Incat Tasmania has officially launched the world’s largest battery-electric ship, marking a new era for sustainable maritime travel. On May 2, 2025, the 130-metre China Zorrilla (known during construction as Incat Hull 096) made its long-anticipated debut on the River Derwent. This monumental launch showcased Incat’s world-class shipbuilding talent and highlighted the pivotal role digital tools play in turning next-generation vessels from concept into reality.
Behind the celebration was a quiet but critical collaboration: a partnership between Incat and SSI, built on shared values of innovation, efficiency and forward-thinking technology. This partnership helped navigate the complex design and production requirements of such a revolutionary vessel and played a significant role in ensuring the project stayed on course.
“Hull 096 is the most ambitious, most complex, and most important project we’ve ever delivered. This ship changes the game.”
- Robert Clifford, Incat Chairman
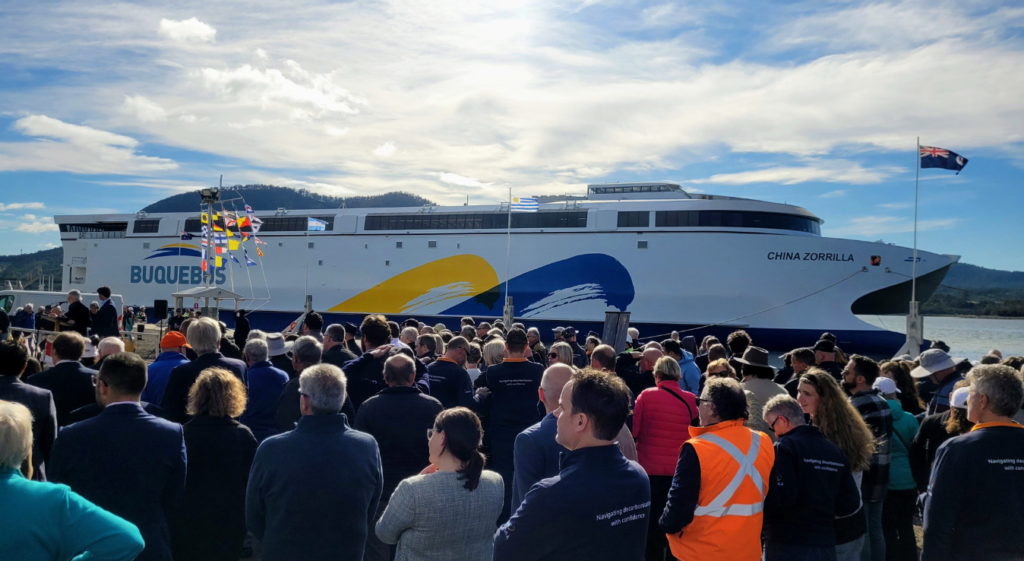
Celebrating A Historic Launch
The vessel’s launch was a proud moment not only for Incat Tasmania but for the broader maritime community. Industry leaders, engineers and local officials gathered on the banks of the Derwent River to witness the float-off of a vessel that is set to transform ferry transportation around the world.
Among the guests was Simon Crook, Senior Solutions Specialist at SSI, who was invited by Incat in recognition of his close involvement during the shipyard’s transition to SSI’s digital shipbuilding tools. Simon’s on-site presence reflected SSI’s strong partnership with Incat — one built on collaboration, support and a shared commitment to innovation in ship design and construction.
A Digital Partner in the Background
While the launch of China Zorilla made front-page news, we at SSI are proud of the groundbreaking work that happened long before the vessel ever touched the water. Incat Hull 096 – the world’s largest battery-electric ship – marked the beginning of Incat and Revolution Design’s transition to digital shipbuilding. ShipConstructor was first introduced during this project to model and produce production drawings for selected areas.
More importantly, this digital transformation happened without disrupting production. During the design process, Stewart Wells, Technical Manager at Incat, spoke about the efficiency of incorporating ShipConstructor midway through, saying “We haven’t stopped production. We’ve had a project running this whole time and there’s been no impact. In fact, we’re seeing benefits.” That uninterrupted momentum was critical in ensuring Hull 096 launched on schedule — and in better shape than ever.
