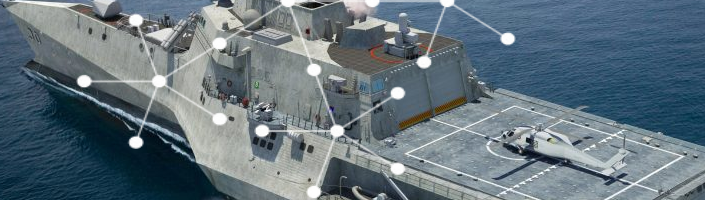
To stay competitive globally, shipyards have commonly turned to specialization. However, the combination of the recent downturn in shipbuilding and the rise of advanced shipbuilding technologies, the trend towards specialization has significantly picked up in recent years. Overall, the divide is growing between new build and repair and, within new builds, between complexity and value. Geographically, the impact of this divide is clear. Europe, and to a lesser extent Japan and Korea, have really used specialization to their benefit, but what’s truly interesting is how they’ve done it and the niches they’ve turned towards.
Shipbuilding vs Repair
While many large shipyards that construct new builds also perform maintenance and repair, we’re beginning to see many yards turn to specializing in either one or another, particularly in Europe. There, we’re seeing clear delineations along country lines. For example, The UK, Greece, and Malta are heavily focused on repair, while Norway, Finland, and Croatia are heavily committed to new builds.
While part of this specialization stems from geographic constraints (ship repair is concentrated along busy shipping routes), another part of what has allowed an increasing number of shipyards to focus on repair so successfully is the adoption of digital technologies. As more ships are delivered with digital twins, shipyards that can effectively connect with and leverage that information, as well as other digital technologies like laser scanning, are at a significant advantage when it comes to efficiently performing maintenance, repair, and overhaul (MRO).
Complexity vs Value
Digging deeper, we see that shipbuilders have also specialized in what new building they take on. Doing so is what has allowed many smaller countries to compete with Asian shipbuilders at scale. The divide itself has come down to complex ships vs value-focused vessels.
To compete with the big three Asian shipbuilders of China, Japan, and Korea, the European shipbuilding industry has turned to focus on building higher-tech, more complex, and higher-value ships. Specializing in these types of vessels is an effective strategy to combat the inherent higher costs of labour and construction present in European shipyards.
Germany was one of the first to fully embrace specialization and has continuously invested in the idea since the early 2000s. Now, as a 2015 German government mandate is finally being realised, we’re seeing the consolidation of German shipyards and a commitment to building specialised vessels, like cruise ships, mega yachts, ferries, and other ships that require high degrees of technical complexity and low standardization, as opposed to (relatively) simpler container ships or tankers that don’t differ as significantly from ship to ship.
Similar changes to the shipbuilding sector have occurred in Norway. Large amounts of outsourcing, and low amounts of standardization, have favoured the production of niche and more specialized vessels. However, in Norway, we’re also seeing a dedication to lean shipbuilding, a unique combination of lean manufacturing and lean construction practices. Lean shipbuilding is allowing Norwegian shipyards to leverage their technical proficiency and minimize the competitive impacts of high costs inherent to Norwegian industry. The key factor that has allowed Norweigan shipyards to commit to a lean model has been technology that allows shipbuilders to understand how parts and components flow throughout a yard. Then, through the analysis of that information, they successfully reduced inefficiencies and improved quality while producing vessels of high complexity.
Aside from Europe, Japanese and Korean shipbuilders have also had to shift focus towards relatively higher-value vessels in order to compete with the low costs offered by Chinese shipbuilders. However, this shift is significantly less pronounced than in Europe. Korean shipyards are particularly competitive in the tanker segment, while Japanese and Chinese yards continue to focus on containerships and bulkers. In numerical terms, this difference in ship value becomes clear, with Korea averaging US$92 million per ship in 2013, compared to US$ 48 million and US$ 45 million in Japan and China, respectively. However, in the same year, German shipyards averaged US$ 175 million per ship, demonstrating the dollar impact behind their specialization attempts.
Future Trends
Naturally, a large part of why shipbuilders are choosing to specialize is driven by larger market trends. In recent years, demand for standard vessels has decreased, while ships requiring more complexity, like ferries, cruise ships, and specialized workboats, are increasingly in demand.
Looking at the bigger picture, this trend is cutting into the market share of Korean, Japanese, and Chinese shipbuilders. While those countries still dominate the market in terms of ship deliveries, combining for an 83% market share. Looking at new orders paints a significantly different picture. The specialized European shipyards have dramatically moved forward, increasing market share from 8.2% in 2014 to 27% in 2017, second only to China.
Unless we see dramatic shifts toward lower-value vessels, which are unlikely considering the autonomous and increasingly data-focused technologies that ship owners are pursuing, the shipyards which will survive long-term, no matter their location, will have the ability to adapt and focus on the most profitable types of vessel.
To maintain that flexibility and effectively construct complex ships, it will become more necessary than ever to understand and manage each element within a shipyard throughout the construction process and the lifecycle of a ship, if dealing with MRO. The shipyards who are doing it best are leveraging technologies and solutions that allow them to connect with each facet of a yard, allow for the easy transfer of information, and make it possible to identify inefficiencies.
Post Comments
One of the problems we have found, is the ignoring of “discovery based innovations” which has the potential of major impact on the industry. This neglect is based on the nature of copying what others are doing, and the skeptical thinking that nothing revolutionary can be developed in such well established industry with as long as history the Maritime Industry has.
But all people we contacted, were wrong not partnering with us, so we are expecting to be copied later, after we show our advanced innovations in hull design and upgrades – but this is yet in the future, although it could have been the standard already. We are OK and are working with special contacts we have – but from our past experience, we suggest for the industry not to ignore inventors or yet unsolicited or unexpected proposals – so you do not just join all others who just folow-up but never take leadership with real revolutionary innovations.
There may be inventors offering new opportunities on the www, so searching for promising innovations can grant you a special leadership position in the industry, where others will follow you, and where you are not just another follower of what others are doing.