We had the opportunity to welcome Andrew Taylor, Managing Director of Southerly Designs at our Victoria, BC HQ while Andrew was en route to visit a local client. Southerly has been an SSI client for almost 20 years, and designed over 250 vessels using SSI ShipConstructor. While at our office, Andrew gave us his take on Southerly Designs, technology innovation, the Australian shipbuilding industry, and how we can continue to improve our solutions.
SSI: Thanks for joining us today, Andrew. To start, could you give us an overview of your current projects and explain what your team is working on?
Andrew Taylor: We have a small team, just six people, but we’re handling about 25 projects. We’re working with about half a dozen shipyards in five different countries. We specialize in in high-speed and medium-speed aluminum monohulls, though we’ve ventured into catamarans and some steel vessel work. The primary focus, however, remains on aluminum monohulls. In terms of scale, our projects typically range from 5 to 50 meters. For instance, we’re currently working on a variety of small rigid inflatable boats (RIBs) for sea rescue organizations in Australia, ranging from 7 to 12 meters, and similar vessels for police use. We’ve also recently completed a research vessel for the Department of Fisheries. We’re also working on a 25-meter large patrol vessel, the SO25, which is designed for long-range operations but mostly operates closer to shore. Our activities extend to constructing fishing boats and oil and gas crew boats in Southeast Asia, handling structural designs for luxury catamarans, and small patrol vessels for the Tanzanian government with a Kenyan shipyard. We also get a fair amount of upgrade and modification work and new stability analyses.
SSI: With such a small team, how do you remain competitive against larger firms?
AT: Our competitive edge largely comes from our responsiveness and the foundational philosophy of our company, which was started by a lifelong fisherman who turned his practical experience into a boat building business. This close understanding of design, construction, and operation, focusing on high-performance rather than purely financial outcomes, allows us to remain agile and innovative. Our operations are streamlined, allowing us to quickly adapt to market needs and technological advancements, which is crucial when competing with larger, more bureaucratic organizations. On another side, again from our heritage, our historical focus on the lobster fishery in Western Australia has pushed us to the forefront of aluminum boat building technology. Those guys have always been at the forefront. New boats, best technology. It’s ensured we’ve pushed the standard in aluminum boat building.
SSI: Speaking of operations, you’ve been using SSI solutions and ShipConstructor for quite some time. What has made that relationship successful, and what’s kept you using ShipConstructor over all these years?
AT: We adopted ShipConstructor following a recommendation from one of our shipbuilding clients who was impressed by its capabilities. This was probably around 2005. This software has become integral to our operations, particularly because it enhances our structural design and detailing processes. Before adopting ShipConstructor, we primarily used Maxsurf for our modeling and detailing, which was effective up to a point. However, ShipConstructor offered more robust features for managing detail, Bill of Materials, and parts numbering, which significantly streamlined our interaction with shipyards and reduced the overall project timelines.
We never really saw the need to explore other options. I spoke to others in the industry and showed them what we did in ShipConstructor. They replied by saying “We can do all that with SolidWorks. I just have to write some macros.” Meanwhile, it’s already built into ShipConstructor.
The software’s focus on structure rather than outfitting aligns well with our work, particularly since we deal with relatively small aluminum parts compared to the larger, heavy-duty items it’s also capable of handling.
SSI: Are there any new technologies or areas of innovation you’re exploring to stay ahead?
AT: Yes, we’re actively exploring advancements in our design and production processes. Although our core focus remains on structure due to our specialization, we’re increasingly interested in expanding into outfitting and pipe work as these elements become more relevant to our clients’ needs. We’ve recently taken on using Rhino, and we still use Maxsurf for hydrostatics and stability analysis. We are able to connect them with ShipConstructor and push things forward.
Additionally, as technology evolves, we’re also considering how we might integrate more advanced digital tools and possibly even virtual reality into our processes to enhance project visualization and client engagement.
SSI: Have your clients expressed interest in virtual reality simulations for your designs?
AT: There is growing interest in virtual reality, especially from clients who are eager to see early-stage visualizations of their projects. While this technology is exciting, our approach remains pragmatic. Due to the cost considerations and the nature of our projects, we typically reserve detailed VR simulations for later stages or for projects where the budget allows. More commonly, we would provide still renderings as a more cost-effective method of project visualization throughout the design process.
