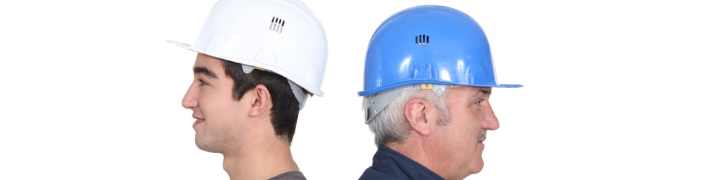
My recent trip to several yards and design agencies reinforced something that I have noticed lately. I am continuing to see a theme of challenges within our industry. Even in different segments of our industry, the challenge of finding and retaining skillful personnel continue to grow as one of the main concerns. There is a lack of skillful personnel currently and there will soon be an even greater shortage of experts shortly due to the high number of soon to be retirees in almost every type of job from the deck plate all the way to management.
This concern is echoed in Lloyds Register’s latest Survey: “Survey shows skills and knowledge shortage as critical change issue.” The survey states: “36% of respondents consider Skills / knowledge shortage to be the primary issue. “
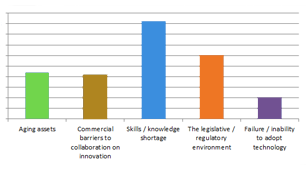
The question I ask myself and others is, “How does one go about preparing themselves for this type of future?”
I have received some very interesting answers such as, “We will deal with it when we have to” and “We will just pay them more money.” I do not think that either of these types of thinking is a viable solution and am always a bit perplexed when I hear these type of responses. I have also heard many organizations investing in educating new potential experts as well as attempting to capture some of the knowledge these experts have in process. I think some of these activities are what should be done but I think there is something that is missing in some of these strategies. The nut of my concern is, “Are we planning for a future where we require the same type of expert? Is this what we should be doing?”
My Thoughts for Preparing for the Future
Planning for the future is a very difficult thing as we all know but I always like to start with the quote from Wayne Gretzky (famous Canadian Hockey player)
A good hockey player plays where the puck is. A great hockey player plays where the puck is going to be.
When looking at the future I think it is important to not get hung up with where our industry is today. Tomorrow (the future) is different and we need to at least look at the trends to anticipate the landscape of tomorrow.
In my view there are three main drivers which will help solve the issue of our ageing workforce and they are:
- New generation of workers have different skill sets.
- Democratization of software.
- Increased amount of connections between systems.
New Generation of Workers have Different Skill Sets
It is no secret that the new generation of the workforce has a different skill set than our current experts. I truly think that this is an opportunity as the experts we need in the future will be different than what we have today. Their ability to use technology is an obvious benefit especially since every single company is relying more and more on technology. Future workers will be a huge asset because they will embrace technology advancements with very little convincing or training. How much time does it take to introduce a new system into your organization today? How much push back do you get from the current experts and the soon to be experts? What is the additional cost of this resistance?
The required skillset for a company that wants to be technologically advanced is different from a company that wants to stay with the traditional methods and the new generation are better aligned with where you are already taking your company.
Democratization of Software
The software solution you are using today allows you to change the way you are doing things to be able to build a better quality product for less money. You are able to calculate the weight of your project as your project progresses, simulate you build sequence to ensure that you will not encounter issues on the shop floor, purchase items just in time to reduce handling and storage, simulate project workflow through the yard that meets facility constraints, ensure safe lifting and turning of blocks and much, much more.
Many of these items which can now be done with software were done by a different type of expert. With more powerful tools available the skillset and the type of expert required is again different. I touch on this slightly in my previous post: Benefits of a Digitally Captured Build Sequence
Connecting Systems
Software continues to get more powerful as mentioned above but the real change you will see and for what most have already seen is the connection between systems. This can be the connection between your CAD system and a PLM / PDM / ERP / MES system or an area that I think will affect the type of experts we need more is the connection between your 3D Product Model to your hardware.
I have seen an increase in the number of integrations with ShipConstructor to CNC profile cutting & bending machines, panel lines and many other types of machines. With the shop floor machines being fully or semi-automated by the 3D Product Model the type of experts you need on the shop floor will change.
Closing Remarks
I am not sure what the future will hold, but I am certain the constraints which guides our decisions today will be different in the future. When looking in the future we need to at least attempt to see how these constraints will evolve.
When trying to determine how we are planning to fill the gap that will be created with our aging experts we need to understand that our experts of tomorrow will require a different skill set.
The skills of the new generation, the software capabilities of the tools we use and the trend of connecting all our systems together can transform the risk of losing our current experts to an opportunity. This is assuming that we can successfully embrace the new landscape of our industry.