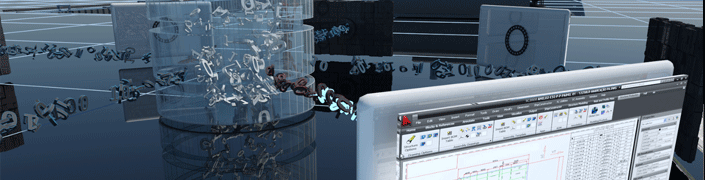
I’d like to dissect one of the most complicated processes any manufacturing environment faces in designing, manufacturing, and building their products. As most people know, the Bill of Materials, or BOM, is the most essential piece of information that any product development and manufacturing company has to have. Effective BOM management allows you to have shorter lead times, less errors in manufacturing and assembly and in the end, reduces the “Cost of Doing Business.” One of the common misconceptions I’d like to discuss is the belief that you need to do business a certain way because of the tools you own.
In 2007, the Aberdeen Group, a consulting agency specializing in evaluating manufacturing organizations, reported that Best in Class companies are 50% more likely to “leverage centralized product repositories” to capture and control the information consumed within the organization.
As someone who has worked with Best in Class organizations and has been involved in the systems used in these complex manufacturing environments, I’d like to break down the key components that are making them successful.
BOM Management in Best in Class Organizations
So what are these best in class organizations doing differently? Are they using different tools that we don’t have access to?
Best in Class organizations understand what goes into the design and manufacturing of their product. They pay more attention to the time and costs associated with each aspect of the process. In doing this, they’re able to further utilize the “central product repositories” such as CAD, PDM, PLM, and ERP to help make them more efficient, not slow them down. If BOMs are the most important aspect of manufacturing complex products, shouldn’t we strive to find the most effective way of managing them?
To start the process, let’s go back to basics in understanding your BOM:
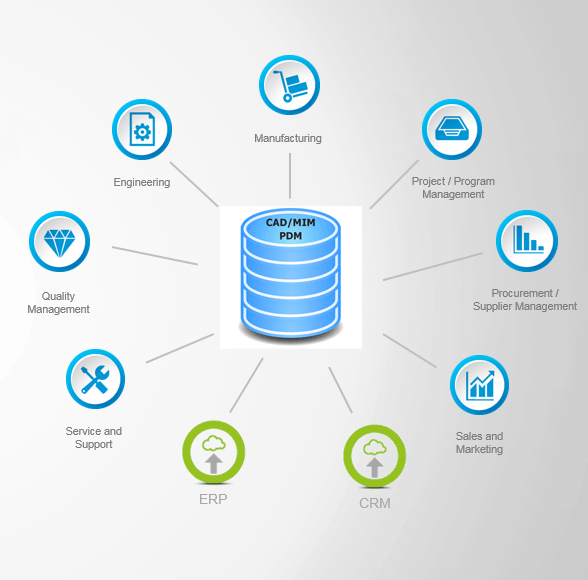
How it’s Created
BOMs are created by your engineering tool, right? Does this really answer HOW they’re created?
In a complex manufacturing environment, say heavy equipment, machine design or shipbuilding, the process starts far before the design engineers get their hands on the projects. For our shipbuilders, project managers, salespeople, and naval architects are working off previous projects to help create the new concept for the project. They must have access to old designs and concepts so that they can effectively portray their ideas to help solve their customers’ needs. This is essential as more often than not, the process is happening before any monetary commitment is made from the customer or client.
After commitment, Engineering gets involved to finalize the design so it can be manufactured. Their Product Data Model, created in CAD, now becomes the most important piece of information in the organization. Why? Because modern tools use the Product Data Model to create your BOM.
Misconception #1: The BOM is just an Excel spreadsheet with the parts used in the project.
You will see the importance when we start recognizing how changes affect the entire process. The importance of the Product Data Model is shown in the growing interest in MBE (Model Based Enterprise) processes. See more on this from a previous article from SSI CTO, Denis Morais.
