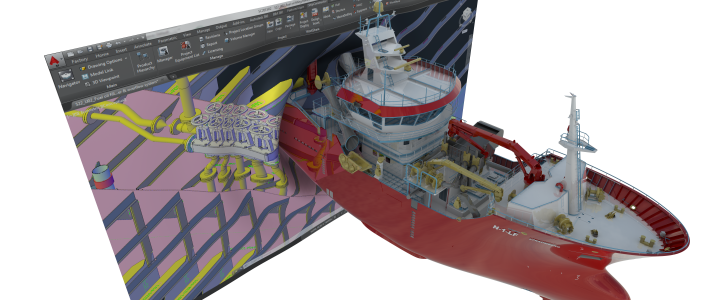
In my previous blog posts I discussed factors that are forcing us to change virtually all aspects of how we build marine structures. These include challenges related to how we decide what to build and how we determine functions and requirements. Another factor is an increased desire to integrate the customer into the design process more tightly. The next step is to see how we will take those initial concepts and designs and translate them into detail designs for procuring materials, optimizing logistics of the yard and physically building ships and rigs.
During the basic and detail design phase there are so many people involved in different roles, each of whom are responsible for a specific aspect of the ship. A very small set of examples are: production planners, purchasing & procurement, weight engineers, multiple different types of simulation experts, suppliers, 3D CAD modelers & designers for various different systems, lifting & turning engineers, customers, classification societies, multiple different types of facility operations and logistics roles, etc. All of these and hundreds more require information from many different departments and stakeholders. The question I will try to answer is, “How will the future change how these people do their jobs?”
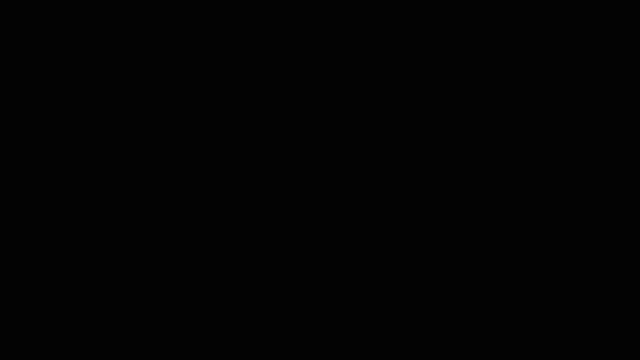
Digital Shipbuilding
Get a first-hand experience of what the design, build, and maintenance phases are like in an increasingly digital shipyard.
Experience nowMoving from Static Processes & Architecture to a Dynamic one
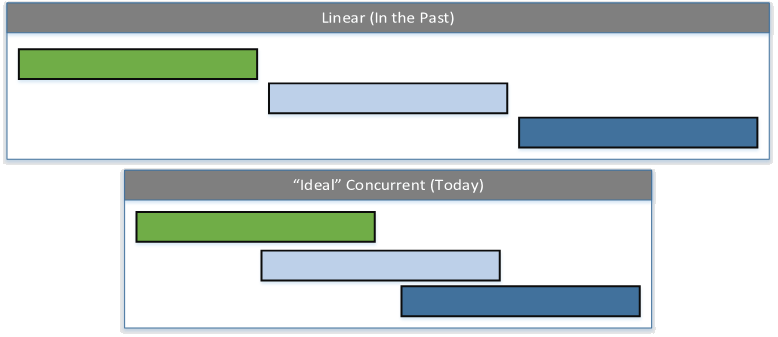
One of the trends of the last decade was “Concurrency.” We all know there are thousands of activities that have to happen to build a marine structure and to execute them in parallel instead of linearly is better. Concurrency obviously reduces the duration (time from start to end) of building the structure but technically does not reduce the total amount of hours. This is largely because of that fact that it introduces new challenges, which require a different process, tools and most importantly, a new culture. Having said that, I do think most of the people in our industry practicing a more concurrent workflow are overcoming the initial challenges and are building their product in less hours.
