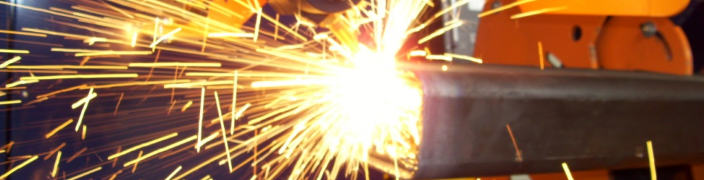
I want to spend some time talking about CNC profiling machines and why connecting them to the 3D information in the product data model can improve overall quality, throughput and cost.
CNC profiling machines have been around for a long time but I have definitely seen an uptick in the number of CNC profiling machines being installed across shipyards around the world. This is not too surprising as next to planar plates, profiles (stiffeners & faceplates) are the most common type of part within a ship. The percentage is dependent on the type of ship, required classification society(s) to support and even designers‘ creativity but can easily account for ~40% of the number of parts within a project.
I have seen two main strategies yards have decided to adopt for the implementation of their CNC profiling machine.
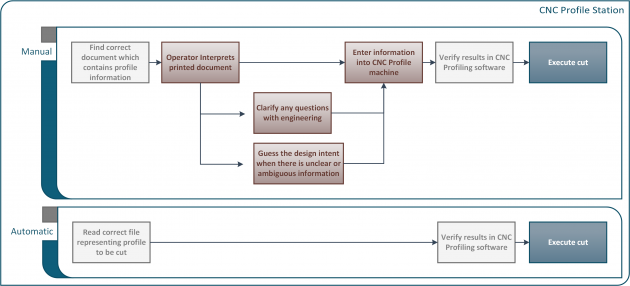
The first is mostly manual. This is where the operator receives some printed documents, either a spreadsheet or a profile plot containing all the information of the profile(s) which are to be cut, marked, and bent. The operator manually enters the information into the machine and then executes the cut on the profile.
The second is more automated. The operator loads a file(s) into the CNC profiling machine and then executes the cut.
*Note: I ignored the handling and setup of the profile before and after executing the cut as they are needed for both strategies.
With the two main strategies above it is obvious which one is more productive for the operator…the automated one. The thing is, just because the automated strategy is more efficient for the operator does not mean it is more efficient for the organization as a whole. We would really need to look at all the effort and artifacts required to support both strategies. When we do this you will see the automated becomes hands down way more productive from an organizational perspective.
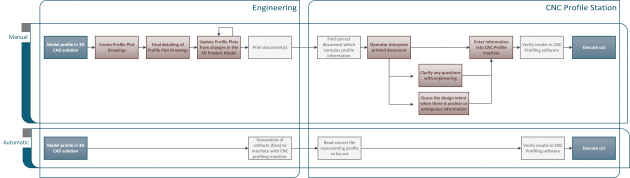
We can assume the exact same 3D product model is required for either strategy.
To support the manual process there needs to be some sort of documentation generated to communicate with the operator the design intent of each profile part. This is usually done via a profile plot. Many modern shipbuilding software packages support the creation of these drawings automatically from the 3D model; however, there is additional management of creating and managing these files.
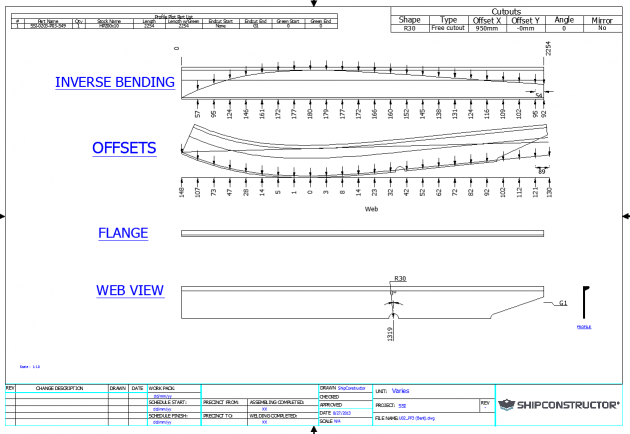
Even though these production documents are created automatically there is usually some manual manipulation required for them to adhere to a yard’s standards. In the concurrent environment most organizations are using, there is a requirement that these drawings to be updated several times before they are released to the shop floor. Most of the time these updates are minor but for more non typical cases more effort is required. All this creation and updating takes time for the engineering team to provide documentation which has all the information the operator requires to prepare the profile part. Then there is all the logistics of printing out the documentation, making sure the profile operator has the documentation when it is ready to be cut as well as the very costly workflow when a change happens after the production package has been sent out. All these steps and many more are required to support a manual CNC profiling station.
Once it is time for the operator to cut the profile they will need to find the documentation which represents the profile (hopefully it is the latest version ? ), translate the information provided (hopefully all the information is available and understood properly), and then execute the cut. It is not uncommon at this stage that the operator has to contact engineering to clarify the profile characteristics, or in some cases make a guesstimate of what the design intent was. Either of these situations can have significant costs to the project.
The automated workflow eliminates virtually all the preparation of the production documents which is a significant amount of time and effort. In turn, it will need a level of integration between your 3D CAD/CAM tool and the CNC machine. With all the information required by a CNC profile machine contained in your 3D product data model, the exchange of information requires virtually no user intervention. When a production package is generated, so are the files which are read by the CNC profiling machine.
Depending on the software application you are using for your 3D environment, you may not have the luxury of having it supporting your CNC profile machines. This is why there are more yards using the manual process instead of the automated process. The only way to support the automated workflow, if your software application does not support this type of integration, is to invest in some custom development. This does scare some people as “custom development” is an unsettling phrase because this usually results in expensive and limiting results. There is some truth in this feeling; however, if managed properly it can improve productivity to the entire yard which will outweigh its investment.
Closing Remarks
Using a manual process to cut, bend and mark profiles is less efficient during the production phase but more importantly it has a higher ongoing cost. This ongoing cost is from creating, updating and managing documentation needed to support the manual process. It also introduces more opportunities for human errors which are introduced during the defining, adding and translating of this information.
Modern 3D CAD/CAM solutions contain 3D information to design and build a ship but it also encompasses a vast amount of information to manufacture the model. Leveraging the information captured within the 3D environment to integrate and automate manufacturing machinery can improve the productivity of the yard. Having an automated process to get information from your 3D product model to your production machines is more efficient not only because it streamlines the process but also because it actually removes all the tasks which are needed to support the manual process.
With the need for every company to become learner, automating processes which eliminate manual and error prone activities are a perfect way to invest in improving your overall productivity.