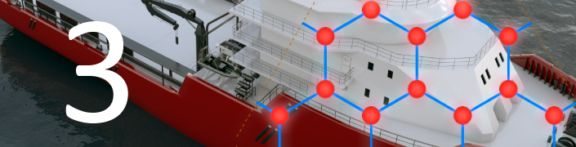
Certain clients and markets perceive ShipConstructor as a product primarily for production design. In many ways this is a self-fulfilling prophecy. Those that only use ShipConstructor for production design rarely bother to put much effort into the creation of a model that can adaptively respond to more macro level changes. The benefits of such a model are reduced in the short term, and for some this decision is the one that makes sense. However as a result they are seldom exposed to the capabilities that do exist and perceive the product as lacking those capabilities. Additionally, those who were trained and experienced with ShipConstructor 2005 or older versions – versions that didn’t have these capabilities – brought many of their practices and processes with them into newer versions.
Those that use ShipConstructor solely for basic design or for both basic and detail design know well the capabilities that can be used to create a model that helps to manage and control change. Like every other product there are areas where ShipConstructor shines when changes occur and areas where a more focused effort is required. It comes down largely to the way the model is created and the degree to which the capabilities that do exist are exploited.
First let’s explore the major types of relationships that can be created in a ShipConstructor product model:
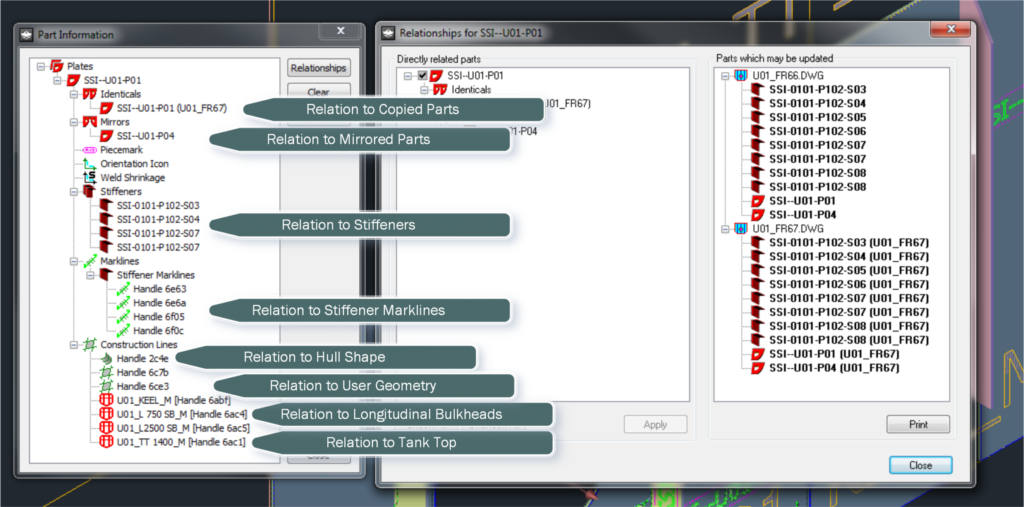
- Stocks/Libraries/Standards to the 3D model – All standards are associatively related to the 3D model. Changes to standards (endcuts, stocks, profiles, cutouts, marking styles, piecemark styles, flange standards etc… etc…) are automatically reflected in the 3D model.
- Construction lines to parts – these lines form portions of the boundaries of one or many parts, stiffener mold lines, marking etc… The relationship to all parts is associative and changes to the lines are reflected in all parts. Construction lines may be user defined, defined by the offset of another construction line, defined by the intersection of one location (frame, deck, longitudinal, arbitrary) and another, or defined by the intersection of the hull shape and the mold plane for a specific planar group (location).
- Copies of construction lines – construction lines can be copied resulting in an associative relationship between the two lines (and any other copies or lines related to the copies – this is a sibling relationship not a topological parent-child relationship)
- Mirrors of construction lines – construction lines can be mirrored, not just in one or two major directions, but about any plane. This results in an associative relationship that respects that particular transformation
- Offsets of construction lines – one construction line can be offset from another. The relationship between the two lines is associative (changes to one can be reflected in the other, while respecting the offset) and the offset parameter can be changed
- Construction lines and corner treatments on plates – corner treatments (snipe, scallop, fillet) applied to plates are inserted on the boundaries of the plates and are related either to the intersection of multiple construction lines or to a point in the parameter space of a single construction line
- Locations (datum lines) and plates. This is an associative relationship between the location groups in the project and the plate. The location groups are marked on plates automatically and update as changes are made or the plate is moved.
- Stiffener intersections (and cutouts) through plates – wherever a stiffener intersects a plate (at any angle), cutouts –defined by rules – are inserted in the plates. This is an associative relationship between the stiffener, the plate, and the cutout type (tight, non-tight, user defined)
- Stiffeners attached to plates – Any stiffener attached to a plate remains associatively linked to the plate and responds to changes to the plate like throw direction and is carried along with copies or mirrors of the plate. This is an associative relationship between the stiffener, the plate, the markline style used to mark the plate, and the construction line forming the mold line of the stiffener.
- Faceplates attached to plates – Any faceplate or rider bar attached to a plate remains associatively linked to the plate and responds to changes to the plate like throw direction and is carried along with copies or mirrors of the plate. This is an associative relationship between the faceplate, the plate, the markline style used to mark the plate, and the construction line forming the path of the faceplate.
