Ships have a lifespan measured in decades, and the impacts of non-standardized deliverables echo through the project lifecycle. Shipbuilding projects have tight schedules, and teams are often pushed to deliver documentation quickly, which can compromise good engineering processes. Immediate departmental objectives and project milestones are met, but without a standardized, holistic approach, the downstream impacts disrupt organizational efficiency and ultimately lead to higher project costs.
About ten years into my career as a designer, I was given the opportunity to give on-site support to a naval refit project. The experience was eye-opening and an opportunity to troubleshoot the issues caused by inconsistent data first-hand: the configuration of the ship was different from the drawings/models provided, as-built changes had not been captured, the production drawings lacked critical dimensions and references, and fabricators needed to dissect the production drawings for the information they required.
Impacts to Models
The disruptions caused by non-standard deliverables begin with the initial creation of the part and insertion into the product model. Failing to feed the product model with all required geometrical and metadata leads to increased time searching for and determining the correct project information at each phase of ship construction.
Example | Impact |
---|---|
Missing Attributes | Information can’t be searched for in downstream processes. |
Parametric Relationships | If parametric relationships are not used, change is difficult as associated parts need to be moved manually, creating more work and increasing the risk of human error. |
Parametric Connections | Parametric connections ensure compatibility between parts reducing errors. E.g., Ø50mm pipe can only connect to Ø50mm pipe of the same material, flanges need to connect to flanges, etc. |
Production Markings | Missing mark lines which could be etched on plate parts during cutting need to be manually added during production, taking several times longer. |
Invalid Parts | The use of invalid parts or ‘dumb solids’ means parts can’t be registered to the project. |
Missing Geometry | Missing geometry, such as mounting locations or connection points, make it difficult to interface equipment with the ship. |
Missing Maintenance Envelopes | Soft clashes cannot be automatically identified. |
Impacts to Drawings
Non-standardized documentation leaves downstream users responsible for determining the missing information or deciphering the documentation for the required information. I’ve experienced the frustration caused, usually by inexperienced designers, by providing dimensions to non-visible planes such as frames or the ship’s centreline. A tape measure cannot be run from this plane, especially at deck level. To get the measurement, the non-visible frame needs to be determined and marked, which can be difficult, especially when bulkheads are insulated.
Example | Impact |
---|---|
Poor Dimensions | As per the example above, poor dimensions leave stakeholders to work out appropriate dimensions. |
Missing Dimensions | Stakeholders are left to determine the dimensions from the information or to reach back to the design team for the correct information. |
Missing Annotations | Drawings often contain important annotations such as weld notes, assembly sequences, tolerances, or finishes. What happens when they are not there and production teams are used to seeing them? It results in rework that could have been avoided. |
Too much information / Hybrid drawings | To save time in the drawing office, a hybrid drawing is created containing class, installation, and fabrication details all in one. This means the same heavily detailed drawing package is handed out to all stakeholders, and they are left to determine which information applies to them. Aside from the time taken to determine what needs to be done, the drawings are often open to interpretation and raise questions between departments. |
Impacts to PLM/ERP Systems
PLM and ERP Systems, amongst other things, let stakeholders quickly search for the information they need and filter through the logical relationships between parts. PLM/ERP systems rely on repeatable, consistent data. You can filter for a system, view the spools, view the P&ID, view the parts and their VFI, but what if the relationships aren’t there? Non-standard naming conventions and missing attributes leave stakeholders with incomplete information. Planning, procurement, production, and estimation departments rely on this information, so it is crucial that it is accurate.
Example | Impact |
---|---|
Missing Attributes | Searching for information will not return accurate results. |
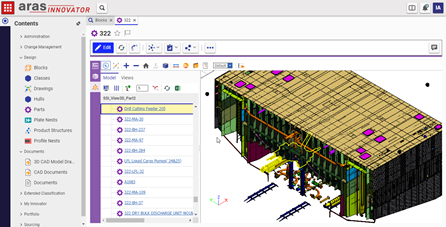
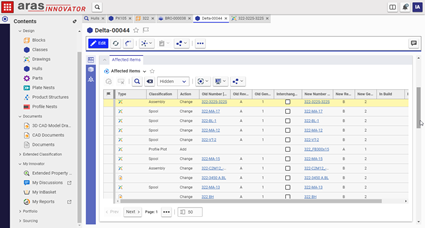
Impacts to change management
Change is unavoidable in shipbuilding. It is one of the few industries where ships begin construction well before the design is finished. Change shouldn’t be difficult with a standardized product model where a single source of truth is used for manufacturing information. Without parametric relationships between parts and drawing views, parts and documentation need to be updated manually. Manually updating parts and views allows for human error to occur and can consume hundreds of design hours depending on the complexity of the change.
Example | Impact |
---|---|
Manually updating multiple sources of information | Change can be time-consuming and prone to human error when updating multiple sources of information and disconnected drawing views. |
Impacts on Your Shipyard
The impacts of non-standardized deliverables may not be immediately visible at first; however, the associated costs are exponential and begin almost immediately at fabrication.
Where do you see non-standard deliverables the most? Comment below.
In part 2, we will discuss strategies and examples of how shipyards can achieve standardized, repeatable deliverables – all while maintaining efficiency – in order to mitigate these impacts and risks to the project.
Subscribe for More Shipbuilding Solutions
To see the next insights from Simon and our other Solution Specialists, make sure to subscribe.