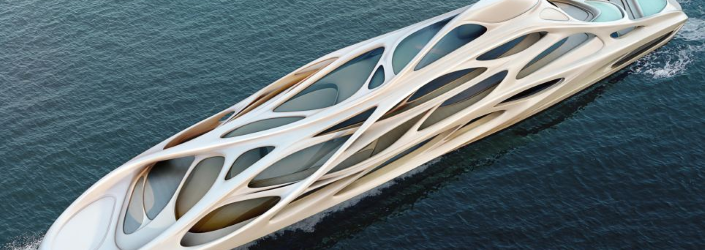
In the future, how will potential ship buyers determine what types of ships they need and when they should be purchased? For shipping companies, servicing companies and even navies, determining the details of a ship’s function and its exact requirements are difficult. Furthermore, if you consider that the lead time to build a ship can be years, it is not always clear when is the best time to buy. Even if some will not admit it, shipbuilding is like rolling some dice.
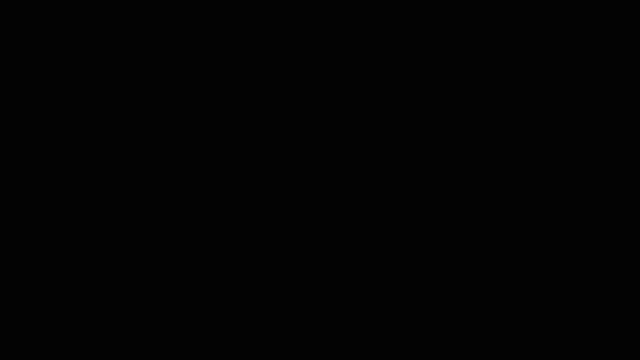
Digital Shipbuilding
Get a first-hand experience of what the design, build, and maintenance phases are like in an increasingly digital shipyard.
Experience nowShips are major capital assets that have to be maintained in order to perform their functions and eventually must be replaced. This means that to understand when you need to purchase a new ship and to help you understand what can be expected related to performance, you need to have data related to the actual ship.
Only after you have this data, can you reasonably make purchasing decisions and set your requirements. However, this leads to an additional challenge. When the ship designer gets the requirements from the customer, how do they transform them into a ship that can meet those specifications? It is all a matter of gathering data and then finding an effective way of putting that data into use.
Customers’ Requirements
A modern vessel generates about 20 GB of data per day. However, all this valuable data is not really being transformed into information. In the future, we will aggregate all of it together and analyze it with Big Data techniques and Artificial Intelligence algorithms. This will enable owner operators to better determine when they need a new vessel, replace an existing one, just repair an existing one, and understand performance of certain routes with variables such as weather, cargo, etc.
This will have a huge benefit to owners because they will be able to save significant money in operating and even servicing their fleet. The data gathering and analysis will evolve to factor in many of the requirements of a ship and no doubt will come to include even more sensors which will in turn create more data to ultimately make better decisions. Below is a list of some of the information that will be analyzed.
Examples of Types of information
- Integrated sensors (IoT) on ships and rigs. According to a McKinsey report, currently, only 1 % of data from an oil rig with 30,000 sensors is exploited for decision making. That will change in the future as increasingly it is realized that this information can be used to determine performance and can provide valuable information.
- Maintenance records: Understanding the maintenance of each ship can provide insight into the quality of the ship and/or the supplier of the ship equipment. Since virtually all ships are different using different designs, shipyards, suppliers and integrators, it is hard for us to find any correlation between better quality and any of those factors.
- Ship performance: Ship performance is measured differently for different types of ships and factors for analysis could include fuel consumption, duration of voyage or response time, max. cargo, etc. This information can and will be used to help determine future performance requirements as well as the potential to modify the current ship so it performs better.
- Business Intelligence: The ship is an asset for an owner which produces revenue. There are many business reasons that the ship may not be capitalizing on current opportunities. It could be that the ship is undersized with today’s market or does not meet certain environmental regulations and therefore cannot be used on more lucrative routes/ports.
There are a lot of other information such as weather and current information which will be used for determining the best ship route, but as it did not affect the changing of requirements I left them out.
