Nor-Shipping 2025 brought together a global cross-section of the maritime industry at a time when change feels more constant than ever. From digital transformation and workforce challenges to sustainability goals and geopolitical uncertainty, the conversations this year reflected an industry navigating both complexity and opportunity.
For SSI, the event provided an opportunity to speak directly with shipbuilders and designers from Norway, Turkey, India, Japan, the Netherlands, and beyond. These conversations revealed not only regional differences but also common themes — concerns about capacity and capability, the urgent need for data-driven workflows, and the importance of building resilient, future-ready shipbuilding strategies.
Here’s a look at the key insights and emerging priorities shaping the direction of global shipbuilding, informed by direct discussions with industry leaders and innovators.
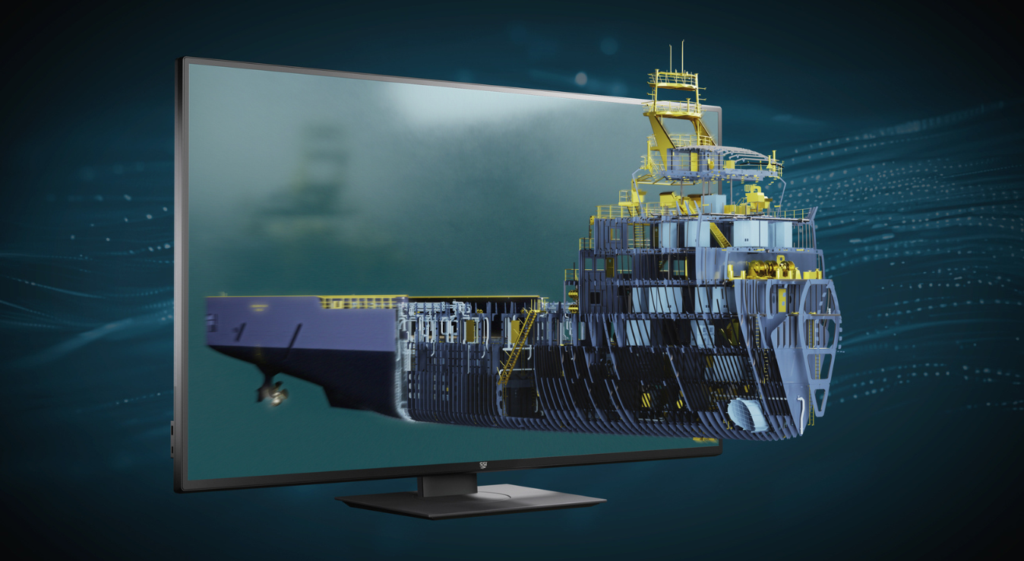
Digital Transformation in Shipbuilding Now
One of the most consistent themes at Nor-Shipping was the growing maturity of digital shipbuilding. From design and production to operations and maintenance, digital tools are reshaping workflows across the vessel lifecycle—and not just in theory. Across conversations with shipbuilders and design offices, it’s clear that digitalization is no longer a goal; it’s becoming the standard.
In Norway, firms like Marin Design AS and Skipskompetanse AS are pushing beyond traditional CAD toward truly integrated digital ship models. These aren’t just design assets—they’re data-rich digital twins that support everything from construction to onboard training and long-term maintenance. As Knut-Ola Martinussen from Marin Design explained, embedding information about piping, electrical, and structural systems into a single model enables shipowners to navigate vessels virtually, identify needed repairs, and streamline dry dock planning, all without flipping through stacks of manuals.
Skipskompetanse echoed this shift, noting that 3D models are now central not only to production but also to knowledge transfer and asset longevity. By replacing static 2D drawings with dynamic, interactive representations, they’re enabling more effective onboarding and a more adaptable approach to maintenance.
Digital transformation isn’t limited to design. Shipyards like Thecla Bodewes in the Netherlands and GRSE in India are expanding their use of automation—particularly in welding, blasting, and painting—to maintain productivity despite tightening labor markets. Together, these shifts point to a future where precision, data access, and adaptability define competitiveness in shipbuilding.
Workforce Challenges and Innovative Responses
Even as digital tools and automation gain traction, one challenge remains stubbornly universal: a shortage of skilled labor. From welders and steelworkers to pipefitters and electricians, many shipyards are struggling to find the hands-on expertise needed to keep pace with demand.
At Tersan Havyard, this issue is front and center. President of Sales Silje Smadal shared how difficult it’s become to recruit workers for the physically demanding and technically complex roles that shipbuilding requires. Part of the problem is generational, and many young people simply aren’t aware of the scope and sophistication of today’s shipyards.