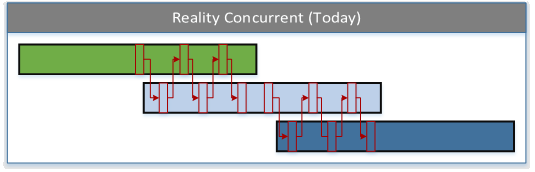
However, if we really look at how today’s concurrent workflows actually function, we will see that they are made up of many discrete static chunks; one set of tasks are completed by a person or team then moved to another. That is one reason I believe we have not really resolved the challenge of department silos. Departments are producing smaller deliverables, which reduces the time it takes to pass on information to another department; however, they are still working in their own bubbles with the information contained in their own systems.
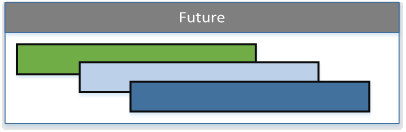
In the future of shipbuilding we will be taking the next leap, moving from this concurrent static workflow to a concurrent dynamic workflow. This will result in information being available with significantly higher frequency, allowing better decisions based on true up-to-date information.
The transition to the concurrent dynamic workflow providing very high frequency information will have the same challenges as when we moved from a purely linear workflow to a static concurrent workflow. The future will require existing systems and potentially new systems and tools to allow information to be provided instantaneously to any other system or stakeholder that requires the information it contains in a context they can use. It will also require a method that allows the identification of the maturity of the information since we will need to distinguish if the information is in the preliminary phase or the completed phase and all stages in-between.
Transparent Connections to Systems and People
The higher frequency data which will be our environment in the future will be driven by the trend we are seeing today of connecting our systems as well as the changes organizations are making to improve communication between teams. However, the way you connect a static concurrent environment and a dynamic one is completely different. It is similar to the difference in turning on the TV to the weather channel and then waiting until today’s temperature is displayed vs. looking at your smart watch and seeing the information on the home screen. One is much more dynamic and instant than the other.
The integration of these systems will transfer data between one system to another as most integrations today but will handle a more “live” mode. In addition, these systems will also be able to initiate actions from one system that will be executed in another system. The connections between systems will be much more sophisticated yet will not seem complex to end users. This is due to the trends in software development which I will not focus on in the post.
We will see many more systems and people who are only connected via some convoluted manual process to be connected by a seamless and effortless connection. An example is the “interesting” ways some companies have their different discipline modelers exchange information today. If the company uses external subcontractors for electrical or HVAC it can even get more convoluted. The serial and manual generation of data with low fidelity between teams will be long gone. Information from each required discipline will be available with the need to generate the information.
There will be completely new Artificial Intelligence (AI) and Big Data systems that will be connected to various aspects of our business. This can be an AI system that will take in all factors to determine cost and even risk of manufacturing. These factors will include the ones we take into consideration today such as labor, materials, etc. but also many more that we do not currently take into account.
New Factors to be analyzed in the future:
- Empirical probability of days we cannot work due to weather (looking at short/medium/long term predictions)
- Amount of sick days employees take during the week a block is being built
- Current cost/resources of lifting and turning using previous shipyard data
- Cost/resources of moving assets around the yard
- Risk of supplier delays during specific seasons
- Many, many more factors
The key to analyzing these factors is the connection of systems within a dynamic concurrent environment. To make that work, there must be user transparency. This means that the connections between the systems are hidden away from the user. The end user does not need to prepare any information to be sent nor follow some sort of manual recipe (series of ordered steps that if not followed will not give you desired results). The proper information will be transferred to the correct stakeholders and systems in the correct context/format like magic. Without user transparency of all these connections, dynamic concurrent environments would simply not exist.
The presence of these connections will allow much more opportunity as to how/when we get information.
Next Blog Post
In the next blog post I will continue discussing how users will no longer need to context switch (switch between many applications) to request information as well as initiate an action in several connected systems. I will also explain why we will finally have an 3D As-Built model.
Blog Posts in the Future of Shipbuilding Series
- Future of Shipbuilding (15+ years)
- Future of Shipbuilding: Engineering Design
- Future of Shipbuilding: Detail Design and Production Planning (Part 1)
- Future of Shipbuilding: Detail Design and Production Planning (Part 2)
- Future of Shipbuilding: Manufacturing (Part 1)
- Future of Shipbuilding: Manufacturing (Part 2)
- Future of Shipbuilding: The Journey Forward