Design of the Ship
Once we have the requirements from the client it is time to create a design that will satisfy or exceed all requirements…this is the future remember:). For the initial design of a ship there are a lot of different calculations that are needed from hydrostatics, hydrodynamics, layout arrangements, loading information, seakeeping, maneuverability, safety scenarios, collisions scenarios and many, many more. Most companies use several pieces of software to run through all the analysis. The algorithms we use today were designed to be run on a single physical box and therefore make several “assumptions” or “simplifications” to reduce the amount of time to do the analysis. Furthermore, each calculation performed has a symbiotic relationship to other calculations with one’s outputs being the other’s inputs and this creates a long chained feedback loop. Because each of these calculations can affect the design of a ship, after one calculation is run and decisions are made, naval architects input the modified design into another calculation, then its output results are fed into another calculation and so on. This is an iterative approach that currently takes a long time for the designer. In the future we will leverage the power of the infinite computing of the cloud to speed up this process.
This will provide two significant benefits. First it will allow us to modify our algorithms to not require the removal of details via simplification. Since we have a lot more horsepower we do not need to be too concerned with processing power. Secondly, it will allow better integration between the products we have selected to do the analysis since software vendors with these cloud applications will focus on the integration with other software vendor products which currently is usually done by the client. This means that the chaining of one set of calculations to another set of calculations input will be done with very little effort for the designer.
This will then allow the user to set a larger set of criteria and constraints and have several calculations generated depending upon different scenarios with each cloud application feeding its output to another application’s input. This can happen several hundreds of times with the end result being several concepts and all the required properties and information for the designer to either
- Refine the criteria and execute more calculations
- Accept those initial concept designs.
The cloud applications calculations will use existing algorithms but will potentially be developed differently to leverage the infinite parallelism of the cloud. There will also be new algorithms. New algorithms could be a generative design of the hull shape, or an algorithm that takes information from the real world such as the previous operating cost of a ship or even the cost of manufacturing at a specific yard/region.
When the appropriate calculations are complete they will allow orders of magnitude more variations than are done today. Once the designer is happy with the multiple concepts generated he will present some of the concepts to the customer.
Integrating Customers into the Design
There are some companies that already involve the customer in the design process; however, in the future this is going to happen earlier and the time between customer feedback and a modified design will be very short.
The first time the customer will be able to review concept designs will be much earlier than is done today, largely due to the fact that many of the calculations will be cloud based. When the concepts are presented to the client they will be done visually. Depending on the ship that is to be built there will be a large virtual reality component in this initial customer review of the concepts. This virtual reality model will be presented to the customer to communicate the concept design perfectly. The customer and the designer will be on the same page from the start.
As the virtual reality model is reviewed, the designer will be able to point out various characteristics of the concepts and then get feedback from the client. Since there are always compromises that have to be made when designing a ship, the client might want to see a concept prioritizing one requirement over another (ex. Capacity vs. performance, changing supplier or where it is manufactured, deck layout, etc. ). Depending on the feedback, the designer will be able to update the criteria and re-run the analysis done in the initial phase. Again, using the cloud and potentially only a subset of calculations (just in order to get an idea) the new modified concept with all related data including the virtual reality model will be updated. This more interactive and instant feedback will significantly improve the results of meeting customer expectations as well as complete the overall task in a reduced amount of time.
After several comments and feedback from the client, the designer will generate a more complete set of calculations as well as narrow down and detail the concept which the customer and designer have collaborated on.
Closing Remarks
In the future of shipbuilding the way owner/operators determine ship requirements will evolve to have much more empirical data from monitoring their current fleet. They will also be able to better analyze what is required to achieve their business goals.
Taking the requirements and generating several concept designs will be aided (slingshotted) by the infinite computing of the cloud. Many more iterations and variables will be taken into account without requiring the current simplification or generalization we have with current algorithms. However, all this will happen in a faction of the time it takes today.
Humans are still much a part of the system and will not be displaced or even replaced by technology. Technology will allow designers to go through many more iterations with very little waiting time between them. Technology will allow designers to get faster feedback on changing or modifying variables or constraints allowing the designer not to be limited or restricted to only previous experience. The ability to try something new and to fail quickly will be a source of a lot of new and innovative designs.
Customers will also be much more part of the design compared to today. We will be able to leverage virtual reality tools as well as provide the opportunity of experimenting with changing the priorities of the requirements and getting results quickly with very little effort. This will significantly improve customer satisfaction as well as produce the best ship for what they need.
Blog Posts in the Future of Shipbuilding Series
- Future of Shipbuilding (15+ years)
- Future of Shipbuilding: Engineering Design
- Future of Shipbuilding: Detail Design and Production Planning (Part 1)
- Future of Shipbuilding: Detail Design and Production Planning (Part 2)
- Future of Shipbuilding: Manufacturing (Part 1)
- Future of Shipbuilding: Manufacturing (Part 2)
- Future of Shipbuilding: The Journey Forward