To change that, companies like Tersan are investing in outreach: connecting with schools, promoting skilled trades, and reframing shipbuilding as a modern, technology-driven career path. The goal isn’t just short-term recruitment—it’s to build a sustainable talent pipeline.
At the same time, the labor shortage is accelerating the adoption of automation. Wilco Smit of Thecla Bodewes noted that robotic welding is no longer just an efficiency upgrade—it’s becoming essential. In Japan, Namura Shipyards is taking it a step further, piloting a digital factory model that incorporates AI-driven inspections, automated fabrication, and IoT-connected systems to maintain quality and throughput with fewer personnel on the floor.
Taken together, these responses reflect a growing industry consensus: the future of shipbuilding depends on a workforce that combines human expertise with machine precision, and on an ecosystem that can attract, train, and retain the next generation of shipbuilders.
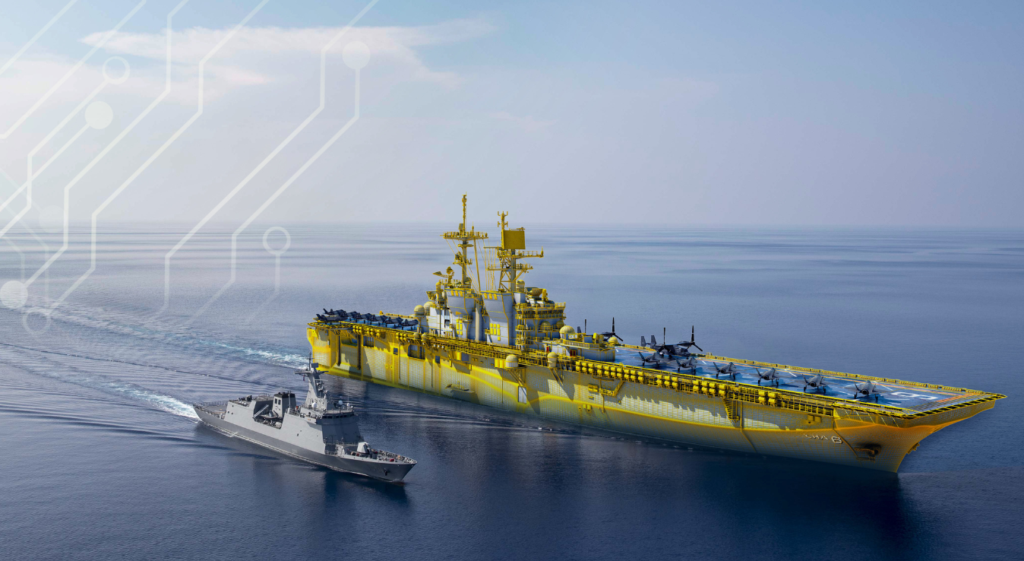
Driving the Energy Transition: Green Technologies and Alternative Fuels
Sustainability isn’t just a goal—it’s becoming a baseline expectation in global shipbuilding. Regulatory pressures, environmental accountability, and shifting customer demands are accelerating the industry’s push toward cleaner fuels and more efficient propulsion systems.
Electric propulsion, once seen as a niche solution, is now firmly in the mainstream. At Thecla Bodewes Shipyards, decades of experience in electric systems are informing new efforts to integrate alternative fuels like methanol, hydrogen, and ammonia. While these fuels offer the potential for significant emissions reductions, their adoption is complex, requiring new infrastructure, safety standards, and operational procedures.
Namura Shipyards in Japan is at the forefront of this transition, already constructing ammonia-fueled vessels and actively researching hydrogen and CO₂-neutral designs. These efforts reflect more than environmental ambition—they’re strategic moves to remain competitive with shipbuilding leaders in Korea and China, where green innovation is advancing rapidly.
In India, GRSE is combining its investment in sustainability with a focus on automation and innovation, developing autonomous surface vessels and next-generation naval warships while expanding into commercial markets. This intersection of technology and environmental responsibility is becoming a key differentiator.
What’s clear across regions is that sustainability is no longer a separate initiative—it’s a core component of long-term competitiveness, with green technologies shaping both the ships of tomorrow and the strategies behind them.

Navigating Global Market Dynamics and Regional Ambitions
Shipbuilding remains a highly competitive and regionally distinct industry. While Asian shipyards, particularly in China, South Korea, and Japan, continue to lead in volume through scale and advanced manufacturing, other regions are finding strength in specialization.
