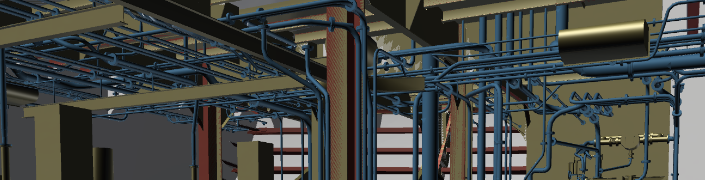
Last week I visited several of SSI’s clients in the Pacific North West: Guido Perla & Associates, Inc.; The Glosten Associates; Vigor Industrial; Gunderson Marine and Jensen. There was definitely a common theme of, “Actively investing in incorporating more detail and information into their projects.” It did not matter if it was a shipyard or a design agent, they are all investing time, effort and $ to produce a more complete model. This investment will result in reduced overall time and cost to build a vessel by allowing better planning, the ability to identify interferences earlier, improved just in time purchasing, better interactions between tools, earlier identification of potential issues and the ability to make relevant information available for better decisions.
It has taken a while, but I now feel that our industry understands that if we invest more time in creating a more comprehensive model, it will increase the quality, improve orchestration of activities, find issues earlier, increase down hand welding and reduce manual field cutting, all of which decrease the amount of time and cost it takes to build a vessel. However “adding more detail” means different things to different organizations. This will always be the case because the ideal amount of details needs to incorporate more than just “Best Practices” such as pre-outfitting, it also needs to take into account facility constraints (cranes, panel lines, CNC burning capabilities, bending press, etc.), skill level of personnel on the waterfront, engineering skill level, internal processes and tools.
Each organization has its own ideas and philosophies as to what level of features to include in their model. I cannot talk too much about them but I believe all the clients I visited have very interesting and successful strategies.
To what level of detail do you include your projects?
I had several long discussions about just this topic. What I was trying to better understand is how one goes about deciding how much detail should be included within ShipConstructor.
This might sound like an easy question for those of you who are not in the shipbuilding industry but because of the long history and tradition of shipbuilding there has been a tendency to only model the major components of the ship structure with only a cursory effort on outfitting (pipes, HVAC, equipment, electrical, etc.). For some marine structures in specific markets this strategy is still used, but overall in the shipbuilding industry there is a trend to expand the design and modeling of more components for the reasons mentioned above.
A challenge that was apparent to me in my conversations was that there is little to no quantifiable information on what the overall improvement would be with a more detailed package. Everyone agrees that adding more details to their model would have downstream benefits but it is all anecdotal. This is why some yards and design agencies (definitely not the ones I visited on this trip) decide to stick with the status quo and not include many of the artifacts which will be part of the vessel. For example many still do not invest time to:
- Pre-outfit
- Model electrical wire ways and transits
- Model pipe under 2”
- Include adequate marking on plates
- Create penetrations
- Include beveling information
- Place hangers and supports
- Place all equipment (manholes, pumps, winches, etc.)
- Include routing information
- Etc.
Without quantifiable information it is difficult for any organization to know what level of detail they should require from engineering. This makes it challenging for yard engineering managers and design agencies to advocate a more detailed production design package even though they feel it would reduce the overall cost of the project. The decision maker will need to know what ROI (Return On Investment) they will receive from the extra effort and $$$ spent on this more complete model. Unfortunately many organizations do not have this information.
This is especially difficult for design agencies since they usually have no information to support their more complete designs. They are often perceived to be a cost and not an investment. This is a similar challenge that we have seen within shipyards where the engineering team has identified an area where they can significantly improve production if they were able to spend additional time detailing more of the project. Unfortunately what happens in this case is that additional engineering hours are considered as an additional cost and not an investment.
I firmly believe all shipbuilders know they need to improve by including more detailed and relevant information to the project model. Even if there is no quantifiable information, it is understood that there are improvements in engineering which can be made that will reduce overall costs. Because companies realize this, I have definitely seen a tendency for shipbuilders to add more information to their project. However, due to the fact that engineering is in essence still incorrectly viewed as a cost center, these companies are trying to do more with less time. Admittedly, trying to do more with less is something we all need to do and with the continuing addition of features in ShipConstructor there are always ways clients can be more efficient with what they are doing today.
The problem from my point of view is that if you are trying to make a more accurate and complete model, eventually you will come to a point where you will need to increase your engineering hours/budget to add extra information for the overall good of the project. There is no way around that fact. It is nice to see that the clients that I visited understand that engineering is not just a sunk cost, it is an investment. If you invest wisely you can add some cost during engineering but it will be paid back in spades during production where the real cost saving will be.
Closing Remarks
The trajectory is definitely moving to a more detailed model and it will only be a matter of time before the industry norm will be that every single component be modeled. It would be ideal and much easier for engineering mangers and design agencies to justify the benefits of a more complete and comprehensive engineering package but even without this quantifiable information, if a little bit of time is spent investigating the cost vs. benefit, I think it is an obvious conclusion.
Investing additional time to create a more feature-rich model will allow better material handling, estimation, planning, identify issues earlier, improve purchasing schedules, and the list goes on.
You need to have the understanding that the time in engineering is an Investment and not a cost. If it was not an investment why would we spend time on it at all? As with any investment, we need to constantly look at how we can improve and in some instances you need to invest a little to gain much more.
Special thanks
Every single client I visited on this trip is creating some awesome packages and vessels. The reason why I wrote this post was because of the question: Why are these organizations increasing their time (investment) in creating a more detail and information rich model while others are staying at the traditional status quo?
Thanks to
- Guido Perla, Chris Chuhran, Jeffrey Wallace & Stefen T.Wolczko – Guido Perla & Associates, Inc.
- Matt Witzeling– Gunderson Marine
- Kevin Hein– Vigor Industrial
- Craig Savey- Jensen
- Josh Horst- The Glosten Associates
For the enlightening discussions.