How it’s Changed
We’re now at that point in the conversation where clients get hesitant. We all know changes are the most difficult to handle and we often don’t like talking about them. Every complex manufacturing environment sees changes to their products. Innovation or manufacturing and assembly inefficiencies, lead to the need for the BOM to be changed.
What do we need to ask ourselves?
Who is filing the Engineering Change Request, Order and Notice (ECR, ECO, and ECN )? (Is it coming from Purchasing, Testing, or Manufacturing?)
Who is affected by the change?
How is the change communicated to those affected?
The reason I like to ask these questions is that even though I’m on the team supporting the CAD tool, you HAVE to understand how the Product Data Model and its information (including the BOM) are utilized throughout the entire organization. Best in Class organizations have a set process for what drives a change in the Product Data Model. This is typically driven by a change to the form, fit, or function of an associated part or assembly. These companies aren’t just understanding how many ECOs they have in a given year, they understand the driving force to those ECOs. They then understand how to control the process so that the correct information is communicated back to Engineering, Purchasing, and Manufacturing. Once you have an understanding of the bottlenecks and inefficiencies, you need to consider how you will manage the process.
Misconception #2: You should be hesitant to adopt Engineering Changes.
With an effective system in place, you can be comfortable with changes as you now know exactly where it is at in the process and what needs to happen next. (Disclaimer: For C-Level individuals, you also have the ability to report on what is causing changes to your process. If you ever wondered what is eating up your margins, you now have a way to track per project, year, etc.)
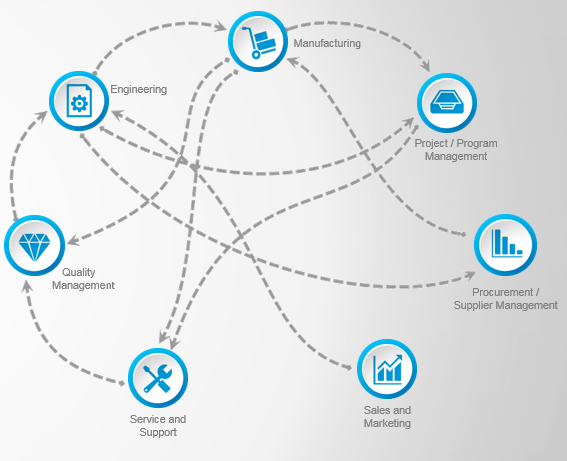
How it’s Managed
Over the last few years, you have heard more and more about the popularity of automating processes with the new state of the art electronic systems. ERP systems have been in place for years and we’re already starting to see the old ones die off and new systems appear. We’re seeing ever expanding interest in PLM systems within mid-market organizations. This is all happening as companies are starting to realize the importance of controlling these processes electronically .
When people ask me what system they should use to help them control their process, I often need to pause. Our CTO, Denis Morais, wrote earlier about how there isn’t a PLM system he recommends for every customer. Instead we need to understand your process and what you already have in place. Every organization operates in a different fashion which means our answer is different for everyone. I’ve assisted customers in becoming successful utilizing different ERP, PDM, PLM, and multiple different CAD packages.
Summary
Creating, maintaining and sharing an up to date Bill of Materials can be one of the most complicated processes to manage within a manufacturing organization. By having a better understanding of your internal processes outside of where they’re created, you can understand the true effects across the entire organization. The BOM is no longer a spreadsheet being passed around an organization. It is the output of the most important aspect, your Product Data Model. The centralized repositories , as utilized by the Best in Class companies, are pulling information from your data model to use in other parts of the organization. Instead of manual input or recreating your information, you have it at your fingertips because everyone is using the same system.
Within a complex manufacturing environment, time and cost are everything. You still need to create the same high quality product but with shorter lead times and tightened cost restrictions.
This is where SSI’s extensive background can assist in helping you understand your process and recommending a solution to fit your needs.