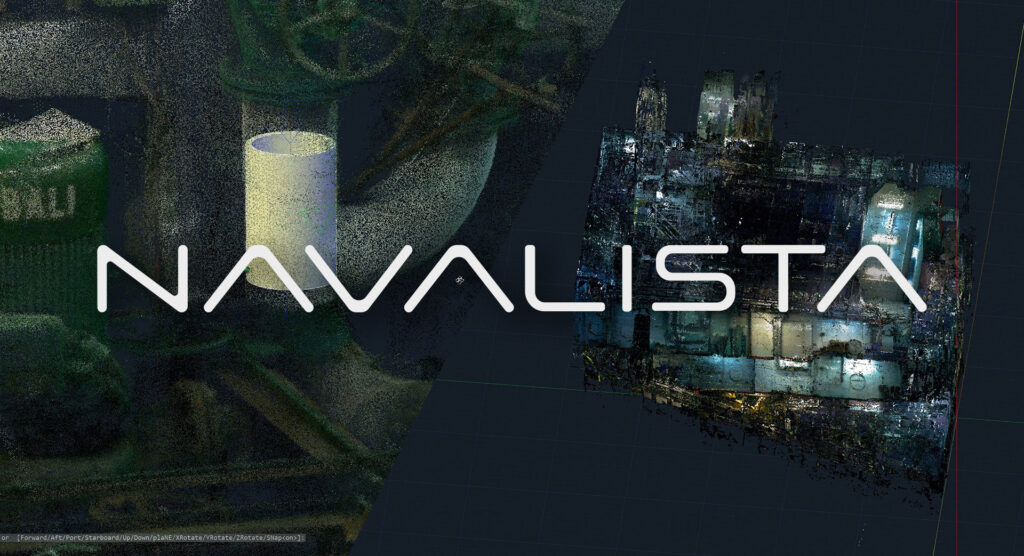
Every day a vessel is in drydock is a day of lost revenue for the ship’s owner. Minimizing the time a ship is off the water is becoming even more important to solve as ships have longer service lives and require an increasing number of repairs and refits to meet environmental and other regulations. Navalista is a Ukrainian-based global marine design and engineering firm that has become known as an expert in helping to minimize the amount of time a ship is in dry dock by using 3D Scanning as part of their repair and refit workflows.
Reducing time in drydock
With measurements, a complete design, and materials ordered and ready at the shipyard before the vessel comes in for a refit, downtime is reduced to a minimum. 3D scanning and reality capture, in combination with their ShipConstructor design workflows, allow Navalista to travel to the vessel, quickly and accurately capture the as-is state of the vessel, and then complete and share the design work with the shipyard far earlier than is traditionally possible.
Why 3D scanning?
In terms of repair and refit, ships usually do not have drawings or documentation, let alone 3D information, available to the designer and shipyard. When the information does exist, the realities of ship construction mean that the ship on the water usually differs from any as-built information.
Traditionally, teams of specialists would need to board a vessel and manually take measurements on the ship, requiring a significant time investment and individuals highly skilled in this specific task. The checking, rechecking, fitting, and refitting of designs that rely on traditional measurements and techniques meant the ship was out of service for longer, at significant costs to the owner and operator.
As Navalista saw, 3D scanning is a cost-effective way to accurately capture the ship as it sits in service and allows the designer to develop the design and make changes rapidly and with less error.