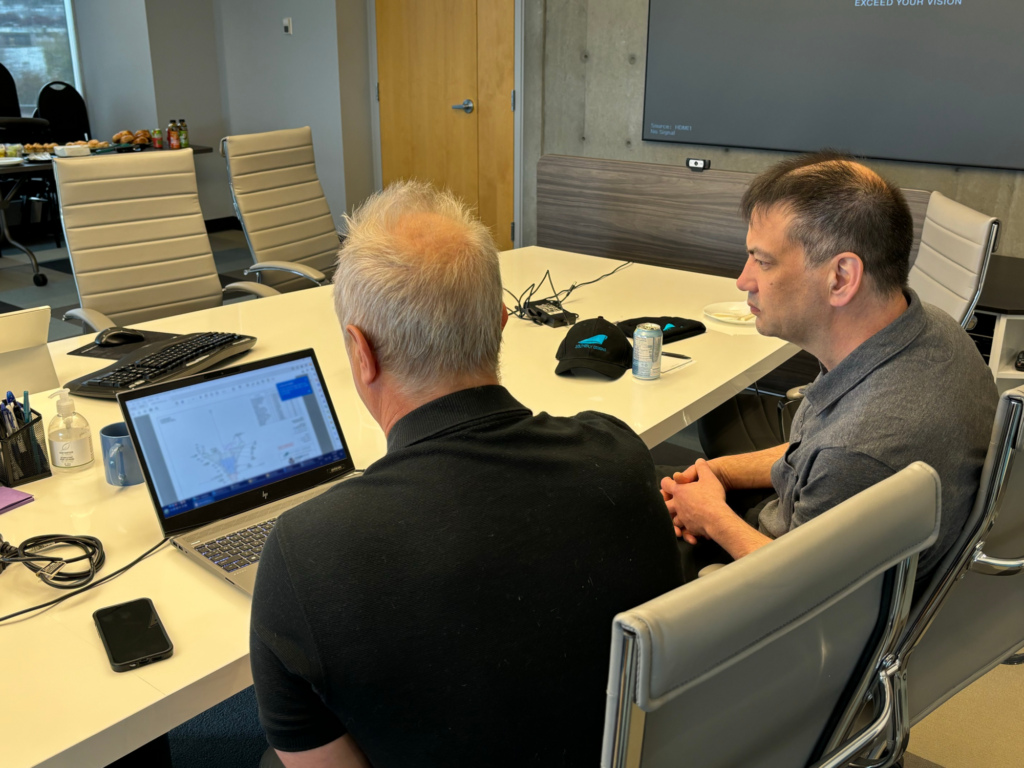
SSI: Considering the variety of vessels you build, do you often reuse past designs, or do you prefer to start from scratch?
AT: We treat each project as unique. Given the diversity of our portfolio, which includes everything from small, agile RIBs to large patrol boats and sophisticated crew boats, there’s rarely an opportunity to reuse past designs without significant modifications. Starting from scratch allows us to tailor every aspect of a vessel to the specific needs and preferences of our clients. This way we can ensure optimal performance and satisfaction, although it demands a higher level of creativity and technical expertise from our team. In our case, we would typically be redoing 75% of an existing vessel.
SSI: Finally, how do you view the current state of the Australian shipbuilding industry, and what impact does it have on your business?
AT: The Australian shipbuilding industry is currently experiencing a wave of enthusiasm, particularly for naval shipbuilding. There is a growing realization that projects need to be executed cheaper and quicker. It’s clear they need to look more to the local industry. For our niche, such as RIBs and other small vessels, this has opened new opportunities that were previously overlooked in favor of foreign designs. This growth also presents challenges with attracting and retaining staff. As more projects ramp up, especially large-scale naval contracts, finding graduate naval architects and marine draft personnel becomes increasingly difficult. Despite these challenges, we’re focused on leveraging our niche expertise and maintaining a steady flow of projects through government and private contracts.
About Southerly Designs
Southerly Designs is an innovative naval architecture and marine design consultancy based in Port Denison, Western Australia. Southerly Designs has been at the forefront of high speed aluminium vessel design since foundation in 1997. Drawing on over 60 years of experience in designing, constructing and operating fast commercial vessels, our professional and dedicated team has forged an enviable reputation for producing robust vessels that are practical, handle well even in extreme conditions, are fuel efficient and offer comfort without sacrificing performance.