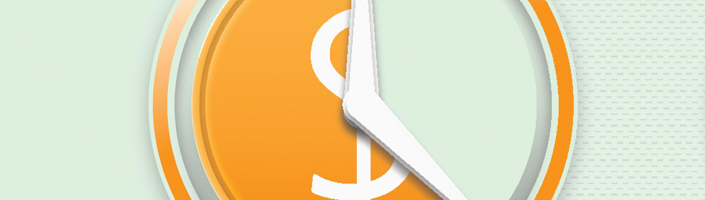
In my first article, Bill of Material Management, From an Engineering Perspective, we looked at how Best-in-Class organizations differentiate themselves by understanding how data transfers throughout their organization. In today’s article, I will look at ways to evaluate your current environment and HOW you can manage your process and the Information that travels through it. In the manufacturing world, the Bill of Materials (BOM) is often considered the most important aspect of manufacturing and assembling products. Engineering, purchasing, manufacturing, and assembly all work off this information. My goal in my first article was to challenge readers’ current thought process so that they could get a better grasp of what was driving their organization. Clients have often asked me what makes Best-in-Class organizations different. My answer may sound a bit basic, but it’s that they “truly” understand how their products are designed, manufactured, assembled, and shipped. (I bet you thought I was going to have a fancy, highly technical answer!)
What I really mean is they understand the process so well that they can break down the time and costs associated in every part of the process. They are the first ones to tell you what I explained in my first segment, that the BOM is an output from your Product Data Model. Instead of the BOM being the most important, the Product Data Model, or content creator, is what leads all changes and automation. They not only understand the many engineering changes they process in a given year, but the root cause and monetary effect of these changes. And yes, in the words of my Economics professors, “Time is Money.”
If someone is doing a manual task, let’s say manually entering a BOM into their inventory management system (ERP – Enterprise Resource Planning or MRP – Material Resource Planning), then they are costing the company time. Therefore, they are adding to the overhead of the overall project.
For today’s discussion, let’s assume that you buy into the idea that your content creator – in our case the ShipConstructor product data model – is the source for up to date BOMs, AND that the more time you spend doing a task, the more it pulls from your bottom line. We’ll assume that your data entry person is perfect at their job. You are still left with the manual tasks of initiating changes, making the changes, and then communicating the changes out to the necessary parties.
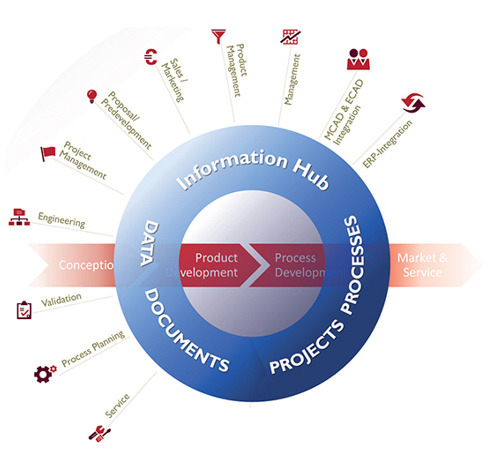
But where do we go from here? You NEED to map out your process to see where to start and where to find the manual portions of your process. I first recommend a technique that we used in my previous life. We would use advanced technology and do mapping exercises on .….. a Whiteboard! It is important to map out processes early to get a big picture view on how your organization operates, without discussing the individual systems you already have in place. For shipyards, this a much more daunting and time consuming task but one that pays huge dividends. (SSI provides complimentary preliminary process mapping services through a structured BPA – Business Process Assessment). During this exercise, you identify precisely HOW and WHAT information passes from one department to the next as well as WHEN it is needed. Once you are able to map your process, including engineering changes, you’re then able to identify workflows between platforms (Eng. & Design, ERP, MRP, PLM, PDM, etc.) compared to current processes that flow around these platforms. It is not uncommon to identify significant processes not covered by ANY of your current systems (which by definition are largely error prone, time consuming manual processes).
What are the top 3 manual aspects of your business that can see improvement through automated control?
- Controlling Engineering Changes – Controlling HOW changes are initiated, HOW the change is made, and HOW the change is communicated to all affected parties.
- Accurate Vendor Furnished Information (VFI) for Purchasing.
- Driving changes to shop floor/Shipyard.
But how do we manage these processes and corresponding information?
At this point you can start evaluating your current systems. The goal of having an effective “Best in Class” system is to eliminate the manual process and this is where time-savings start to add up. Your organization most likely has CAD, ERP, and CRM systems in place. But how many times are you still manually inputting BOMs into these systems? How many times are changes made on the shop floor and not communicated back to your BOM or engineering data?
The good news is that you can very likely improve all of these areas using the tools you own today. Remember when we said that the data creator (in our case ShipConstructor) is the most important part of the process? Your data model is created in ShipConstructor which includes your manufacturing drawings, your mechanical and electrical BOMs, and even nesting programs. If this information is the output from ShipConstructor, can we use it to improve the manual processes in the other departments of the company? Simple answer: Yes. (For more information on PLM in Shipbuilding, check out Denis Morais’ article on Waveform).
ShipConstructor information can be utilized in other company systems that need updated information once changes happen. Your BOM, or VFI (Vendor Furnished Information), can be automated so that everyone has a single source of truth. You can connect this via SSI’s Enterprise Platform, our output tool that allows you to connect to your ERP or PLM systems.
Simply put, since your information is already in ShipConstructor, let the tool do the work. Depending on what output and content you need across your organization, we might recommend different tool sets that move your process into the PLM arena. Remember back to when you had to manually design your ship on paper, then create a BOM to match the parts you just designed? Remember when they finally created a CAD tool that could automate this process? We are now in the age of being able to manage your process virtually, so that you can have one source of truth and truly understand the time between each stage in your process.
Post Comments
thank you Jason, very easy yet very rich reading