- Plate flanges to construction lines – When a flange is added to a plate it is added to a portion of the boundary of the plate related to a construction line. This results in an associative relationship between the flange standard and the plate part with a parameter on the boundary of the plate that determines the section to retain the flange as changes occur.
- Copies of parts – When a part is copied an associative relationship is created between the parts, and separate relationships are created between all sub-geometry of the copied parts. This relationship extends to all other copies as well, and through them to mirrored parts and more. This is not a parent-child topology and changes to any one part can impact all others (or not as the user chooses). Even if the parts themselves are no longer identical the sub-geometry relationships allow changes to propagate.
- Mirrors of parts – When a part is mirrored (about any desired plane) an associative relationship is created between the parts, and separate relationships are created between all sub-geometry of the mirrored parts. Even if the relationship between the parts is broken the sub-geometry relationships allow changes to propagate.
- Penetrations in structural parts – Penetrations caused by systems in the product model are an associative relationship between the plate(s) they have been created through, the penetration standard that was used, and the system parts that caused the penetrations. The size of the actual penetration and resulting components (collar, sleeve, doubler…) is parametrically derived from the dimensions of the system parts.
- Planar groups (frames, decks, longitudinal bulkheads) to other planar groups – the result is an associative relationship between 2 planes, 1 in each planar group, and a construction line in the group that will be used to define portions of the 3D product model. This geometry is updated whenever one of these planes is moved (for example a plane 15mm from the mold plane for the group is changed to be 10mm instead, or an entire planar groups is moved (i.e. a bulkhead location is changed).
Provided the relationships outlined here are employed, and employed wisely, the result can be a responsive product model that will adapt well to change for the basic design and throughout the life of the model as it transitions into later phases.
Best Practices
So we’ve seen that there are a fair number of relationships that can be built into a ShipConstructor product model and that these can be beneficial at any phase of design and engineering. However creating the right relationships in the right way requires some forethought. Unfortunately the deceivingly simple way in which many of these relationships can be created makes many users underestimate the abilities they have and the impact of the relationships they create.
It turns out that the easiest way to create geometry in ShipConstructor is simply by copying, mirroring and offsetting existing geometry by using native AutoCAD commands like copy, mirror and offset. These create relationships in the ShipConstructor Marine Information Model. Selecting a boundary point on a plate using the Nearest OSNAP or the Intersection OSNAP (intersection of two construction lines) to insert a corner treatment (scallop, fillet, snipe) will create two different types of relationships. Simply defining plate parts in a frame when a deck has been used to create a construction line in the frame will create a relationship between the parts in that frame and the height of the deck. Many of these relationships are created so easily that users seldom think of them: and that can sometimes be a problem in situations where a responsive model is important.
I had originally had started down a path where I was going to describe the differences for using ShipConstructor for basic and detail design. But in hindsight, what I was really going to describe would not have been best practice, but the best of the common practice. Instead let’s look at a few guidelines that apply across the board:
- Model the big relationships, always. In some ways this is obvious. But as an example many users use the intersection of geometry and solids from other planar groups rather than using the group plane construction lines. It seems easier and it is how they worked in older versions. These make great checking and reference tools but should not be used to form the boundaries of parts that would otherwise be related to a frame, deck, longitudinal or any arbitrary group. The types of relationships that should always be employed when possible include:
- Group plane intersections
- Stiffener cutouts in plates (as opposed to user geometry added to plates)
- Corner treatments (as opposed to user geometry added to plates)
- Mirror, copy, at the part level, even if they are to be broken later. (the sub-geometry relationships are crucial)
- Cut the model some slack. As changes occur the geometry in the model needs room to move and grow. If the geometry used has been cleaned and trimmed to a point that the changes can’t grow into it you will cause yourself more work when those changes happen. Leave some slack in the geometry and resist the urge to clean up too much.
- Make decisions on how smaller relationships will be dealt with for that project, and more importantly communicate these across the team. The model should respond intuitively no matter who is making the change. For example, when working in a frame do you mark the mold plane and thickness plane of continuous longitudinal bulkheads in the frame (plates in the frame on either side of the bulkhead will be associatively connected to the appropriate planes in the bulkhead) or do you mark just the mold plane and offset that construction line (remember this is also an associative relationship) to get the association to the thickness. Either of these approaches brings benefits, but you should know how you want the model to be created and ensure everyone follows the same process.
In Summary
Starting in part 1 of this series of posts we discussed the types of change that occurs in the earlier design phases and the different strategies various types of tools use to help users manage that change. In part 2, I described the philosophy SSI applies to our products when creating capabilities that help users manage change. And finally, here in Part 3 we looked at how ShipConstructor specifically allows users to create responsive models, and some guidelines on how to approach doing so yourself. In the end the capability is there, and it is what you make of it.
Post Comments
“Changes to standards (endcuts, stocks, profiles, cutouts, marking styles, piecemark styles, flange standards etc… etc…) are automatically reflected in the 3D model.”
Its refreshing to hear that SC has finally added these capabilities. In old versions, once a pipe catalog part was in use there seemed to be no way to modify its geometry to refine details. We faced a similar challenge with penetrations. Once they were applied, they could not be modified to facilitate changes to reconfigure for sisters ships. Glad this obvious shortcoming is finally fixed.
I’m genuinely impressed by the quality of your blog – it’s informative, engaging, and incredibly well-written!