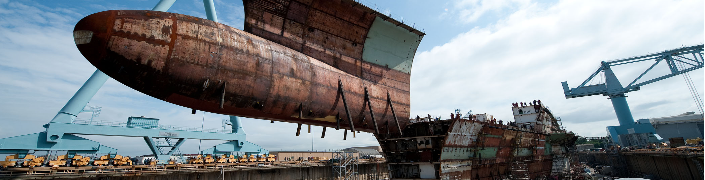
The product breakdown structure or build strategy is one of the most important pieces of information in any shipbuilding project. A good build strategy will consider and be optimized for a yard’s facility and the skills of the workforce, thereby significantly reducing the cost of building your project. ShipConstructor’s ProductHierarchy product is one of the key components in SSI’s solution which allows management of your project’s build strategy. Product hierarchies, (created by the ProductHierarchy product) allow you to easily manage your project in a visual and interactive way. More importantly, they are fully integrated into the MIM.
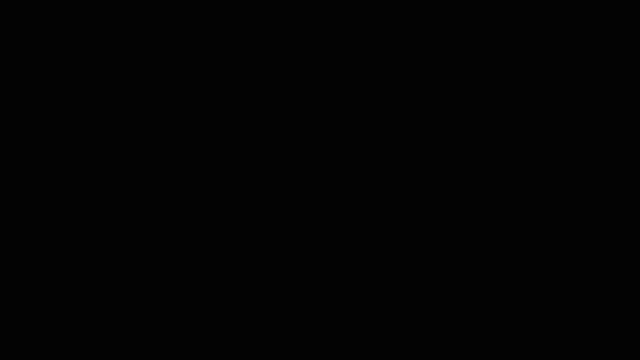
Digital Shipbuilding
Get a first-hand experience of what the design, build, and maintenance phases are like in an increasingly digital shipyard.
Experience nowThe ProductHierarchy product can in some respects be considered the hub of ShipConstructor because it automates many downstream workflows such as creating your deliverable drawings or reports as well as those used to organize, plan and coordinate your project. Proper use of ProductHierarchy will improve engineering, operations and production efficiency by supporting lean initiatives such as need by date or just in time methodology. Despite all the benefits which can be extracted from using ProductHierarchy, it remains one of the products that I often see as not being fully leveraged by many of our clients.
Quick Overview of ProductHierarchy
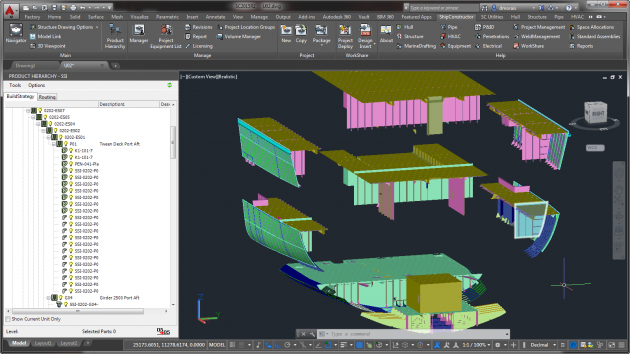
Using ProductHierarchy’s modern Graphical User Interface (GUI) you can easily create assemblies, subassemblies, panels, or any other type of grouping for absolutely any reason. It allows you to move parts between these assemblies (groups) by simply clicking and dragging. It automatically updates your part names by using the rules and standards you have defined for the project so mistakes are virtually eliminated. Default assemblies are set up to reduce the amount of “decision making” required by modelers but also are flexible enough to allow any modifications required at any stage of your project.
ProductHierarchy supports the creation of multiple product hierarchies. Each of the product hierarchies are fully integrated into ShipConstructor allowing reporting, filtering, attribute inheritance and drawing generation based on any product hierarchy. Users have often created multiple product hierarchies for numerous reasons:
- Purchasing information
- Facility routing information
- Critical system analysis such as weapons systems. This includes all disciplines (hull & structure, pipe, HVAC, supports, Electrical, etc.)
- Multiple build strategies when a ship will be built at different yards with unique facility constraints
- Sister ship management
- Change management
- Etc.
Another key advantage of ProductHierarchy is that it has a direct bidirectional connection to any ShipConstructor drawing. This facilitates more visual and instantaneous feedback for any changes. It can even be used in a lightweight Navisworks model to aid in helping you understand your product structure.