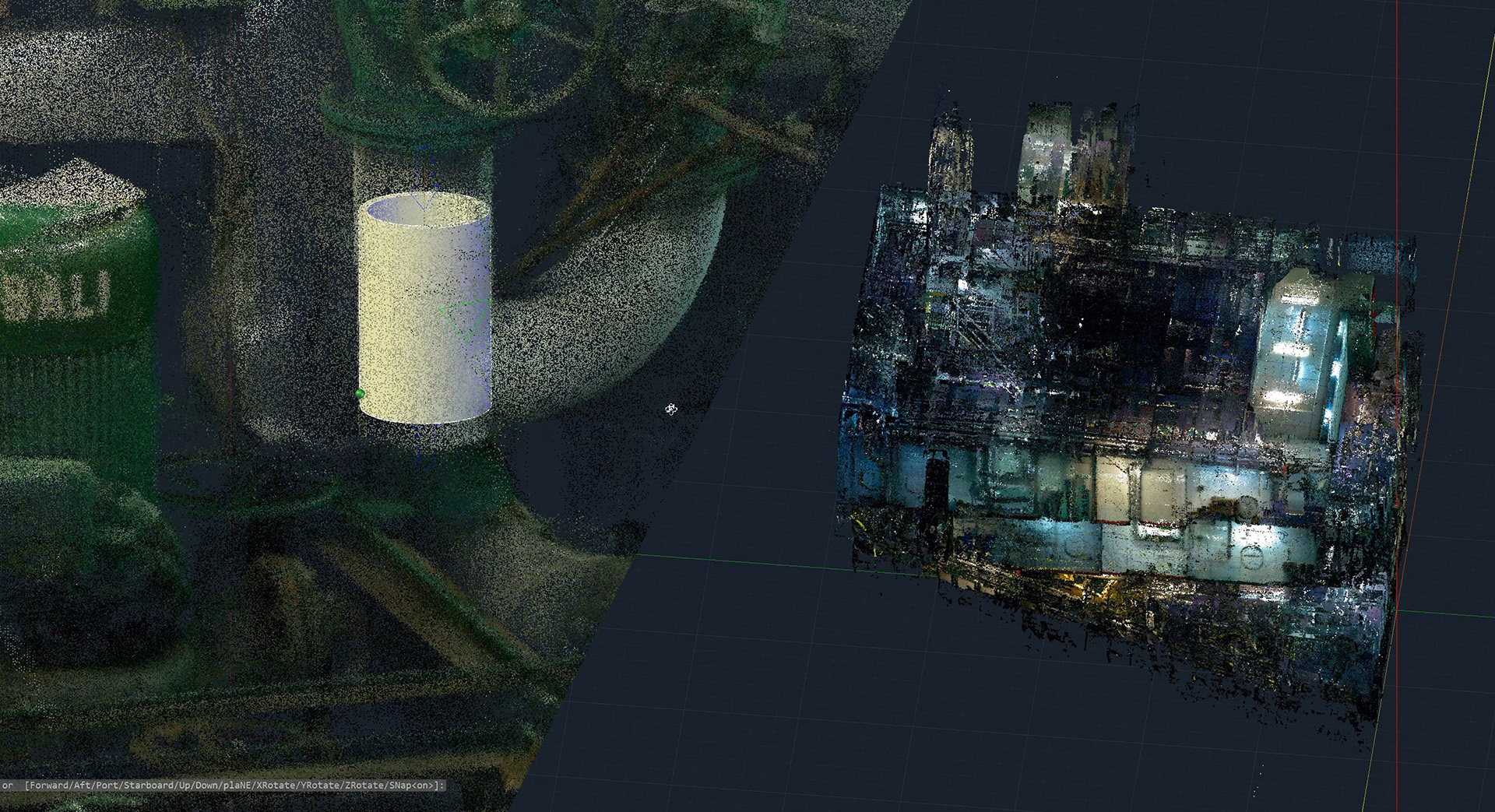
It was easy to get started and use 3D scanning. We have completed close to 50 projects with ShipConstructor and 3D Scanning, and, at this point, my team can’t go without it.
Oleksandr Vasyliev, Technical Director, Navalista
How Navalista implements 3D scanning
Many scanners are available, and, depending on the project’s demands, Navalista uses a combination of Faro and Leica scanners. Compact scanners would be more suitable for tight spaces, for example. The team generates a point cloud in .rcp format using the scanned data and then imports it into the ShipConstructor project. It was easy for the team to get started since point clouds and .rcp files are supported natively in ShipConstructor as first-class citizens.
Only what is needed for modification is modeled to save time, such as existing piping, pumps, and cuttings. Once the model is complete, the team checks for clashes between the point cloud and modeled modifications in ShipExplorer. This ensures that all components of the design work together as intended.
