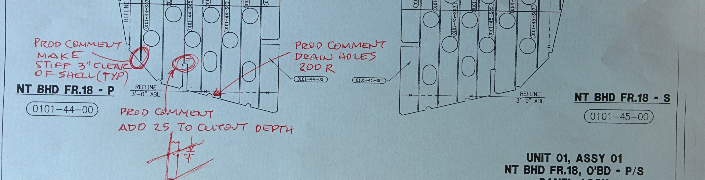
A current challenge many ship builder face today is implementing a successful feedback loop between the production floor and the engineering team. Lack of a good feedback loop can be very costly and is an area any ship builder should look at improving if they want to be more productive. There are some very modern, technically advanced yet simple ways which I think this feedback can be improved.
A common practice today is for engineering to create deliverable documents such as assembly drawings, arrangement drawing, isometric/spool drawings, profile plot drawings, etc. which will be used at the waterfront to build the designed vessel. Engineering ensures the design of the ship meets all classification rules and satisfies the ships predetermined characteristics but also includes the production engineering to build the vessel as efficiently as possible.
These documents produced by engineering and which are used by the production floor often contain inconsistencies and are missing information. Also, even with the best intentions from the engineering team, these documents do not always decompose the parts in the most efficient build sequence.
With the tight deadlines that virtually every client faces, the production floor personnel are left to make decisions to simply get the job done on time and on budget. These decisions can range from making educated guesses on the design intent, calling engineering for clarification to significantly changing the build sequence of the assembly/block/unit. I do think there are many ways where ship builders can significantly reduce the late and possibly costly decisions; however, I will tackle that in several other blog posts.
The issue is when these decisions are made on the production floor, they are rarely communicated back to the engineering team and therefore the changes are not captured in the MIM. This is not ideal and is especially bad if you plan to build one or more additional vessels with that production package.
I have seen many ways shipyards are attempting to solve this feedback loop; however, I want to talk about two methods which I have not yet seen but I think are viable in today’s shipyards.
Feedback loop workflow option 1
On the shop floor when the provided document requires some modification, instead of the changes being made on the printed document, the changes would be done in a digital version of the document. The changes would not include geometry changes so therefore the only tools which would be required would be redlining tools.
This modified digital version of the document would be available to the engineering team and therefore can be incorporated into the product model and the generated deliverable drawings.
The one question you may be asking yourself is how does the shop floor personnel find the digital version of the drawing which they need to mark up. Well, there are many ways this can be done. For instance, it could be accomplished by having the documents scheduled for that day in a specific location so there is limited amount of time required to find the drawing. However, the one I like the most is to have a QR Code on the document which will take them straight to the document (on the device which scanned the QR Code or on another device, (i.e. Computer) which needs to be edited.
Go ahead and try it.
- Scan the QR Code
- Add a comment, take a picture or use the redlining tools
- Save
Disclaimer: The link is open to the public and any changes you make can be seen by others. This is why you may see markups from other readers 🙂
This option is probably the less viable solution in today’s ship yards from the two options as it requires an additional skillset for at least the shop foreman to use redlining tools. It also may not work for some types of changes such as if the build sequence needs a major overhaul; however, I think this type of problem should be fixed by an improved production review process prior to building the assembly.
Feedback loop workflow option 2
This option really bridges the gap between tradition and technology. One thing I learnt very early in my career is that the biggest challenge to incorporating new and improved workflows and technology is people. So to provide as little disruption to the shop floor but still get the changes made at the waterfront to the engineering team is to take a picture of the changes on the printed document (what is currently done) and send it via email.
To streamline this as much as possible I would use a QR Code again (yes I love QR CodesJ) on the printed document which automatically sets the recipient (most document management systems PDM/PLM support email), subject (the specific drawing) and a message. So the workflow looks like this:
- Scan QR Code on drawing they made changes to
- This will automatically open the email program, set the recipient, set the subject to specifically specify the drawing being scanned, and sets a message.
- Take a picture of document
- Click Send
Go ahead and try it:
This has the benefit over the first option as no new skill set needs to be learnt by the shop floor, unless of course they do not know how to take a picture, which actually might be the case for some yards.
Closing remarks
The feedback loop from production to engineering has seen little improvement in many yards in the past decades. A seamless workflow to exchange the information changed at the waterfront continues to be one of the areas where many ship builders want to enhance. With a better feedback loop, ship yards will ensure modifications are incorporated into the 3D product model and re-used for follow-on vessels.
By using modern and mature technologies ship yards can significantly improve how this information is transferred with very little disruption and requires virtually no new skills.