チャレンジ
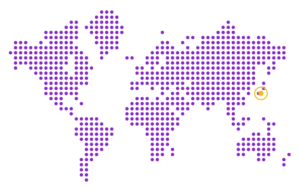
常石グループの一部である三穂造船所は、100年近く漁業、政府、貨物、専門船を建造し、合計で1,400隻以上の船舶を建造してきました。 造船所は、品質、技術的な洗練、多様な船舶での経験、コスト競争力に対する評判のおかげで、数多くのシップ・オブ・ザ・イヤー賞を受賞しています。
三保はきわめて品質の高い船舶を製造しているにもかかわらず、非効率で旧式のシステムとプロセス で作業しているという課題に直面しました。 三保が直面している課題の一つはネスティングです。
既存のプロセスでは、半透明の紙に部品を印刷してから手動で切断し、マットフィルムに貼り付ける必要があります。 MihoがNC切断機自体にデータを入力すると、データはフロッピーディスクに転送されます。 基盤となるシステム(SHIP SYSTEMとCAMSR)とハードウェアはライフサイクルの終わりに達しており、代替ソリューションが必要でした。 この新しいソリューションは、品質を犠牲にしたり、既存のプロジェクトを危険にさらすことなく、船体生産設計のすべての機能的側面の改善を示すために必要でした。 さらに問題を複雑にするために、船体の設計は2Dで外部委託され、完了し、下流の多くのプロセスはまだ2D図面を必要としました。 実装されたソリューションは、既存の2D情報をシームレスに取り込み、以前のように詳細な2D図面を出力できる必要があります。
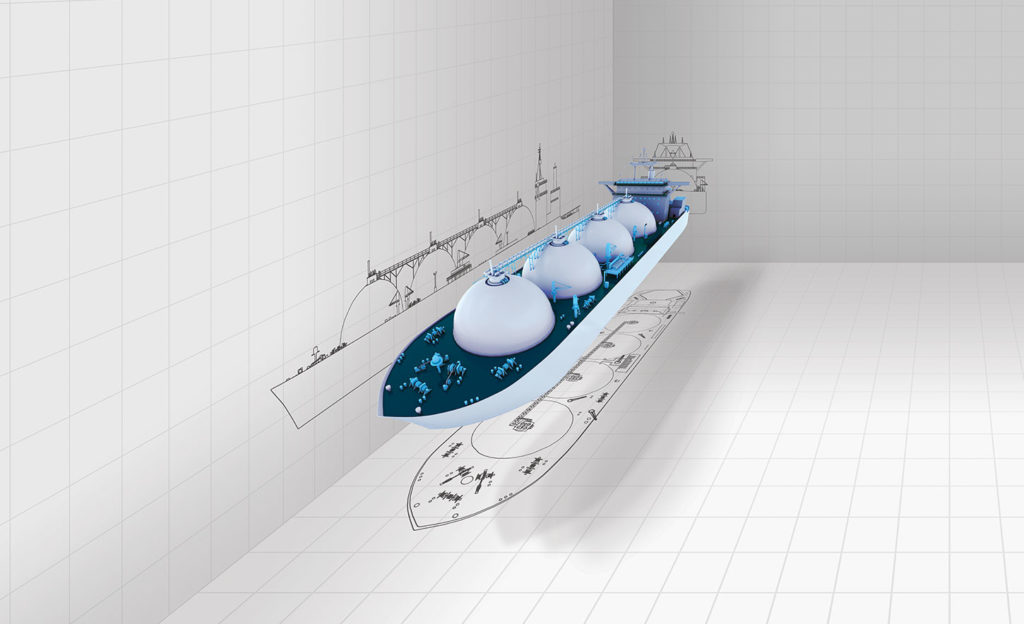
ソリューション
三保は次世代のシステムを探すのが喫緊の課題であることを理解し、多くのソリューションを評価した 後、2010年にその第一の船殻製造設計ソリューションとしてShipConstructorを導入しました。 3Dの明 らかな利点は一目瞭然でした。しかし、考慮すべき重要な点は実施されたソリューションはすぐに、しか も進行中のプロジェクト や確立されたプロセス を中断することなしに導 入される必要があるとい うことです。
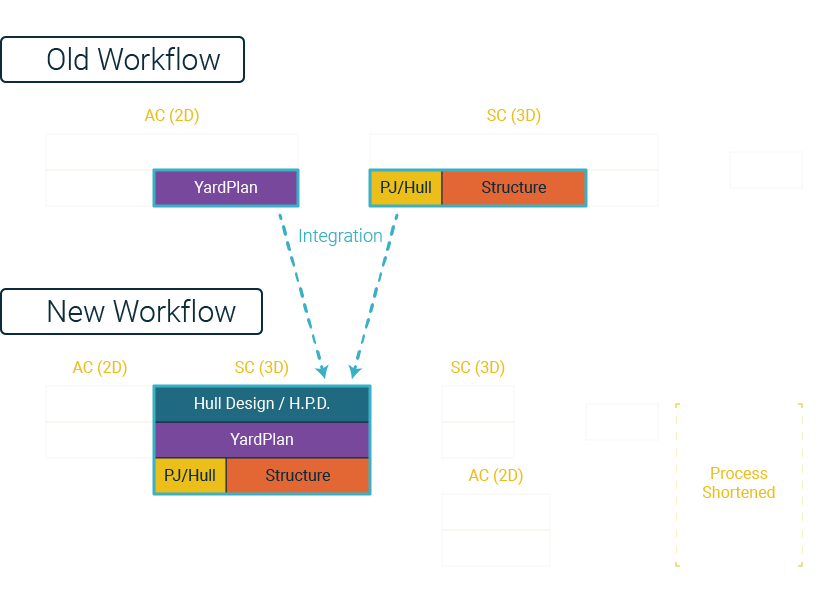
結果
以下の完全なケーススタディをダウンロードして、2Dおよび3D ShipConstructorソリューションの増分実装の前後のMiho造船所のプロセス、Mihoがコストを削減し品質を維持した方法、およびそれらがどのようにしてメリットを獲得したかに関する詳細情報をご覧ください。