Incat’s Head of Design, Jason McVicar, echoed the value of SSI’s hands-on involvement: “With SSI, we always knew that we were partnering with a group that was not going to just provide us with a set of software.” Instead, our experts — including on-site support from Simon Crook — helped identify the best-fit workflows to align with Incat’s unique production style and ambitious goals.
That combination of strategy, software, and support made a real-world impact. Detailed designs reached the floor faster, automation sped up production output and the ability to cut plate sooner kept the project firmly on track.
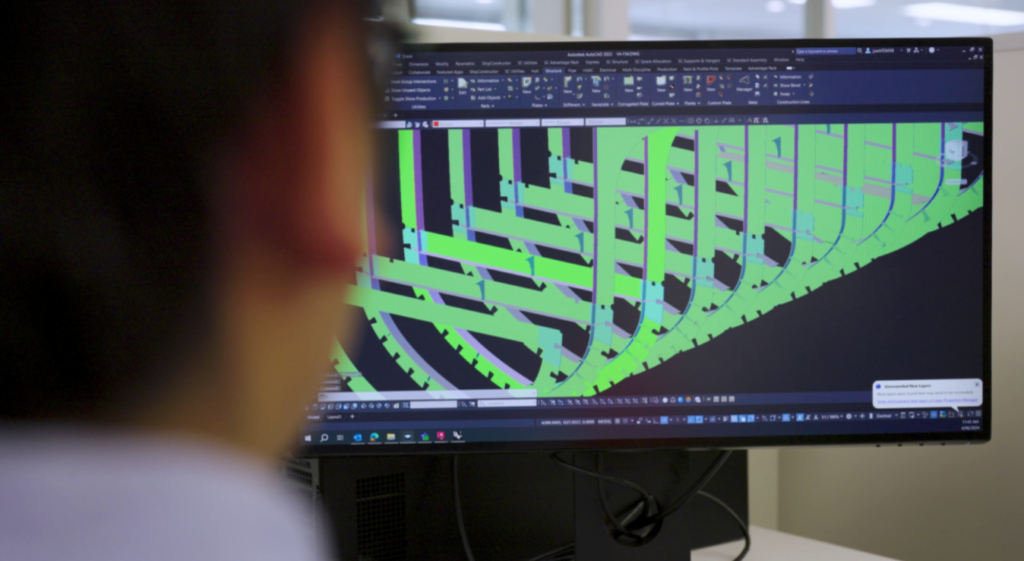
Designing Complexity with Confidence
Hull 096 posed unique design and production challenges, including:
- Coordinating modular construction across different teams and build zones.
- Adapting to evolving design requirements and late-stage changes.
- Managing and distributing massive amounts of production data.
- Maintaining design continuity from concept to final assembly.
Traditional workflows weren’t equipped to handle this level of complexity. But with ShipConstructor, Incat was able to model structural, systems and outfitting components in a single environment, streamlining coordination across disciplines.
With EnterprisePlatform, the production team always had access to the latest design updates and information, ensuring fewer errors and less rework on the floor.
Supporting Modular Production
Incat’s build strategy involved constructing the vessel in distinct modules, with different teams working on various zones simultaneously. This modular approach offered speed and flexibility but also required extreme precision.
Our tools ensured that all design data flowed through a single source of truth. This meant changes made in one part of the model would update across the entire system, reducing confusion and preventing production mismatches between zones.
By working from synchronized digital models, each team could build with confidence, even while operating on separate areas of the ship. The result was a seamless build that came together exactly as planned.
The lessons learned during the design and build of Incat Hull 096 laid the groundwork for a broader rollout on future builds, including the 78-metre hybrid-electric ferry, Hull 100, where a digital twin is being developed to enable new advances in shipbuilding. SSI is proud to be supporting Incat and Revolution Design in their next chapter of sustainable shipbuilding.
“We’re not just building a ship – we’re building the future.”