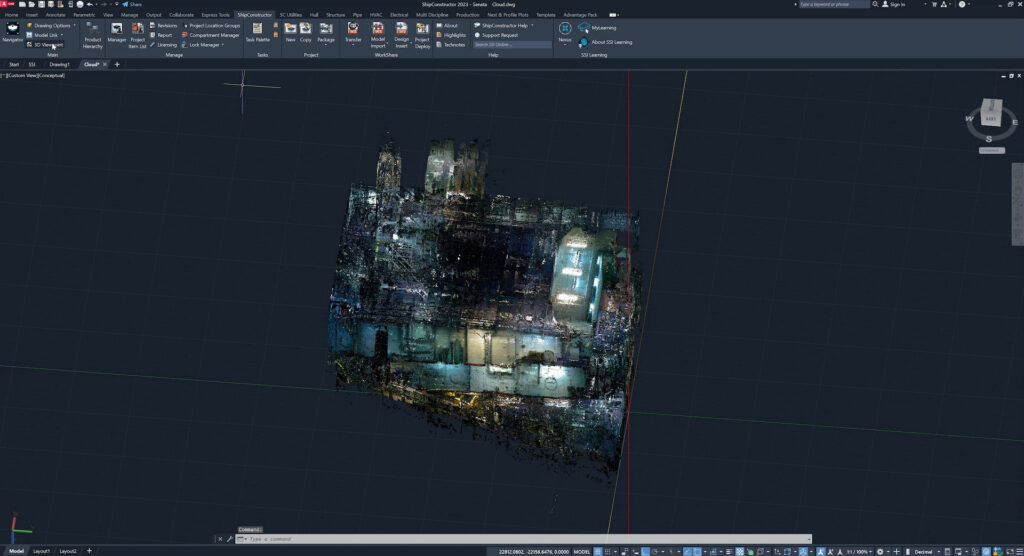
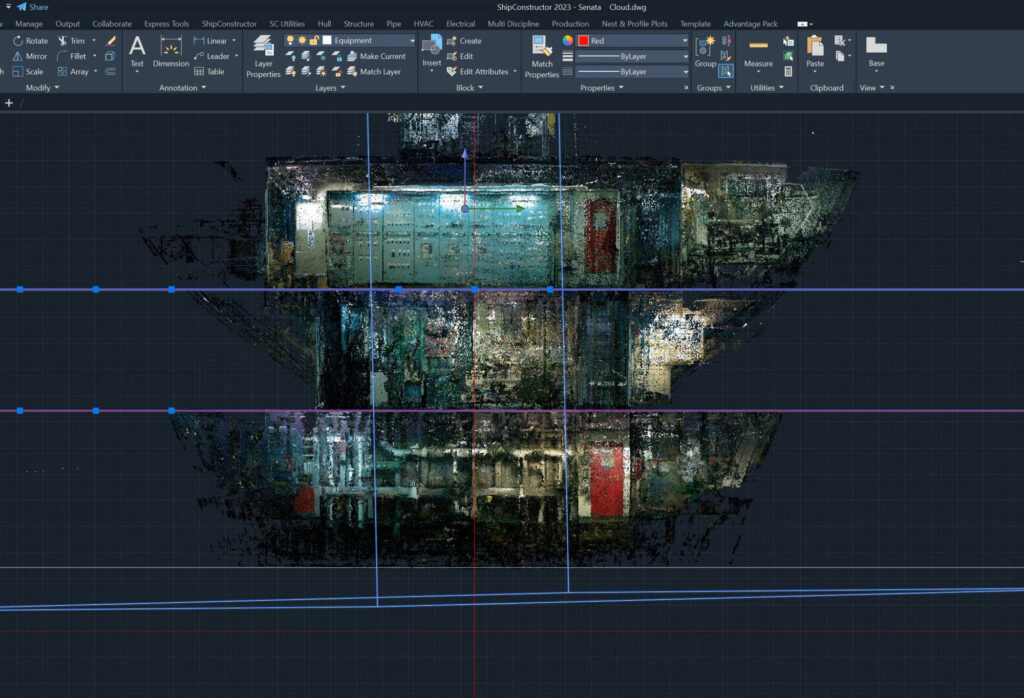
Modeling on top of the point cloud in ShipConstructor lets the Navalista team automatically find pipe centers, easily validate the point cloud against existing drawings, and model with less than 5mm error.
Navalista connects all its disciplines with the point cloud. “It’s easy because, in the database, we just link to the point cloud and can work separately with the same information,” said Oleksandr Vasyliev, Technical Director at Navalista. By using the same underlying point cloud for hull, structure, piping, electrical, cable routing, and any other discipline, the team is confident that the end design will work.
