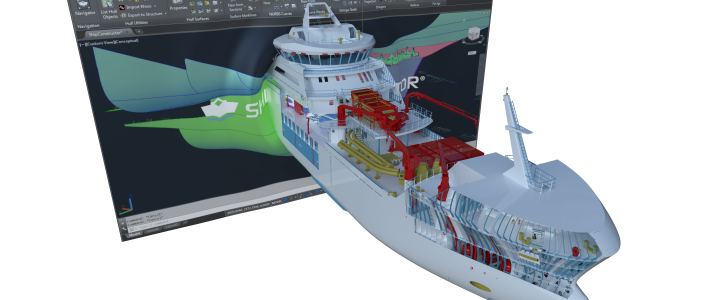
In this blog post I will continue the discussion of the Future of Shipbuilding series focusing on Detail Design and Production Planning.
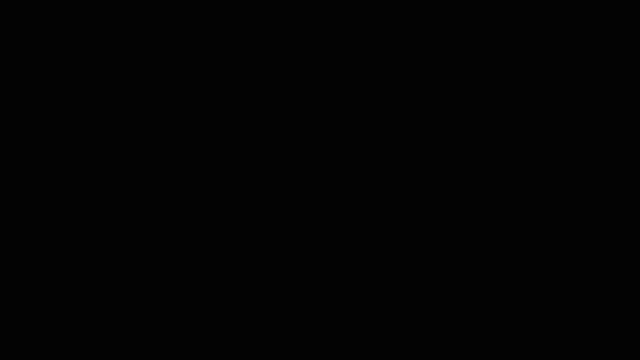
Digital Shipbuilding
Get a first-hand experience of what the design, build, and maintenance phases are like in an increasingly digital shipyard.
Experience nowNo more Changing Context and Waiting
With a dynamic concurrent environment, the current way we access information will fundamentally change in the future. Currently when we have completed our static task, a person or multiple people generate different formats/representations of that information and pass it to a different department. This manual generation of information will not happen. Systems are great at these types of tasks and will do virtually all transformations of information from one team to a context that can be understood by another team.
This means the team member that rely on certain information from another team will always have it available. There are several ways information can be passed. These are outlined as follows:
1. User Initiated Request
An important point to mention is that a person will be able to query/request the information they need without changing applications. This will allow the user to stay in the context (application) that they will use to make a decision based on the information they received. We will no longer have over 30% of people’s time looking and translating information from other teams into a format they need to make decisions.
Another reason that users will not have to change contexts is because there will be increasing use Intelligent Virtual Assistants. These assistants are derived from the current chat bots we are hearing about from Microsoft and Facebook among others, which allow users to ask questions to the assistant and get answers. Examples would be:
- Who made modifications to …?
- What parts were modified in ECR 123?
- What are the type of equipment’s I can use in zone X?
- What compartment is this object in?
- Where is this stock used in the other ships?
- How many parts did I create today?
- Which parts do not have production details verified?
- What is the weight of block 123?
- Show me all related classification drawings for this section.
In addition Intelligent Virtual assistants will be able to do all of above with the addition of providing content and performing actions. Examples would be:
- Open the drawing where this part is modeled
- Create me a visual representation of all changes in ECR 123
- Get me the Vendor Furnished Information for pump ABC
- Get visual representation of assembly X
- Send an email to the creator of this part and tell them that they need to….
- Create an ECR for this assembly
- Approve all production drawings associated to this assembly
- Show me all model parts which are inconsistent with functional design
- Notify simulation team to conduct a local FEA of this section and send me the results
2. Asynchronous Automatic System Determination
Another way, and a much better method a person will get information will be automatically determined by the system’s environment. Sometimes a person may not know that there is an issue, a potential issue or even something they need to take action on. With future systems information will be provided to stakeholders with all the artifacts they need to make a decision which does not necessarily mean they need to “do” the work. An example could be a weight engineer who is automatically sent information from the detail design model with a maturity level that is relevant to a weight engineer of a potential issue in a certain weight zone. The weight engineer will review the information provided and can make a decision without changing context (applications) to:
- Ignore the automatic error/warning
- Create a task for another team member to investigate and add additional notes
- Choose to solve the issue at that time.
With the dynamic concurrent workflow, teams will have the information available to them when it is at a level of maturity that they need. They will no longer need to wait for a static push which contains the information they need as well as other information needed from other departments allowing them to get information faster. An example is currently when a designer is building a package deliverable for a block it will contain information for the shop floor and the planning department as well as many other stakeholders. Since the information that the planner needs is only a subset of what is needed for the waterfront (ex. Annotations of details) the planner will be able to get the information they need when it is complete for them. This means they do not need to wait for the static push from the designer which includes a bunch more information not directly needed by the planner.
3. Synchronous Knowledge Aware Engineering
When a user is performing their task they need to refer to a lot of sources of information to make their decisions. Since there are a lot of sources it can be time consuming for a designer to reference all pieces of information created by different stakeholders.