Why clients are not fully utilizing ProductHierarchy
There are several reasons for this and I want to discuss the main two reasons from my discussions with our clients as to why I think ProductHierarchy is underutilized.
1. Slow to Change Processes and Workflows
Almost every ship today is designed and engineered with modern shipbuilding software. This transition in our industry to using more modern and digital tools has enabled us to improve our design and engineering of our products.
Production processes on the other hand have not really changed very much. By using the tools available today we have just as much opportunity, if not more, to improve the construction of our ships than the engineering of the ship.
It is not uncommon for me to hear that the same block managed by Foreman A will be done 5% faster than if managed by Foreman B. The reason for this discrepancy is because each decided to build the block in their own way. I see this as a huge issue and great opportunity for where a yard can reduce cost.
By accurately representing the build sequence digitally you would be able to eliminate these difference by creating a comprehensive build package containing the information to build the block in the most cost effective way. All the construction decisions should include waterfront personnel and engineering and then be captured in the ShipConstructor project.
There are several benefits of capturing this information in the ShipConstructor project:
- Capturing of Knowledge: One major issue in our industry is the loss of experienced personnel on the waterfront. In the good old days, many engineers left it up to the production floor to determine the best way to assemble your ship. However, these experienced personnel are starting to retire and are leaving a hole for many organizations. By leveraging these experts during the engineering of the project and capturing their years of experience into the ShipConstructor project, you will ensure that the ship is assembled as efficiently as possible. The output from ShipConstructor will in essence be a step-by-step manual on how to build your project. The analogy I give is, “If your build strategy is done properly then the output will be similar to an IKEA instruction manual for a ship.” This will translate to repeatable and quality output which will not require the same type of experts we currently need.
- Better scheduling and estimation: If we look at the ramifications of the scenario mentioned above when the cost of a single block can be 5% slower than the exact same previous block, it is no wonder that our schedules are never correct. A single block even taking 1% longer can affect our tightly connected timetables even without considering the 1% additional cost. If a block is not completed on time then we need to make some costly compromises. This is because by not moving that block to the next stage, it will mean that it will halt all the previous assemblies, subassemblies and panels from progressing to the next stage. On the other hand, if you capture the actual build sequence, it will allow more accurate scheduling and that is a huge cost saving for any yard.
- Promote better communication between engineering and production: One thing I have definitely seen in my years in shipbuilding is the rivalry between production and engineering. I have also seen many companies make huge strides to bridge the gap. Almost every successful company understands that by having all teams working together as one single team, they will get better results. By having the production team work with the engineering and/or planning team to capture the “true” build sequence, they will strengthen the teams’ relationship…hopefullyJ.
I understand the reality and difficulties of making these type of changes but I also know the benefits of making them as well.
2. Lack of Available Resources
This is where SSI and our representatives need to take some ownership. The capability of ProductHierarchy is huge and is as intuitive as using a hammer. However, like a hammer without guidance and good resources, it can be difficult for you to understand the best way to represent your product breakdown structure within ShipConstructor or the endless possibilities available using secondary product hierarchies.
We are currently investing in ways to provide more resources to you in many different formats and delivery methods. These will be documents, images, workflow diagrams, forum discussions, videos, training material and even blog postsJ. If you have any other ideas please let me know.
In the meantime, if this post stirs up any questions or ideas, please feel free to contact us or your SSI representative.
Closing Remarks
Many shipyards are still using traditional approaches by not defining an accurate manufacturing build sequence within ShipConstructor. This was arguably acceptable in the past. However, because the experienced workforce that is capable of deciding how the ship should be assembled is shrinking, we simply need to change our current processes and even thinking to achieve a sustainable strategy.
Capturing the knowledge from the production experts (before they decide to retire) within the engineering solution is the only way we can secure and record this wisdom forever. This will ensure their knowledge is in a digital format and allow future team members to access this information.
A well thought out and designed build strategy can be produced that reflects the reality of how the structure will be assembled. This will maximize facility constraints and the experience of senior production floor personnel which, in the end, will reduce man hours, facilitate repeatability, improve schedules and increase quality.
Additionally, the capabilities in the ProductHierarchy product will allow for production to be much more efficient by visualizing and simulating the build sequence. The interactive features of working with your build sequence will promote engineering, planning and production to work together. This new type of collaboration and open communication will be a more sustainable solution. This capture of knowledge will also have additional benefits by identifying issues much earlier in the design, even before a part is cut.