g., turn the handle, see the valve open. The shipbuilding industry is unique for a number of reasons, particularly it’s scale. Success requires a parametric modeling tool made specifically for the business of shipbuilding.
A shipbuilding-specific CAD tool, like ShipConstructor, creates an intelligent ship model, using shipbuilding-specific parts, terminology, drawings, and production processes. Crucially, it also has the capacity to ensure that parametric changes don’t negatively impact the rest of the model.
Further reading
Ensuring design and engineering teams produce standardized, repeatable deliverables
Part 1: The impact of non-standard deliverables
Ensuring Design and Engineering Teams Produce Standardized Repeatable Deliverable
Creating Processes for Standardized Shipbuilding Deliverables
Part 2: The impact of non-standard deliverables
Creating Processes for Standardized Shipbuilding Deliverables