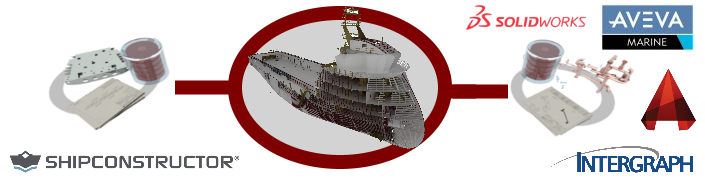
In this blog series I am going take you through a strategy to successfully work with a distributed team that use disparate CAD/CAM authoring tools. I discussed the challenges in working in this type of environment in my previous post.
Even though this blog series focuses on the scenario of having a non-collocated team using different tools, it can also be implemented successfully when the teams are using the same authoring tools. I focus on the former because of the additional challenges they introduce in managing the project.
Use Case
Organization structure
There are two companies with each responsible for a particular portion of the project. The companies are separate entities with absolutely no affiliation. They have their own processes, standards, workflows, culture and tools.
Authoring tools
The authoring tools they use are different. One team uses ShipConstructor (yes I know, it was obviousJ) and the other uses AVEVA PDMS (at least I picked one of our competitorsJ). I should note that in no way is the workflow I am going to demonstrate constrained only by those tools. The combination of tools which can use the strategies outlined in this blog series are vast.
Project responsibilities
As stated above, each company is responsible for their own portion of the project. I will use a common strategy used in the marine industry with one company responsible for the hull and structure (shell and skeleton) and the other company responsible for the mechanical systems such as pipe, HVAC, electrical, etc.
Overview of the strategy and tools
The selection of tools is very important in order to make this a very robust solution that will allow you to work with various CAD/CAM authoring tools. In this case, I have decided to use Autodesk BIM 360 Glue as the main hub of the rich 3D product model.
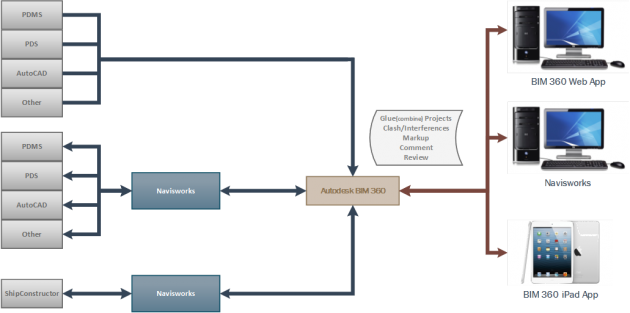
There are five reasons why I selected Autodesk BIM 360 Glue as the hub:
- It accepts many formats (more than 50) from the popular CAD tools.
- It can merge or Glue models created from different tools into one model without losing any fidelity.
- It offers a Web App as well as an iPad App that allows stakeholders to view and interact with the model. This is especially important as many of the stakeholders do not have or do not want to have the heavy CAD/CAM application installed to view the model
- Has great integration with Navisworks
- And finally to be honest, it is what I am most familiar with. To be fair I have looked into many others; I just have not seen any which have the same feature set as Autodesk BIM 360 Glue
Each company will only be required to upload their portion of the project model to Autodesk BIM 360 Glue. Yes this means there is no need to send the model via email, Dropbox or ftp. If either company wants to get the latest version of the model from the other company they can do so without requesting the latest information. They can simply download their counterpart’s product model from BIM 360 Glue or view the model in the BIM 360 Glue Web or iPad App.
BIM 360 Glue supports activity base permissions for each user. These permission can control who can:
- Upload and modify the models
- View the model
- Administer the project
I also use Autodesk Naviswork as a key part of the workflow. Navisworks is the best visualization tool I have used and I have been using it for a very long time, even before Autodesk acquired it. Navisworks supports more file types from CAD to laser scanning than any other visualization tool I have encountered.
I use Navisworks as the bridge between the authoring tool to BIM 360 Glue. There are additional benefits we will get from using this strategy that will be apparent in the following posts. It is not a necessity to use Navisworks as an intermediate step; however, I would recommend it.
Next posts
Part II: Create, update and manage the combined product model.
Part IV: Communicate and collaborate synchronously and asynchronously with all team members
Part V: Detect and manage clashes and interferences in combined model.