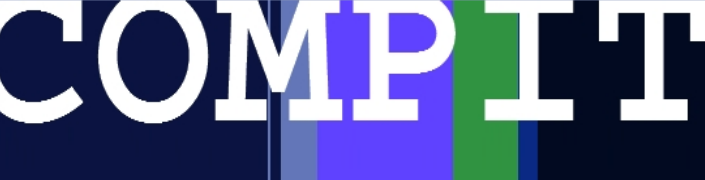
I just returned from my 5th attendance at COMPIT (Conference on Computer Applications and Information Technology in the Maritime Industries). If you are not familiar with COMPIT you can visit the COMPIT site and you can refer to my previous post COMPIT 2014 Post-Mortem.
This year many of the topics and challenges discussed were similar to previous years but there definitely seems to be a bit more concentration on exchanging information and team collaboration. Here are some of the topics I found interesting.
CAE to be Integrated with Design
The conference started with several presentations about exchanging or interfacing CAE applications or tasks with CAD applications or design tasks. The challenges in our industry are no different than what other industries are facing…surprise, surprise. The times of doing all the hydrostatics, hydrodynamics, stability, performance calculations, etc. in a silo are long gone. To optimize the design, construction, cost and even time to create a good model requires continuous feedback between many disciplines. (This was also noted in the paper SSI’s Darren Larkins, Mark Waldie and myself wrote for the conference.)
One of the strategies mentioned from Altair was similar to much of the discussion at COFES 2015. This slide is very similar to the many of the slides I saw at COFES:
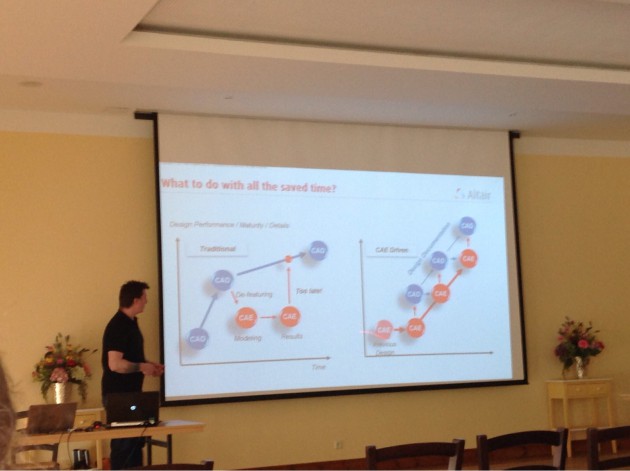
The challenge that this process is trying to solve is to validate the design as more detailed information becomes available. This does create new challenges which is sometimes overlooked but I do think these challenges are relatively “easy” to overcome and the overall benefit is worth the additional challenges. The three main challenges are:
- The CAE/FE model requires a different set of information not always available in the CAD model. This will require “linking” of entities and not just exchanging.
- The two models require different geometric representations. FE models usually work with surfaces without requiring details (holes, cutouts, corner treatments, bevels, etc.)
- CAE tools require speciality skills which are not found in most designers using CAD. I do not think that the CAD designers will do all CAE but they can do some basic CAE to eliminate really bad designs early. The final verification will most likely always be done with someone who can set up the scenarios accurately and interpret the results correctly.
Model Based Enterprise
On a related theme, one of my favorite presentations was by Darren Larkins who talked about the holistic view of your digital project. This is where he demonstrated using DWFx as a Model Based Definition in a Model Based Enterprise. If you are not familiar with MBD / MBE you can refer to my blog Model-Based Enterprise Summit 2014.
The general idea is to generate a technical data package which contains all the information required to describe an object (part, assembly, spool, etc.)
Connect Systems Via Peer-To-Peer Strategy
A virtual Single Ship-Design System Composed of Multiple Independent Components presented by Herbert Koelman was an interesting presentation. It focused on connecting three products together. The key point in his presentations was that when we have attempted to use a “Neutral Model” (central data storage) or neutral file formats (STEP, IGES, DXF, etc.) to try to exchange information between systems, we have failed.