The key to a synchronous system is that as the user is performing their action, it will refer the result of what is being done to information contained in other connected systems. If there is a discrepancy it will immediately tell the user in the current application they are using of this discrepancy. In certain cases it can also provide actions to take.
A couple of examples of this would be if the designer is modeling a frame and they accidently selected the wrong stock of a plate or stiffener. The synchronous system would compare the result of what the user did with the information that is in the classification drawings. It would provide a window in the CAD application and tell the user that the stock they picked does not match the classification drawing. It will then be able to provide the user an option to ignore or to change the stock.
The second example is to have the synchronous system check a rule based knowledge system. These systems will continue to gain and build on it’s knowledge using artificial intelligence and machine learning strategies. The workflow would be similar to when the user models a deck drain system as usual but if a rule is not met, (e.g. such as not extending a drain hole inlet a certain distance from the deck to account for the final surfacing) a window will be displayed about the error listing several actions the user can take.
Synchronous systems will find mistakes and provide guidance much earlier to users and this will save a company both time and money. It will reduce the requirement, or at least the effort involved with tedious checking and re-work that currently occurs weeks/months after the design was submitted.
Finally, the Future has an As Built 3D Model
As-built 3D models have been a topic of discussion for a very long time. There are several reasons we have not achieved this. In my opinion, we have not achieved this because as we are in the business of shipbuilding and not technology, the cost of generating and maintaining the As-Built model was not worth the benefit which would be realized. Notice I said “would be realized” not “could be realized.” This is an important distinction as I think if done right the benefits we can currently get from an As-Built exceed the cost. However, most companies today will not exploit or realize all the benefits of the As-Built because they believe the cost vs. benefit is too low.
In the future this will definitely change. There are several reasons for this:
- Context is King in the future
- Realization of benefit for production
- Digital Ship (aka. Digital Twin)
1. Context is King in the future
With the high frequency of information being exchanged it would be hard to interpret the information you are provided into actionable decisions without some visual context. Leveraging the 3D model and incorporating information in the model is a much faster way to communicate. You can communicate much more information with tremendous clarity compared to any textual method. I have blogged about this before Visualization of information is a powerful thing
2. Realization of benefit for production
The production floor will be reaping the benefits of the 3D model. I really, really want to say 2D paper documents will be gone but it is hard to say it. However, what I can say with confidence is that a digital representation of the ship will be used on every production floor. There will be various ways to access it possibly with some new technologies not even invented yet. Automation of shop floor machines will come directly from the 3D model which forces the 3D model to be 100% accurate. Because of the use of the digital model being used on the waterfront, shipyards will start gaining the benefit of keeping the model up-to-date. This additional benefit will encourage shipyards to invest more in maintaining an As-Built model and drive its adoption into the mainstream.
3. Digital Ship (aka. Digital Twin)
There is no argument that maintaining an as-built has additional costs. That is why I think that probably the strongest driver for as-builts will be the customer. As mentioned, future ship owners will need to have a better understanding of their asset and one way they will do this is with their requirement for a Digital Ship. The reason this is important and will push the generation of the as-built is because they will pay for it. You are right that they will try not to, but at the end they will fork over extra cash to get their digital ship because it will save them a lot of money during operations.
Generative Design & 3D Printing
Unfortunately, I did not have time to talk about Generative Design and 3D printing. The combination of these two can change the way we design our marine structures by allowing us to leverage new types of designs which before were not possible with current manufacturing techniques. I will plan to have a blog post on this topic sometime in the future.
Closing Remarks
The future sounds a lot like what many vendors say we have today. Some do a small portion and may require users to follow a specific recipe (order steps which cannot be deviated from). However, in the future, it will be much more fluid and systems will connect items more freely without requirements. The systems that will be connected are the ones we have today, but also include new systems, which, for example, will leverage artificial intelligence, machine learning and Big Data.
The improved seamless flow of information between the systems we use will allow us to evolve from a static concurrent environment to a dynamic concurrent environment. This will enable the ability to have access to the information we need at a much higher frequency. It will also provide other stakeholders the information we are creating to make decisions earlier and give feedback to our work.
Finally, there will be a move towards As-Built models. This has been a topic in shipbuilding since I can remember. In the past we were not able to achieve this mainly because no-one was driving this initiative. Owners did not want to pay for it and shipyards did not see the benefit from the additional effort. However, in the future the changes related to how we will work using the 3D model to provide the main source of context as well as the realization from the owners of the benefits of the digital twin will change this.
Blog Posts in the Future of Shipbuilding Series
- Future of Shipbuilding (15+ years)
- Future of Shipbuilding: Engineering Design
- Future of Shipbuilding: Detail Design and Production Planning (Part 1)
- Future of Shipbuilding: Detail Design and Production Planning (Part 2)
- Future of Shipbuilding: Manufacturing (Part 1)
- Future of Shipbuilding: Manufacturing (Part 2)
- Future of Shipbuilding: The Journey Forward