In Europe, shipyards in Norway, the Netherlands, and Turkey are focusing on high-quality builds, innovation, and strong regional collaboration. Trabzon Shipyard, strategically located on the Black Sea, is expanding into European markets even as it navigates the complexities of regional geopolitics.
Meanwhile, India is positioning itself as a rising force in global shipbuilding. Commodore PR Hari of GRSE spoke to the country’s bold goal of growing its global market share from under 1% to 10% over the next 15 years. That ambition is backed by government investment and a nationwide push to modernize infrastructure and shipyard capabilities.
Across all regions, one thing is clear: market dynamics are being shaped not just by production capacity, but by trade policy, technological leadership, and geopolitical strategy. Shipyards that can adapt quickly and think long-term will be best positioned to lead in this evolving global landscape.
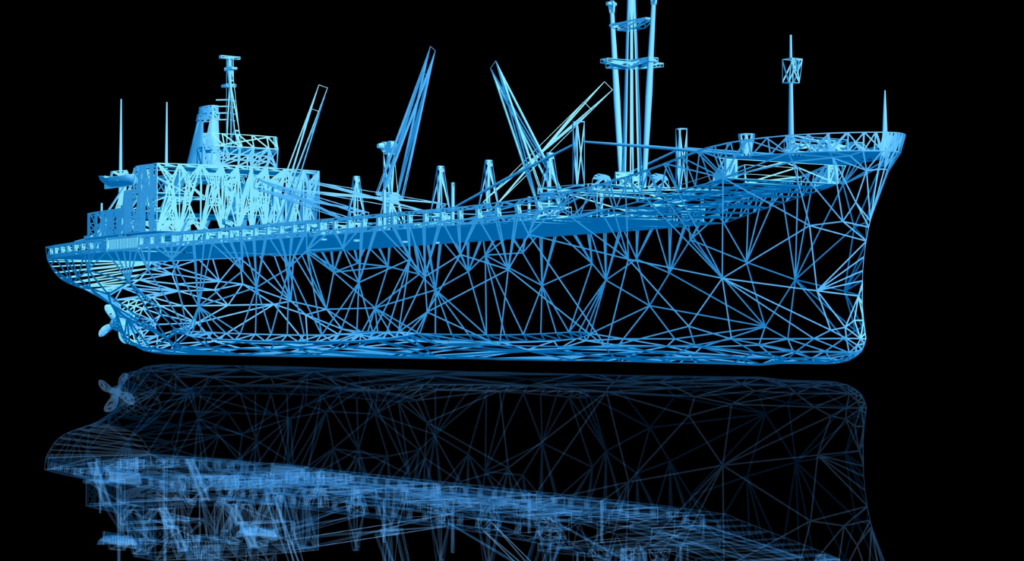
Innovation in Shipyard Operations and Project Diversification
Shipyard modernization has moved well beyond incremental upgrades—it’s now central to staying competitive. Around the world, shipyards are adopting advanced manufacturing tools like laser cutting, CNC machining, and digital factory systems to improve precision, adaptability, and long-term efficiency.
At Turkey’s Trabzon Shipyard, these technologies are being implemented alongside green energy systems, illustrating how operational innovation and sustainability increasingly go hand in hand.
This push for flexibility is also reshaping project portfolios. Many shipyards are expanding beyond traditional builds into areas like naval vessels, multipurpose ships, and superyachts—diversifying not just to grow, but to remain resilient in volatile markets.
Namura Shipyards in Japan is a case in point. By integrating AI-powered inspections and broader digital strategies, Namura is redefining what’s possible for legacy shipyards in an evolving industry.
Industry-wide, the takeaway is the same: in today’s landscape, innovation in process is just as critical as innovation in product.
Where Shipbuilding Is Headed — and How We Get There
Nor-Shipping 2025 offered a clear view of an industry in motion, where digitalization, workforce reinvention, sustainability, and global pressures are no longer future concerns, but immediate priorities. What stood out most wasn’t just the scope of the challenges, but the creativity and urgency with which shipyards and designers around the world are responding.
From adopting BIM and automation to investing in alternative fuels and reshaping talent pipelines, the path forward is being built by those willing to rethink what’s possible — and act on it.
At SSI, we’re proud to stand alongside shipbuilders as they navigate this transformation. Our role is to enable the shift toward smarter, more connected, and more resilient ways of working, helping our partners stay agile in a rapidly changing world.