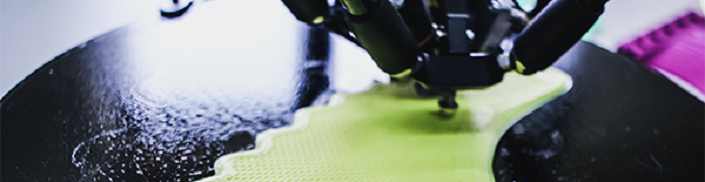
3D printing, the most common form of additive manufacturing, has become a ‘buzz’ technology in every sector connected to manufacturing and engineering, and it’s no different in shipbuilding. However, the excitement is not for nothing. Five years ago, 3D printing was being used for the restoration of wooden ships, rapidly prototyping proofs of concept, and creating scale 3D models. Now, we’re seeing additively manufactured parts installed on ships, further enhancements to the rapid prototyping capabilities of 3D printing, 3D printers installed onboard ships and within shipyards on a more significant scale, and sea-faring 3D printed boats. While all this progress is exciting, and the future looks bright for additive manufacturing, some serious hurdles remain before 3D printers are commonplace at every shipyard and onboard every vessel.
Rapid prototyping
One of the biggest advantages additive manufacturing has over more traditional techniques is speed. Shortening the timeline between initial concept, 3D model, and manufactured parts. While 3D CAD technology has removed the need to physically manufacture parts at each step of the process, sometimes the most effective way to understand a design, or visualize inconsistencies is to see the object in 3D space.
By quickly printing the design that already exists as a 3D model in minutes or hours, instead of sending it to be machined in several days (at best), it becomes possible to iterate on a significantly larger scale. At Norfolk Naval Shipyards (NNSY), the rapid prototyping capabilities of 3D printing are being used to service the Gerald R. Ford class of aircraft carriers.
“Rather than making something out of metal, which would probably take two to three months just to see fit-up purposes, we print out a 3D part and we can put it on a mockup,” said Bill Harrell, NNSY rapid prototype program lead, “It’s really rapid prototyping or proving a concept for actual use, which can save time, material money and labor.”
3D printing can be a particularly useful tool if used in conjunction with a 3D CAD model that’s created early in a ship’s design process. A 3D printed, exact model of a vessel can be used for more than just show and tell. It’s the perfect solution for hydrostatic or other testing in a pool or other real-world environment as a complement to computer-aided analysis.
Additive manufacturing
Beyond prototyping, additive manufacturing is now being used to produce finished parts that are certified for and installed on US Navy ships and workboats – further reducing the gap between concept and final product.
At Huntington Ingalls Industries’ (HII’s) Newport News Shipbuilding division, additively manufactured hardware is being used on US Navy warships for the first time. The prototype piping assembly that is being installed on the aircraft carrier USS Harry S. Truman in early 2019 will be tested on board for one year, before being removed for assessment. The US Navy’s dedication to 3D printing also goes beyond its implementation on vessels, the US Naval Air System Command (NAVAIR) has also invested heavily into 3D printing in 2018, increasing the number of approved 3D printed parts for its fleet by about 5 times to 1,000.
Maintenance considerations
Apart from being an effective tool at a shipyard for prototyping, and to a lesser extent manufacturing, 3D printers are becoming a solution for replacement parts right on board a ship. The flexibility of having access to any particular part on-demand, especially if that part could be retrieved from an existing As-Built 3D CAD model of an entire ship, is extraordinary.
Most notably, the US Navy is experimenting with this kind of system aboard the USS Essex. While early efforts aboard that ship have been limited to producing plastic medical supplies, oil tank caps, and similar parts, it does represent a leap forward in the traditional thinking surrounding 3D printing within shipbuilding.
On a smaller scale, French sailors have used a 3D printer aboard their sailboat to successfully print and deploy plastic components during their six-month long, 10000km, sail around the Mediterranean Sea and North Atlantic. Despite the small scale, their success shows the unique possibilities that an onboard 3D printer or additive manufacturing machine can provide to a vessel.
Software’s Role
Part of the key behind the adoption of 3D printing within shipbuilding lies in the transfer of data. The time savings of 3D printing can evaporate if you’re forced to redesign parts from scratch or ‘phone home’ to have them manipulated off-ship.
Having an existing 3D CAD model of your ship and its components and being able to quickly export those components into a 3D printing friendly format, like STL, reduces downtime and plays directly to the efficiency strengths of additive manufacturing. This is especially true if the part you are printing requires additional manipulation, being able to quickly revise, re-export, and reprint onboard and within a single ecosystem is crucial.
Looking Forward
Despite the technical challenges that remain, particularly the unique problems associated with 3D printing at a useful scale on a moving vessel. It’s clear that the industry sees the potential efficiency gains that can be had. Within the next 5 years, it’s likely we’ll see a substantial increase in the number of 3D printed parts in use aboard real vessels.
But if the first hurdle hindering additive manufacturing in shipbuilding is the inherent technology itself, then the next will be widespread adoption. Currently, while components are being installed and tested on ships, it’s at a small, ad-hoc scale. However, the first key component to the mass implementation of additively manufactured components is already in place – certification. The ability to objectively and quickly assess the quality of a process can be the difference between implementing a new technology or sticking with the tried and true. Companies like DNV GL are already certifying additive manufacturing processes and products and more are sure to follow.