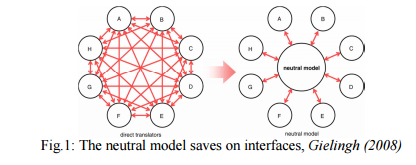
The problem was explained that in reality there is never one single central repository of data but rather many sub-systems. These sub-systems need to act as peers with other connecting sub-systems. This would require that each set of sub-systems need to create their own distinct communication framework.
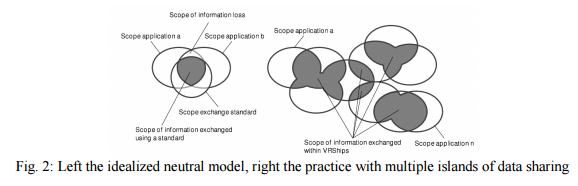
The presentation and his paper are full of references to papers and statistics which I enjoyed learning. For example:
According to the survey of Srinivasan (2008) the most frequent used data exchange standards appear to be DXF, IGES, STEP, with a combined utilization of 60%.
If I recall correctly DXF was the most common which I would not have guessed.
PLM
There were, as always, several presentations on PLM and exchanging information between systems. There was some interesting information but for the most part it was solving the same challenges of exchanging information between systems which were not designed to share information or at least not as a first class citizen feature.
Rethinking Weld Management
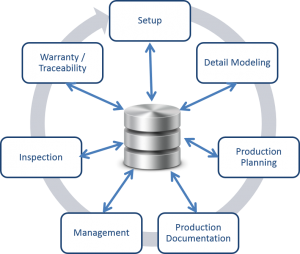
The presentation from Nick Danese about Rethinking Weld Management was interesting since it was co-authored by myself. I think the biggest take-away, as with most of SSI’s presentations, is that a true open architecture not only allows you access to your information, it makes it available.
From the Weld Management perspective this means:
- You will not have to change your processes, user skill set, or tools. Many of the tasks you are doing around weld such as inspection, reports, weld schedule, etc. use Excel. With SSI’s WeldManagement product, you can still use Excel the exact same way but now you can have the information be automatically linked to the Marine Information Model (MIM).
- You can reuse information and ensure you have the most up-to-date data when making your decisions. If the weld schedule changes it will be reflected in all stages of the model. If the inspection of the weld fails that will be reflected in the model for traceability as well as to define a new weld for the portion which failed. The list goes on.
- Most importantly, it allows you to have new ways to communicate much more efficiently and effectively. A good illustration is the example of a weld report to determine failed welds.
Closing Remarks
COMPIT is one of the very few shipbuilding technology conferences. It is definitely the conference that is known for their very remote location with very poor internet :).
There is always interesting new topics presented as well as many of the topics which are reoccurring every year. It is almost guaranteed that I will learn something new as well as get new ways to think about an old stubborn problem.
The best part of any conference is the networking and the conversations with some very smart people. It was even good to have a couple drinks and some great dialogue with SSI’s competitors.
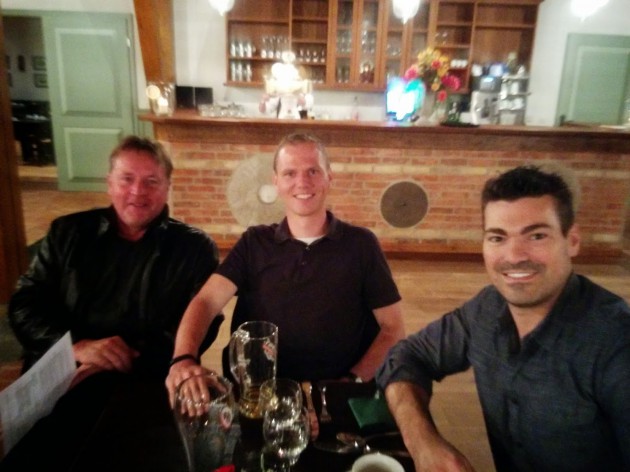