In shipbuilding, a wealth of engineering information is created well before detail design begins. In some cases, even before the build contract is awarded. This early engineering information (regardless of source) must be captured, reused, and carefully managed.
The information collectively forms the framework of the production model, reduces rework, validates the design and mitigates the risk of errors as the design matures.
At the same time, many shipbuilders hold on to a misconception that to manage information effectively, they need one engineering solution that does it all. The pitfall is that such solutions can offer a few basic capabilities, but they cannot meet the very specific requirements of a shipyard and cannot be configured fully to align with the workflows in the office and on the shopfloor. Let’s explore a few alternatives of efficient information management through all the engineering stages.
Managing shipbuilding projects is challenging
Shipbuilding programs are of a massive scale and complex, some lasting decades. It often involves multiple organizations collaborating on the design and a global supply chain. It is typical to have each step in the whole ship design-build project treated independently by different groups, with each group using specialist modeling and simulation tools as appropriate. The result is that others may not efficiently utilize the information generated in each process. At worst, the information cannot be reused in similar projects which generates unnecessary work instead of reducing it and optimizing it.
Initial Design
During initial design, the overall architecture of the vessel and main systems are designed.
Making sure the design and engineering package integrates with the industry-leading naval architecture design packages like NAPA, Maxsurf, Paramarine, Rhino will provide a good starting point in capturing the design information and distributing it further between the teams.
This also allows for immediate surface design validation, ensuring that they are producible and production-ready. Information about features like weld seams, marklines, bevels, penetrations, plate expansions for nesting and forming should be created at this stage. This makes the project proceed rapidly and avoiding major errors downstream.
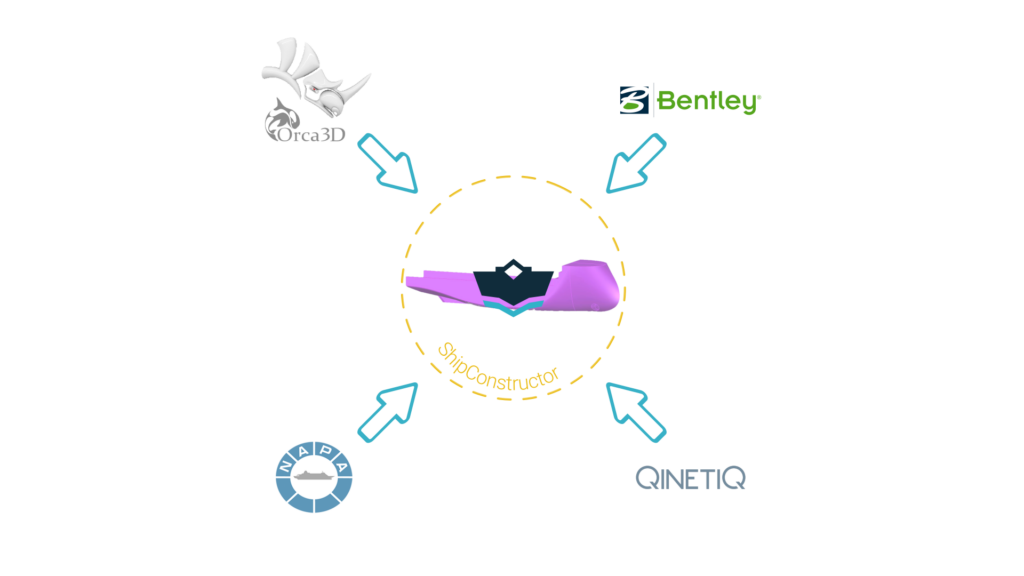
General arrangements and other 2D documentation are easily referenceable as underlays when modeling.
