Conversations on Improvement
My last blog post covered how engineering can improve by assessing key metrics and making better data-based decisions. However, more elements are in play when a shipyard wants to improve project efficiency and optimize costs.
I’d like to elaborate on that, inspired by a conversation I had in the comment section of my previous post. I have found it very insightful and worth exploring further.
Knowledge Transfer
Industry-leading shipyards are good at retaining core competencies in-house and leveraging employees’ collective knowledge and expertise. That can help improve operational efficiency and make shipyards agile even in tough competition.
Challenges in shipbuilding with an aging workforce put shipyards in situations where competence gets lost over time. For instance, Japan and Korea experience a shortage of workforce due to jobs in shipyards being less attractive for a younger generation while seasoned experts retire. Focusing on passing core competencies over to future hires and making knowledge more accessible for all employees is an undisputable measure for shipyards that want to keep a leading edge in the industry.
Lessons Learned
Lessons Learned is a common and well-known approach to improving shipbuilding projects and reducing costs caused by errors during design and construction. Unfortunately, shipyards often don’t utilize it properly for knowledge capture and strengthening core competencies in-house. They repeat the same mistakes throughout several projects until it finally gets captured.
The Same Hurdles
As an engineer, I have worked in large (with remote shopfloors), mid-size (on-site shopfloors), and very small (fewer than ten employees) engineering companies. In all of them, we used Lessons Learned to some extent, but it’s not always been efficient and successful. Many engineers (and I was one) are skeptical of this approach and say that Lessons Learned don’t help pass knowledge from production to design and improve shipbuilding projects.
Improvement Basis
However, the problem is not that the Lessons Learned approach doesn’t work. That’s just a tool. The problem is the lack of clear goals, good leadership, and the inability to communicate based on facts instead of assumptions.
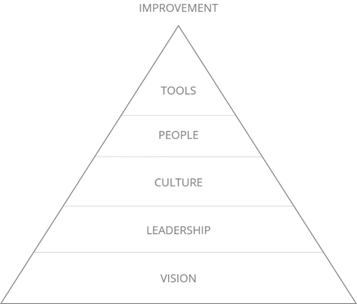
Based on my experience and what I have learned about leadership and innovation, I see a tool or technology as just a tiny piece of a holistic approach, a tool in the toolbox, if you will. Any technology implementation will always rest on good communication, a culture of trust, ownership, responsibility, and people who make use of it:
- Clear Goals
Knowing goals for creating a knowledge base in a shipyard is as much important as using the knowledge base itself. It doesn’t make sense to collect Lessons Learned entries if they are not applied diligently in future projects.
- Communication
One doesn’t need to have a leading role to excel in leadership. That concerns everyone from an entry-level designer to a highly skilled seasoned supervisor to top decision-makers. Leadership is about how we communicate and how we collaborate with our teammates.
- Culture of Trust
Disconnection and sometimes confrontation between design and production teams leads to mistrust and jeopardizing shipyard initiatives. Focusing efforts on building a culture of trust and good relationships between disciplines will decrease friction in sharing critical information and implementing solutions for a digital shipyard.
- Expertise
When a shipyard invests in people, it inevitably grows its core expertise. Proactively nurturing soft and hard skills, giving good challenges, and helping employees grow professionally play a significant role in retaining competence in-house.
- Technology Solutions
A well-implemented PLM system is an excellent way to capture lessons learned and project knowledge. In that way, shipyard teams can collaborate, learn from past projects, share information, and re-use it for product and process innovation.
Shipbuilding-specific CAD tools are also perfect for incorporating intelligence into the product model and making it easily accessible to relevant disciplines or teams.
Immediate Action
Unsurprisingly, I had the best communication experience and the most efficient project execution in a small-size company. Our team was 5-6 people. But the lessons and working principles I learned in a small and dynamic organization also apply to larger companies.
Below is a simple six-step workflow for capturing Lessons Learned we used to go through and to ensure nothing was left behind before the next project started.
- Identify design or production issues. Give a comprehensive description of a problem.
- Rate by priority level to resolve it (e.g., low, medium, high).
- Define and list specific actions to take. Clearly define due dates.
- Allocate workforce based on Step 2 and Step 3.
- Capture a new design in the product model and document it well.
- Review the documented issues before similar projects start.
It’s often neglected, but visiting other disciplines (production, procurement) for immediate feedback and talking to the floor workers directly and frequently brings a lot of value to the entire team. Do it regularly to capture possible issues (and knowledge) in the early stages and optimize the deliverables of the projects.
Holistic Approach
More data does not equal more beneficial information unless the shipyard implements clever means of managing it, practicing good leadership, and creating a healthy culture to improve operational efficiency.
Involving specialists and leads from different levels in the project reviews and optimization activities will help imprint the gained learning, form solid collective competencies to apply in future projects, and make the shipyard’s core business more profitable.
The topic is more extensive than a brief blog post, unfortunately. But we certainly can continue the conversation in the comments.
Share your insights on how shipyards solidify their competence or good practices implemented in your yard to grow and get efficient. How do you practice lessons learned? What are your experiences?