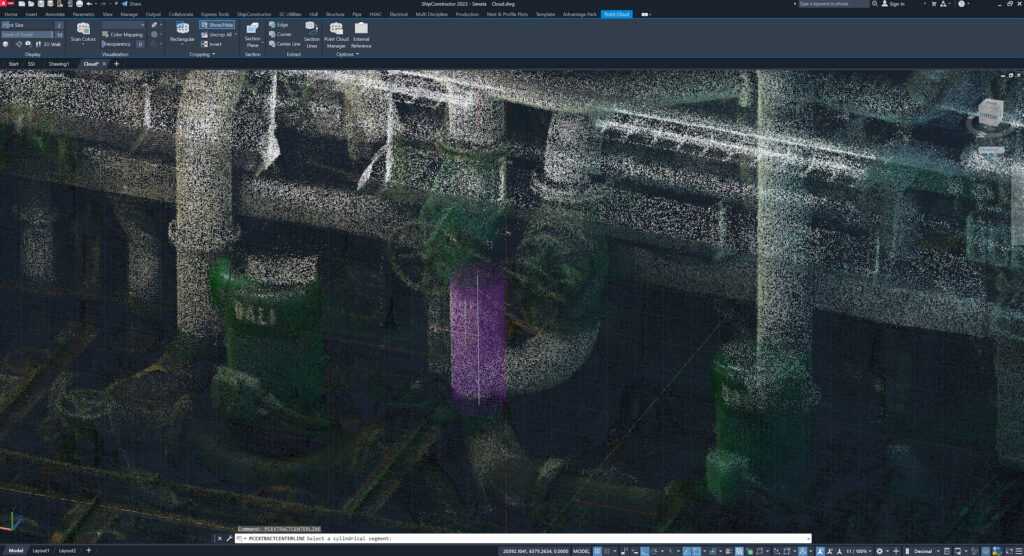
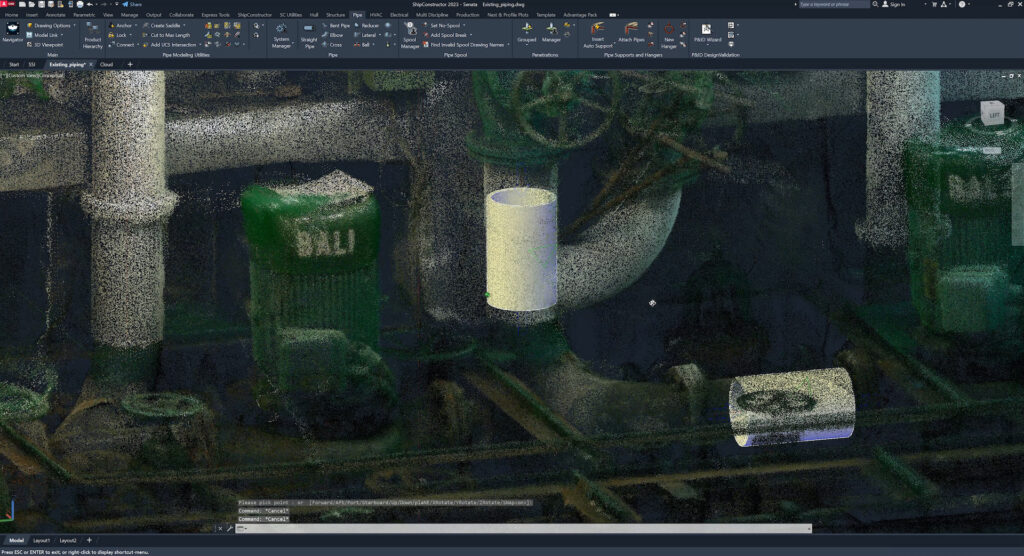
Results
“For us, the main benefit of 3D scanning is time savings,” said Oleksandr. “But the quality of our designs is higher than before, and we are becoming known and sought out for that. Clients see that investing in an accurate, high-quality design upfront saves them money.”
Quickly and accurately performing scans lets Navalista take advantage of time, labor, and cost savings while simultaneously producing higher-quality retrofit designs that allow the shipyard to procure materials and prepare for the refit before the ship arrives. The shipyard can start the installation immediately, without rework risk, and turn the vessel around faster.
The shipbuilding-specific capabilities of ShipConstructor, combined with a native and open ability to consume and use point clouds, made the combination a natural choice for Navalista. “In the future, we will always proceed with 3D scanning first,” said Oleksandr. “There will always be a new problem in shipbuilding where 3D scanning is necessary.”
In short, implementing the 3D scanning workflow:
- Reduced the need for measurement experts.
- Lowered the long-term costs associated with measurement.
- Improved the accuracy and precision of captured measurements.
- Reduced the time vessels have to stay in drydock.
About Navalista
NAVALISTA is a professional Consortium of international independent companies with different business directions – united to serve the Global Maritime Industry. NAVALISTA’s main business activities include but are not limited to:
- Technical, Design & Engineering Services for Water Transport;
- Ship’s Condition Related Surveys;
- Ultrasonic Thickness Measurement (UTM);
- Inventory of Hazardous Materials (IHM / HAZMAT);
- Ship Emergency Response Service (SERS);
- 3D Scanning Surveys.