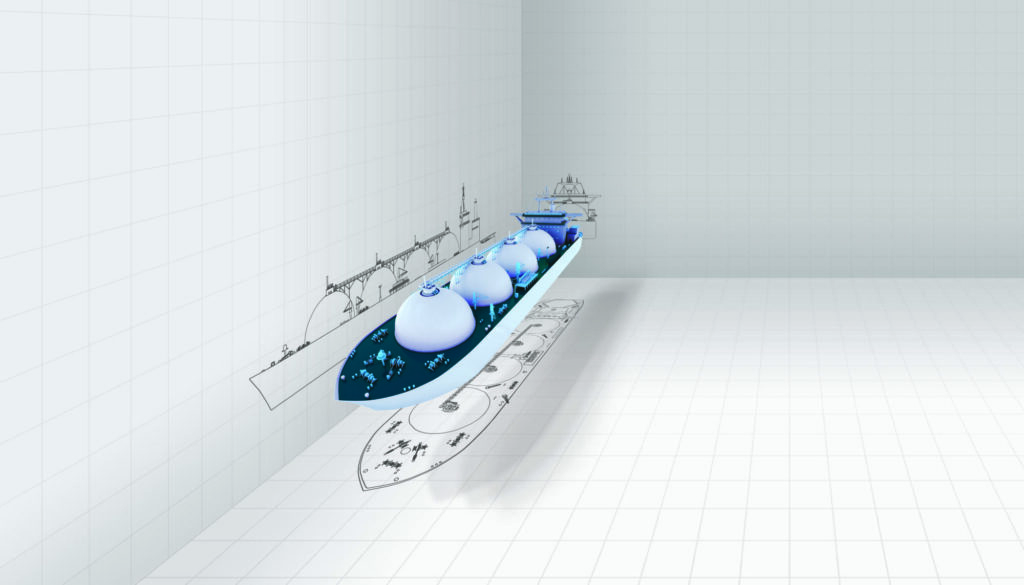
Basic Design
Like for initial design, the industry has several well-known tools for rapidly defining the ship’s basic structural design, including ExpressMarine, Seanaptic, NAPA Steel or directly in ShipConstructor. The basic design models are created for classification societies for review.
These models lack the required detail to support construction and generate MI (Manufacturing Information). In many cases, the model must be recreated in detail design software which entails much rework. The SSI Solution uses Open APIs (Application Programming Interface) and a deep partner ecosystem. In situations where the basic design was not started in ShipConstructor this makes it possible to begin detail design where basic design has left off.
The basic design model can be converted to intelligent, production-ready parts. From here, production details such as end cuts, bevels and weld reliefs can be added.
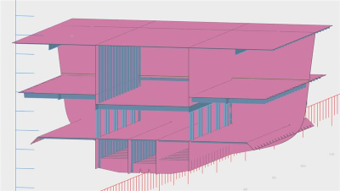
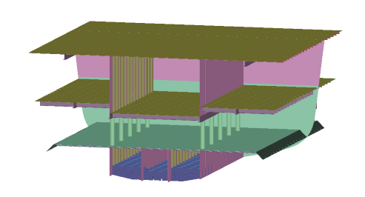
Functional Design
Although functional design often is defined under the basic design stage, it’s an integral and a quite important part of the project, ensuring all systems communicate and connect well. Using engineering solutions that integrate with functional design and provide capabilities for automated design validation reduces time spent on detail design further down the line.
During the functional design phase, systems are designed in P&IDs (Process and Instrumentation Diagrams) and Master Equipment Lists (MEL) created. This information is captured within the engineering environment and used to place equipment in the model without designers needing to filter through catalogues to find the correct part.