- Stephen Casey, Incat CEO
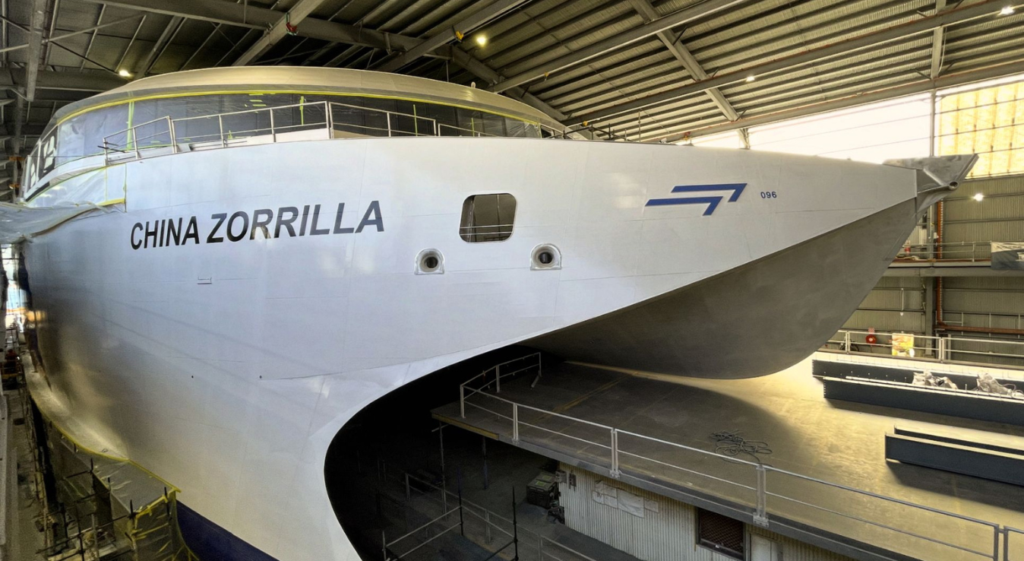
A First-Of-Its-Kind Vessel
Hull 096 is unlike any ship before it. Once delivered, it will be the world’s largest zero-emission lightweight Ro-Pax ferry — entirely battery-powered and capable of transporting 2,100 passengers and 226 vehicles without burning a drop of fuel. Its construction represents a huge leap forward for the decarbonization of marine transportation.
Powered by six electric motors and an onboard battery energy storage system, Hull 096 shows that sustainability and performance can coexist at scale. Its ultra-lightweight catamaran design, built from marine-grade aluminum, allows for high-speed transit and lower operational costs — all while dramatically reducing environmental impact.
Designed and built in Tasmania for South American operator Buquebus, the ship has become a global symbol of what’s possible when innovation, engineering and digital shipbuilding align.
A Blueprint for the Future of Shipbuilding
Hull 096’s launch isn’t just a milestone for Incat — it’s a blueprint for what’s possible in shipbuilding when traditional craftsmanship is paired with smart digital tools. This vessel shows how early digital adoption empowers shipbuilders to meet the demands of modern projects without sacrificing quality, budget or timeline.
By partnering with SSI, Incat was able to:
- Improve design accuracy and communication
- Cut production time drastically
- Adapt quickly to change without starting over
- Deliver a world-first, zero-emission vessel on schedule
As shipowners continue to push for greener, faster, and more efficient vessels, shipbuilders will need digital-first workflows that can scale to match those ambitions. Hull 096 is proof that those workflows are already here, and they work.
Celebrating Partnership and Looking Ahead
At SSI, we’re proud to have played a role in helping Incat turn this ambitious project into a celebrated reality. The successful launch of Hull 096 proves what’s possible when forward-thinking shipbuilders are equipped with the right tools and support.
To the entire team at Incat Tasmania: congratulations. You’ve built more than a ship — you’ve built the future of ferry transportation.
Want to see how SSI’s digital shipbuilding solutions can support your next build?
Read the Full Case Study or contact us to talk about how we can help turn your next big idea into a milestone success.