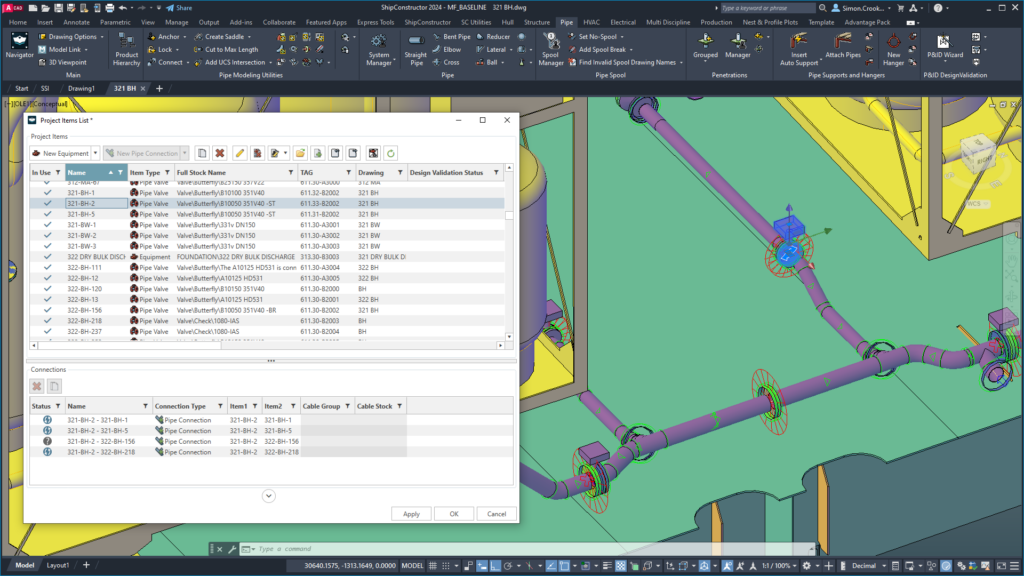
Using a PLM system for informed decision-making
The amount of data involved in designing and building ships is huge. The multiplicity of tools used during distinct phases of ship design makes the data handling and sharing between departments, phases, and partners a challenging task. A PLM system allows a shipyard or a ship design organization to deal with these tasks in an efficient way. This is achieved through different capabilities a PLM system provides, like requirements capture and management, product decomposition (definition of ship work breakdown structures), a centralized environment for storing and managing design and analysis/simulation data under revision control generated by CAD and CAE (Computer Aided Engineering) tools used during initial, basic & detail design, managing all project drawings & documents and bill of materials (BOMs), and project management.
The PLM system can also be harnessed to gain knowledge about why different solutions were chosen in previous projects, how projects evolved, which are the good reference projects for reuse, and find the required information & documentation more easily.
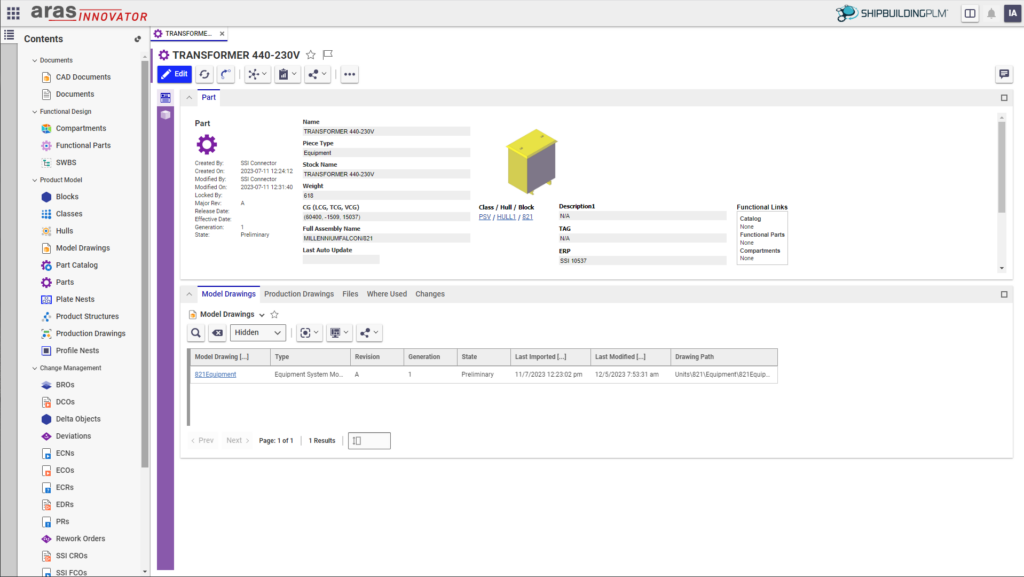
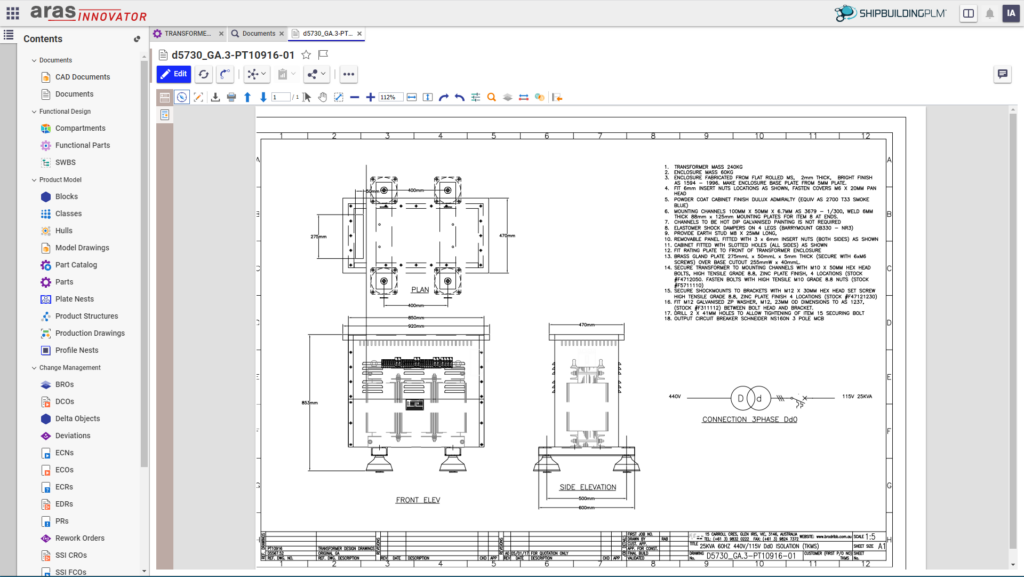
A PLM system allows all information from all design phases of the project to be centrally stored and managed, allowing for improved integration and collaboration between offices or teams responsible for different tasks in the design process.
Benefits of design reuse
Design Framework
The early-stage engineering forms the framework for detail design to begin. Catalogs are defined, the primary work breakdown structure (PWBS) is outlined, and requirements are linked back to system models. The initial design model geometry is used to define structural sections.
Reduced rework
By capturing the critical engineering information available from the early design stages, regardless of source, detail design is rapidly accelerated.
Design Validation
The functional design information is validated as it is placed on the vessel product model. SSI’s Open Shipbuilding Platform captures the design intent from intelligent P&IDs allowing system assets to be intelligently selected and placed on the model while connections are validated, and pipe runs auto-routed in between.
Conclusion
Capturing the available early-stage engineering data and geometry within the detail design environment is critical for accelerating detail design. Projects are a collaboration between multiple stakeholders including clients, designers, builders, and suppliers. The information needs to be leveraged moving forward regardless of source. SSI’s Open Shipbuilding Platform comprising of ShipConstructor and ShipbuildingPLM (SSI’s shipbuilding industry-specific PLM system) captures the relevant early-engineering information into a single source, the detail design model, where it is leveraged in the engineering environment.
Managing the information in ShipbuildingPLM enhances the engineering environment further by storing revision histories, lifecycle statuses, and relationships between all project artifacts, creating a digital thread throughout the project.
Further Reading
Reusing Initial Design Data for Basic Design – Solution Story | SSI | ShipConstructor
Generating Class Approval Drawings – Solution Story
Placing Major Equipment – Solution Story
3D Class Approval